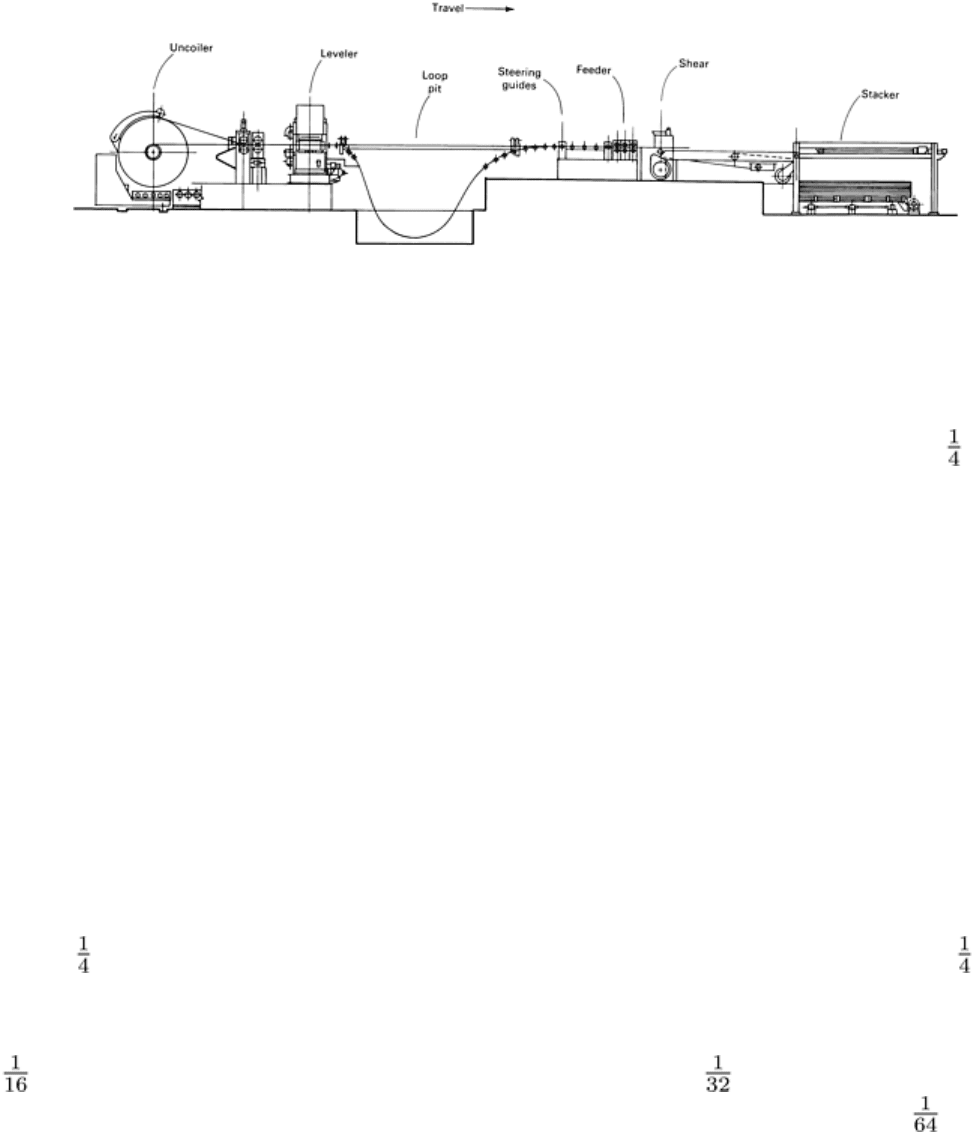
the gage stop retracts, and the cut sheet is delivered to the stacker. As the cut sheet is removed, it trips a limit switch that
resets the gage stop. Then, the shear opens, permitting the strip to slide out of its loop through the shear and onto the gage
table against the gage stop again, and the cycle is ready to be repeated.
Looping Pit. As shown in Fig. 10, many stationary shear lines have precision measuring feeder rolls just before the
shear, instead of hump and gage tables. In these lines, there is a looping pit below the passline, after the
straightener/leveler and before the feed rolls and shear. The flattener and/or leveler runs continuously, with coil stock
accumulating in the pit during the cut cycle. Side guides control the feed angle of the strip for maximum cut squareness as
it exits the looping pit and enters the shear. On some lines, the shear knives can be pivoted to cut trapezoidal blanks.
Fig. 10 Stationary shear lines with looping pit located below passline and between straightener/
feed rolls and shear
A stationary shear line generally provides the best squareness and length tolerance and most productivity for lighter-gage
materials. Because of the nature of the loop, this feeding method is not practical for strip over about 6.4 mm ( in.) thick.
A hump line may be somewhat less expensive when the costs of installation are included, but tolerance, squareness, and
productivity may be sacrificed.
Rotary drum shears are sometimes used in high-production sheet mills at speeds to 300 m/min (1000 ft/min). The
tinplate flying shear, a special type of rotary drum shear, is made specifically for cutting coils of tinplate into lengths for
use in the manufacture of cans.
Blanking lines are a special derivation of shearing lines. Most shearing lines, of any of the above configurations, are
designed for cutting sheets ranging in length from 0.6 m (2 ft) to 8 to 9 m (25 to 30 ft). Because these sheets are to be
fabricated later into an end product, length tolerance requirements may not be critical. Blanking lines have the special
capability of rapidly cutting and stacking relatively short and dimensionally accurate blanks.
Edge-trim slitters are incorporated into some line configurations. However, these follow the camber or sweep found in
almost all master coils obtained from the mill. These slitters cannot be counted on to eliminate or even control camber or
to provide improved sequences.
Cut-to-length line capacity may be limited by the shear. Most shears include a raked blade. As a result, the shear,
and therefore the cut-to-length line, does not have a short/thick capacity. If, for example, the line capacity were 6.4 ×
1830 mm ( × 72 in.), the maximum thickness for 305 mm (12 in.) wide material would still be only 6.4 mm ( in.).
Dimensional accuracy of the cut sheet length depends on the line configuration, condition of the equipment, speed
and length of sheet, and the condition of the master coil. In previous generations of equipment, an accuracy of ±1.6 mm
(± in.) was acceptable. Most modern lines are accurate to ±0.8 mm (± in.), except on very long sheets.
Sophisticated equipment is also available that can produce sheets or blanks with tolerances of ±0.4 mm (± in.).