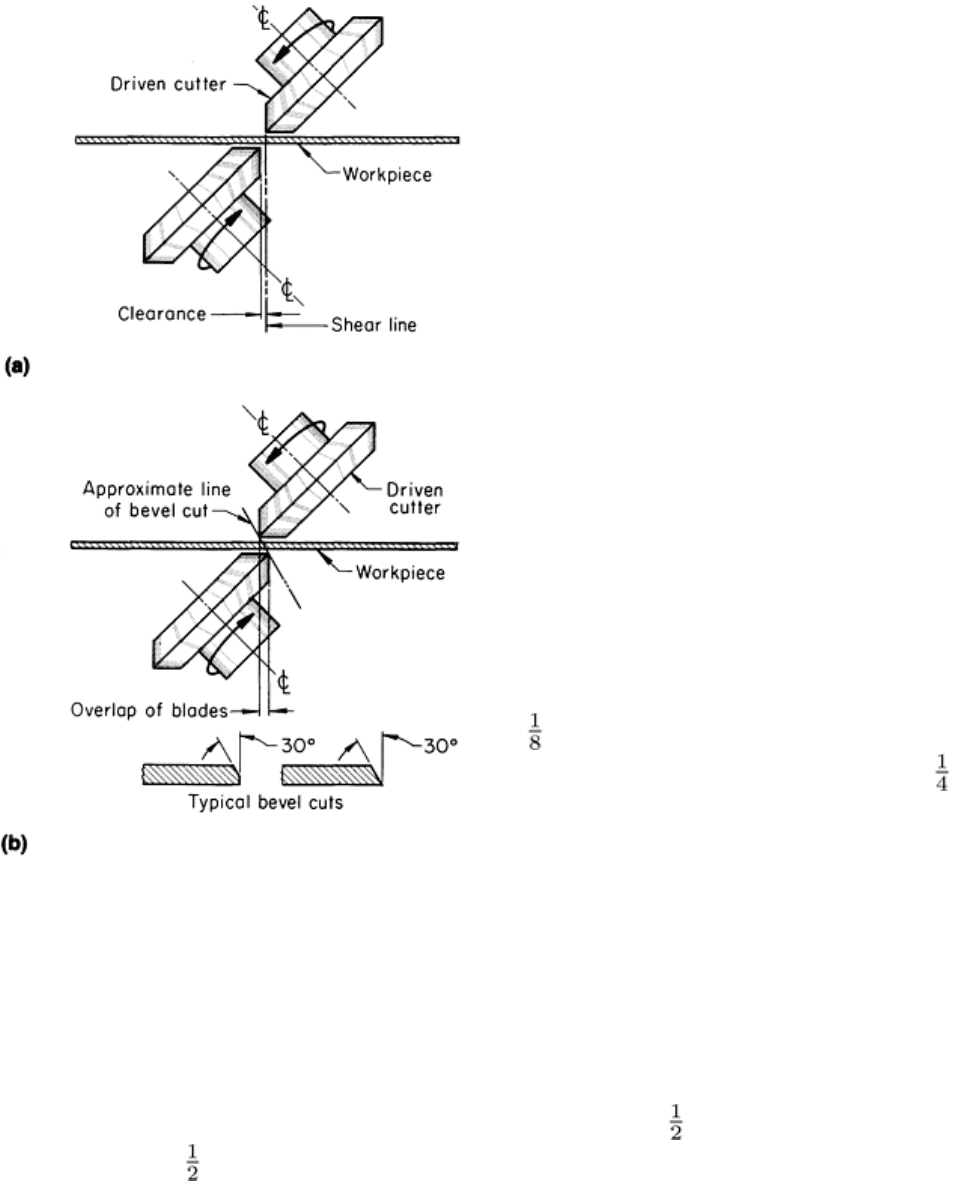
Overlapping of the cutters to the position shown in Fig.
6(b) permits the shearing of smooth beveled edges in
straight lines or circular shapes. With the cutters
positioned as shown in Fig. 6(b), a bevel can be cut across
the entire thickness of the workpiece, resulting in a sharp
edge on the bottom of the workpiece, or (by varying the
overlap of the cutters) only a corner of the workpiece can
be sheared off, leaving a vertical edge (or land) for
approximately half the workpiece thickness.
The shearing of workpieces into circular blanks requires
the use of a holding fixture that permits rotation of the
workpiece to generate the desired circle. For straight-line
cutting in a rotary shear, a straight-edge fixture is used,
mounted in the throat of the machine behind the cutter
heads.
Applicability. Any metal composition or hardness that
can be sheared with straight knives can be sheared with
rotary cutters. In general, rotary shearing in commercially
available machines is limited to work metal 25 mm (1 in.)
thick or less. There is no minimum thickness. For
example, wire cloth made from 0.025 mm (0.001 in.) diam
wire can be successfully sheared by the rotary method.
Circles up to 3 m (10 ft) in diameter or larger can be
produced by using special clamping equipment. Minimum
diameters depend on the thickness of the work metal and
the size of the rotary cutters. With material up to 3.2 mm
( in.) thick, the minimum circle that can normally be cut
is 152 mm (6 in.) in diameter. For 6.4 mm ( in.) thick
stock, the minimum diameter is 230 mm (9 in.), and for 25
mm (1 in.) thick stock, the minimum diameter is 610 m
(24 in.).
Rotary shearing is limited to cutting one workpiece at a
time. As in straight-knife shearing, multiple layers cannot
be sheared, because each layer prevents the necessary
breakthrough of the preceding workpiece.
Rotary shearing, plasma cutting, laser cutting, gas cutting,
and electric-arc cutting are competitive for some operations. Each can produce straight or beveled edges of comparable
accuracy. The selection of one of the four processes depends largely on the thickness of the work metal. In general, rotary
shearing and laser cutting are used for sheet and plate less than 12.7 mm ( in.) thick, and gas cutting is used for
thicknesses of 12.7 mm ( in.) or more (see the articles "Laser Cutting" and "Thermal Cutting" in this Volume).
Gas cutting is less suitable for cutting a single thickness of sheet or thin plate because the heat causes excessive distortion,
but it is often feasible to minimize this problem by stack cutting (cutting several thicknesses at a time). Gas cutting is
more versatile than rotary shearing; it can produce smaller circles than rotary shearing and can produce rings in one
operation. Gas cutting, however, produces a relatively large heat-affected zone on the workpiece.
Laser cutting produces an extremely narrow kerf that provides unmatched precision for cutting small holes, narrow slots,
and closely spaced patterns. Complex openings, contours, and patterns, which are impossible to cut with conventional
tools, are routinely cut using a laser and require little if any additional processing. A smaller heat-affected zone than
traditional thermal cutting processes minimizes distortion and improves part quality.
Fig. 6 Two types of rotary sheari
arrangement of cutters for producing a perpendicular
edge.
(b) Overlap of cutters for producing a beveled
edge.