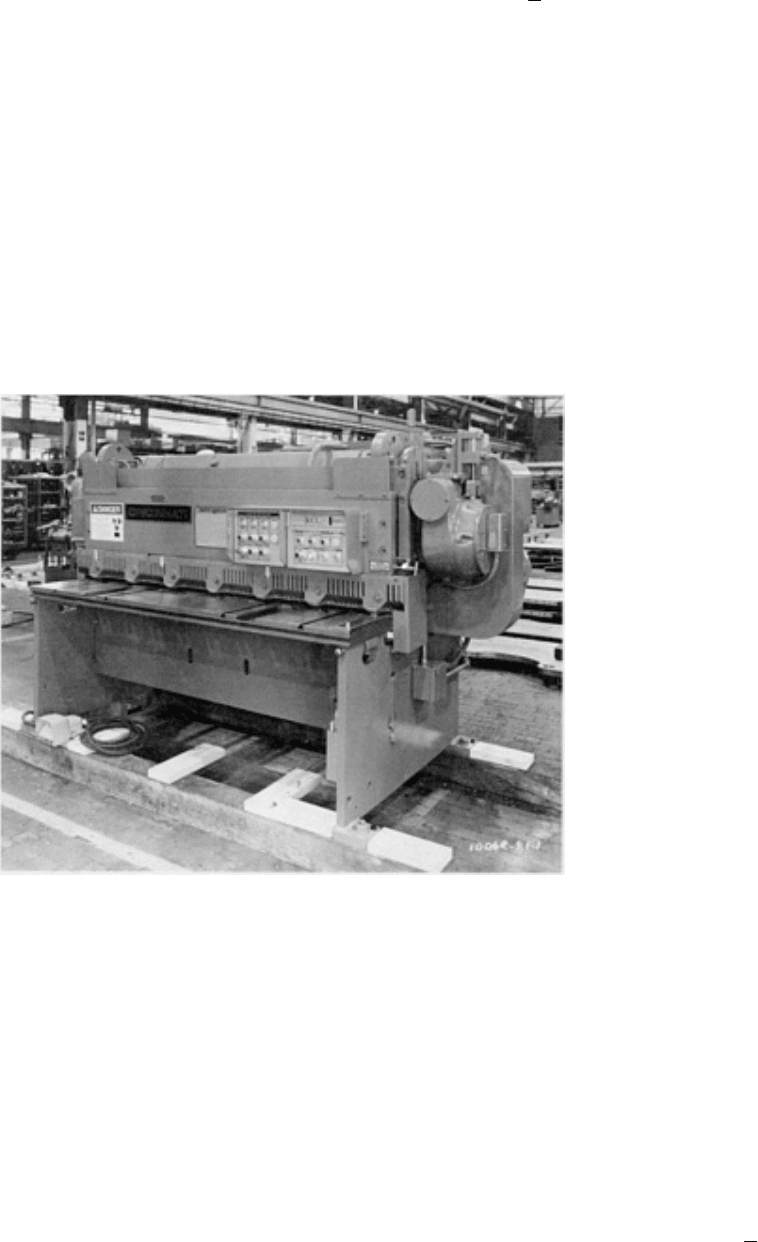
In general, it is practical to shear flat stock up to 38 mm (1
in.) thick in a squaring shear. Squaring shears up to 9 in (30
ft) long are available (even longer shears have been built), and some types are equipped with a gap that permits shearing
of work metal longer than the shear knife.
Machines for Straight-Knife Shearing
Punch presses and press brakes are sometimes used for shearing a few pieces or are used temporarily when more efficient
equipment is not available. Production shearing, however, is usually done in machines that are designed for this operation.
Squaring shears are usually used for trimming and cutting sheet or plate to specific size (Fig. 2). Squaring shears (also
called resquaring or guillotine shears) are available in a wide range of sizes and designs. Some types permit slitting by
moving the work metal a predetermined amount in a direction parallel with the cutting edge of the knife after each stroke
of the shear.
The sheet or plate is held rigid by hold-down devices
while the upper knife moves down past the lower knife.
Most sheet or plate is sheared by setting the upper knife
at an angle. The position of one knife can be adjusted to
maintain optimal clearance between the knives.
Squaring shears can be actuated mechanically,
hydraulically, or pneumatically.
Mechanical Shears. The power train of a
mechanical shear consists of a motor, the flywheel, a
worm shaft that is gear driven by a flywheel, a clutch
that connects the worm gear drive to the driveshaft, and
a ram actuated by the driveshaft through eccentrics and
connecting links. Under most operating conditions, a
mechanical shear can deliver more strokes per minute
(spm) than a hydraulic shear. Some mechanical shears
cycle as fast as 100 spm.
Another advantage of the mechanical shear is that,
because of the energy stored in the flywheel, a smaller
motor can be used for intermittent shearing. For
example, a mechanical shear with a no-cutting or free-
running speed of 65 spin can make approximately six
full shearing strokes (maximum thickness and length of
cut) per minute with a standard motor. However, when
the same shear is cutting at full capacity in a rapid shear mode, a much larger motor is required. For such rapid cutting,
there is not enough time between cuts for the smaller motor to restore the speed of the flywheel.
An additional advantage of the mechanical shear is that its moving knife travels faster than the moving knife of a
hydraulic shear. In some cases, greater knife speed can decrease work metal twist, bow, and camber.
Hydraulic shears are actuated by a motor-driven pump that forces oil into a cylinder against a piston; the movement of
the piston energizes the ram holding the upper knife. A hydraulic shear can make longer strokes than a mechanical shear.
In general, long shears and shears with low-carbon steel capacities above 12.7 mm (
in.) are almost all hydraulic.
Hydraulic shears are designed with a fixed load capacity. This prevents the operator from shearing material that exceeds
capacity and therefore saves costly damage to the machine structure. This is a basic advantage of hydraulic shears.
The total load that is experienced during the cut is related to the rake angle, sharpness of the knives, mechanical
properties of the material, type of material, knife clearance, and the depth of the back piece. It is possible to stall the
machine on a rated-capacity cut if the clearance is incorrect, the knife is dull, or the back piece is excessively deep. In this
Fig. 2 Typical squaring shear. Courtesy of Cincinnati Inc.