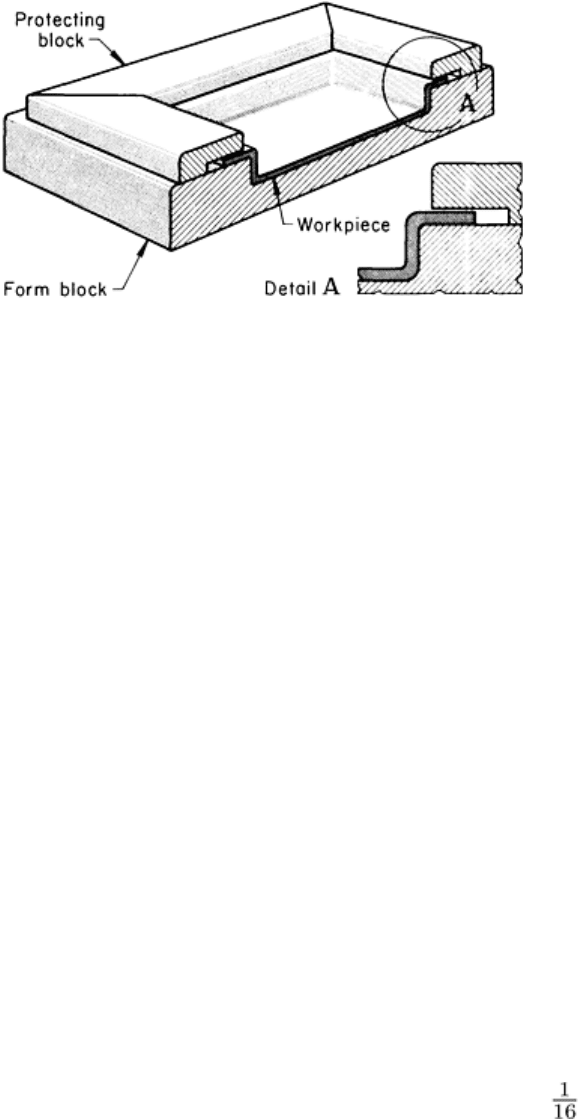
Marform Process
The Marform process was developed to apply the
inexpensive tooling of the Guerin and Verson-Wheelon
processes (see the section "Verson-Wheelon Process" in
this article) to the deep drawing and forming of wrinkle-
free shrink flanges. A blankholder plate and a hydraulic
cylinder with a pressure-regulating valve are used with a
thick rubber pad and a form block similar to those used in
the Guerin process. The blank is gripped between the
blankholder and the rubber pad. The pressure-regulating
valve controls the pressure applied to the blank while it is
being drawn over the form block.
While forming a soft aluminum alloy blank, the diameter
can usually be reduced 57%, and reductions as high as
72% have been obtained. A shell depth equal to the shell
diameter is normal when the minimum stock thickness is
1% of the cup diameter. Depths up to three times shell diameter have been reached with multiple-operation forming. The
minimum cup diameter is 38 mm (1½ in.).
Foil as thin as 0.038 mm (0.0015 in.) can be formed by placing the blank between two aluminum blanks about 0.76 mm
(0.030 in.) thick and forming the three pieces as a unit. The inner and outer shells are discarded.
Presses. The Marform process is best suited to a single-action hydraulic press in which pressure and speed of operation
can be varied and controlled. A Marform unit comes as a package that can be installed in a hydraulic press having ample
stroke length and shut height. However, a press that incorporates a hydraulic cushion system into its bed has been
designed specifically for Marforming.
The rubber pressures used depend on the force capacity of the press and the surface area of the rubber pad. Recent
installations range from 34 to 69 MPa (5 to 10 ksi).
Tools. The rubber pad used in Marforming is similar to that used in the Guerin process. It is normally 1½ to 2 times as
thick as the total depth of the part, including trim allowance. The rubber pad can be protected from scoring by the use of a
throw sheet, which is either cemented to the pad or thrown over the blank.
Well-polished steel form blocks are used for long runs and deep draws. Aluminum alloy form blocks must be hard coated
to prevent galling for draws deeper than 38 mm (1½ in.). Masonite form blocks can be used if they can withstand the
abuse and wear of forming a particular part in a given quantity. When a cast shape is more economical, aluminum or zinc
alloy form blocks can be used.
Blankholder plates are usually made of low-carbon steel. The contact surface is ground flat and polished to avoid
scratching of the blank. Clearance between the form block and the mating hole in the blankholder is 0.76 to 1.52 mm
(0.030 to 0.060 in.) per side. The edge should have a 1.6 mm ( in.) radius.
A radius plate is necessary when the machine pressure is insufficient for forming the flange radius within tolerance. The
part is drawn first without the plate, then redrawn using the plate to form the exact radius. The radius plate is usually 13
mm (½ in.) thick and 25 mm (1 in.) wider than the workpiece. A sealing ring is used to prevent the rubber pad from
extruding out of the container.
Procedure. The blank rests on the blankholder plate above the form block. The rods supporting the seal ring and
blankholder plate (Fig. 6) are supported on a variable-pressure hydraulic cushion. As the press ram is lowered, the blank
is clamped between the rubber pad and the blankholder before forming begins. As the rubber pad continues to descend,
the blank is drawn over the form block while the pressure control valve in the hydraulic cushion releases fluid at a
controlled rate. The pressure in the hydraulic cushion must be adjusted to prevent wrinkles from forming in the flange but
to permit the blank to be drawn into a smooth shell. The part is stripped from the form block by the blankholder. The
following example describes an application of the process.
Fig. 5
Use of a protecting block to prevent work metal
irregularities in shallow drawing by the Guerin process.