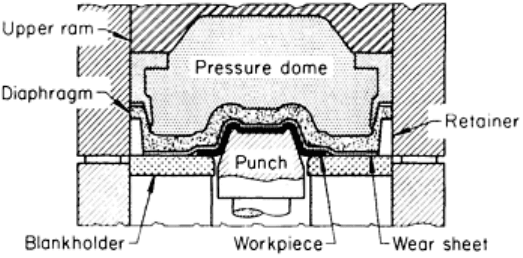
draws can be made by this method than in conventional draw dies because the oil pressure against the diaphragm causes
the metal to be held tightly against the sides as well as against the top of the punch.
Reductions in blank diameter of 60 to 70% are common for
a first draw. When redrawing is necessary, reductions can
reach 40%. Low-carbon steel, stainless steel, and aluminum
in thicknesses from 0.25 to 1.65 mm (0.010 to 0.065 in.) are
commonly formed. Parts made of heat-resistant alloys and
copper alloys are also formed by this process.
Presses. A special press, called a Hydroform press, is used
for this process. A lower hydraulic ram drives the punch
upward; the upper ram is basically a positioning device. A
hydraulic pump delivers fluid under pressure to the pressure
dome. The blankholder is supported by a solid bolster and
does not move during the operation.
Dome pressures range from 41 to 103 MPa (6 to 15 ksi), and
punch force capacities vary from 3.2 to 19 MN (368 to 2089
tonf). Special guide pins and a platen adaptor convert a standard Hydroform press into a single-action conventional
hydraulic press with a force capacity of 6.2 to 40 MN (700 to 4470 tonf). This variation of the process has the punch
stationary and the blankholder actuated by the die cushion of a single-action hydraulic press, as shown in Fig. 20.
Maximum blank diameters are 305 to 1020 mm (12 to 40 in.), maximum punch diameters are 254 to 864 mm (10 to 34
in.), and maximum draw depths are 178 to 305 mm (7 to 12 in.). The maximum rating is 1500 cycles per hour. The
practical production rate in cycles per hour is usually about two-thirds the machine rating. However, the operation often
takes the place of two or three conventional press operations.
Tools. Punches can be made of tool steel, cold-rolled steel, cast iron, zinc alloy, plastic, brass, aluminum, or hardwood.
Choice of material depends largely on the work metal to be formed, number of parts to be made, shape of the part, and
severity of the draw.
Blankholders are usually made of cast iron or steel and are hardened if necessary. Clearance between punch and
blankholder is not critical; it may be 50% or more of the thickness of the metal being drawn.
For short runs, an auxiliary blankholding plate can be placed on a blankholder that is already in place. The auxiliary
blankholder plate should not overhang in the punch clearance more than its thickness, and it should not be larger than the
blankholder.
Rubber strips are placed on the blank to break the vacuum caused by dome action during drawing. Blankholders can be
contoured to match the shape of a preformed blank or to preform the blank as an aid in forming.
Procedure. The blank to be formed is placed on the blankholder. The pressure dome, filled with the hydraulic fluid and
covered by the rubber diaphragm, is lowered over the blank, and preliminary pressure is applied through a pump in the
hydraulic supply line. The preliminary pressure can range from 14 to 69 MPa (2 to 10 ksi), depending on the part to be
formed.
The punch is raised and pushed into the blank from underneath. As the form in the blank rises into the hydraulic chamber,
the pressure in the chamber increases sharply, reaching as high as 103 MPa (15 ksi). A pressure control valve keeps the
pressure within programmed limits. When parts are formed of thin metal, a vacuum release valve can be built into the
punch to aid stripping after forming.
Three cams are programmed to control the operation of the machine. The first controls the height of rise of the punch, the
second controls edging or sharpening of the corner radii, and the third returns the punch at the end of the stroke while the
blankholder strips the finished part from the punch. The forming of a complex part by the rubber-diaphragm process is
described in the following example.
Example 6: Rubber-Diaphragm Forming of a Complex Jet-Engine Part.
Fig. 16 Fluid-cell forming in a Hydroform press.