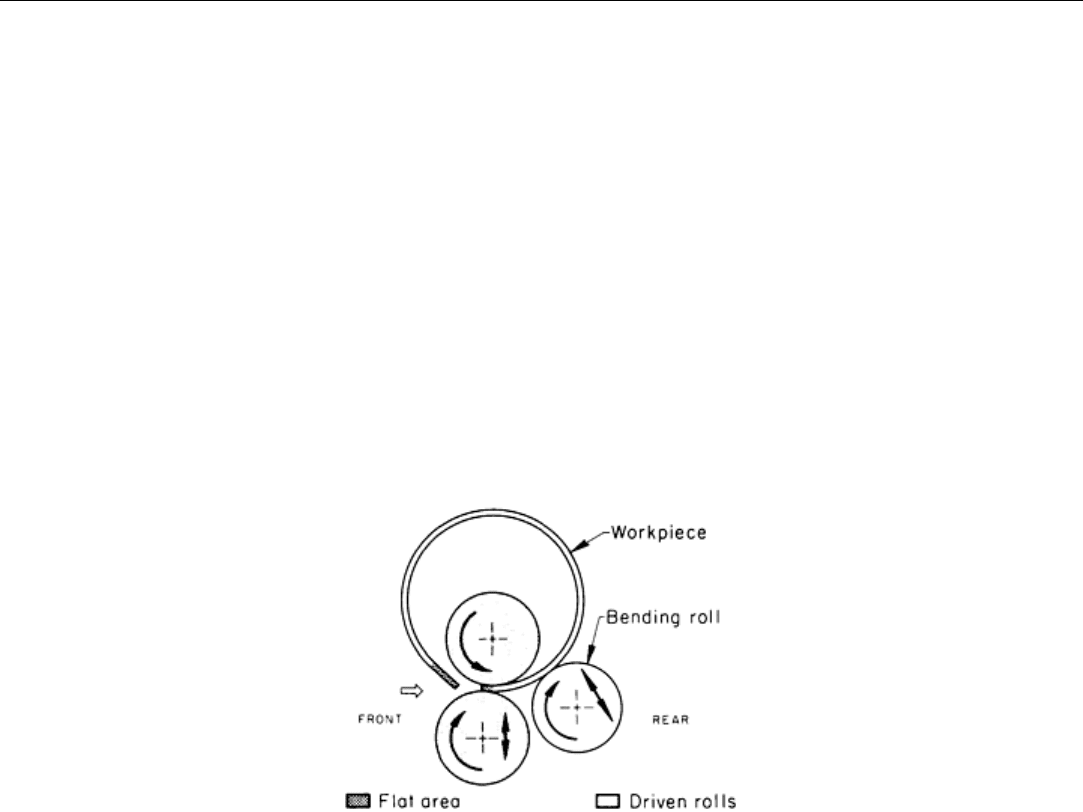
a maximum capability for rolling 1.52 mm (6 in.) plate can successfully roll plate as thin as 13 mm (½ in.)--even less on
some machines.
Diameter and Width. The minimum diameter of a workpiece that can be successfully formed in a given machine is
governed by the diameter of the top roll on either of the two types of machines used in three-roll forming--pinch type or
pyramid type. In general, the smallest cylinder that can be rolled under optimal conditions is 50 mm (2 in.) larger in
diameter than the top roll of a pinch-type machine. On a pyramid-type machine, the minimum workpiece diameter is
rarely less than 152 mm (6 in.) greater than the top roll. However, more power is required to form sheet or plate into
cylinders of minimum diameter than to form cylinders substantially larger than the top roll.
The maximum workpiece diameter that can be rolled is primarily limited by the space available above the machine to
accommodate extremely large circles. Thin-gage metal rolled to a large diameter on horizontal rolls becomes less self-
supporting as the workpiece diameter increases, and out-of-round cylinders will result if supports are not used. However,
by using supports, almost any diameter can be rolled from thin metal. In general, 1.52 mm (0.0598 in.) thick low-carbon
steel sheet can be formed into cylinders as large as 1.2 m (48 in.) in diameter without support, while 6.4 mm (¼ in.) thick
low-carbon steel can be formed into cylinders as large as 2.1 m (84 in.) in diameter without support.
The width (dimension of the work metal parallel with the axes of the rolls, designated as length in the formed cylinder) of
sheet or plate that can be rolled is limited by the size of the equipment; machines with rolls as long as 12.5 m (41 ft) have
been built. The width-to-diameter relationship for workpieces that are extremely large in both directions is limited by
problems in handling.
Three-Roll Forming
Machines
There are two basic types of three-roll forming machines: the pinch-roll type and the pyramid-roll type. The rolls on most
three-roll machines are positioned horizontally; a few vertical machines are used, primarily in shipyards. Vertical
machines have one advantage over horizontal machines in forming scaly plate: Loose scale is less likely to become
embedded in the work metal. With vertical rolls, however, it is difficult to handle wide sections that require careful
support to avoid skewness in rolling. Most vertical machines have short rolls for fast unloading and are used for bending
narrow plate, bars, and structural sections.
Conventional pinch-type machines have the roll arrangement shown in Fig. 2. For rolling flat stock up to about 25
mm (1 in.) thick, each roll is of the same diameter. However, on larger machines, the top rolls are sometimes smaller in
diameter to maintain approximately the same surface speed on both the inside and outside surfaces of the plate being
formed. These heavier machines are also supplied with a slip-friction drive on the front roll to permit slip, because of the
differential in surface speed of the rolls. Therefore, as work metal thickness increases, the diameter of the top roll is
decreased in relation to the diameter of the lower rolls.
Fig. 2 End view of a cylindrical workpiece being rolled in a conventional pinch-t
ype machine. Note the large flat