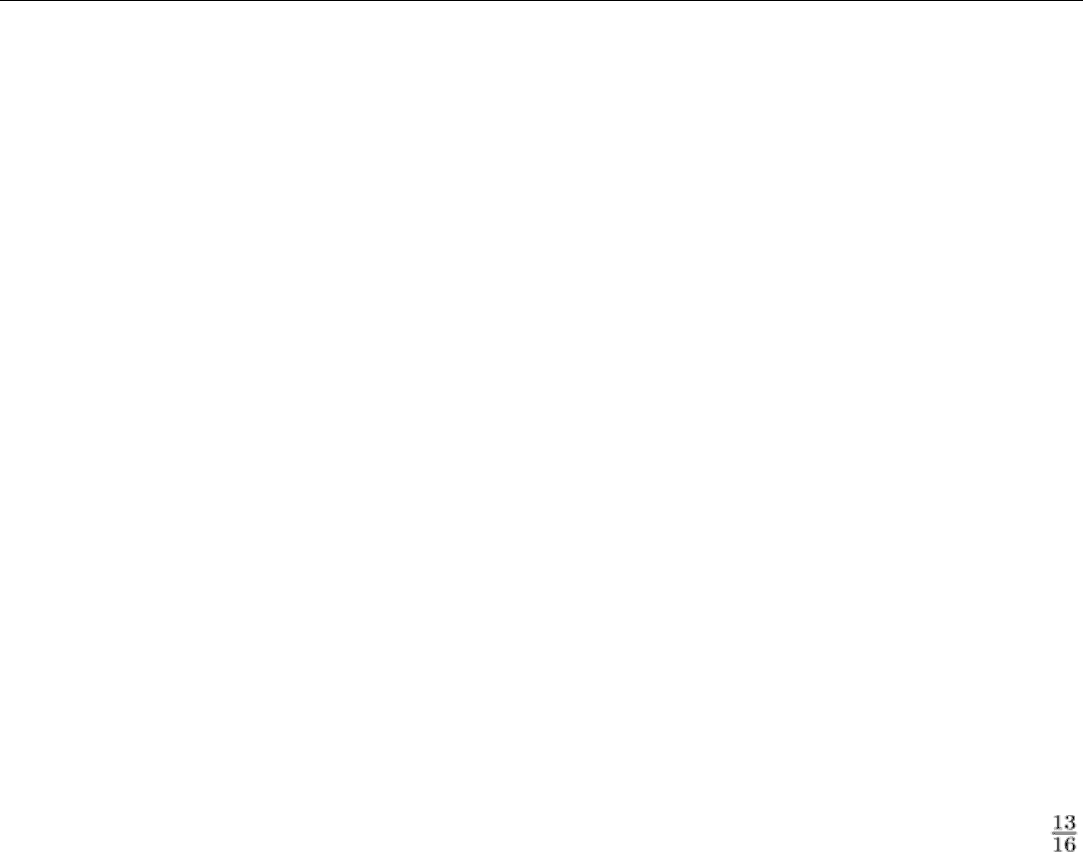
Machines for stretch wrapping consist basically of a variable-speed power-driven rotary table and a double-action
pressure-controlled hydraulic cylinder. The form block is bolted to the table. Grippers are connected to the hydraulic
cylinder so that tension can be applied to the workpiece, as in Fig. 1(c). The fabrication of a typical part by stretch
wrapping is described in the following example.
Example 3: Forming of an Aircraft Leading-Edge Wing Panel by Stretch
Wrapping.
A corrugated leading-edge wing panel of aluminum alloy 6061-O was stretch wrapped in a stretch-forming machine with
a vertical-axis turntable. The sheet, with corrugations in the direction of airflow, was gripped at each end with grippers
shaped to fit the corrugations. The tension applied was slightly above the yield strength of the work metal. The form
block, bolted to the turntable, rotated slowly into the workpiece, causing it to form smoothly into the shape of the wing
without flattening the corrugations. While the form block was moving in the sheet, the hydraulically restrained gripper
maintained tension slightly above the yield point. The form block was made to the required final shape without allowance
for springback because only a small amount of springback occurred.
Stretch Forming
Compression Forming
In compression forming, the workpiece is pressed against the rotating form block instead of being wrapped around it. The
process is typically used for maintaining or controlling workpiece cross-sectional dimensions throughout the contour, for
bending to radii small enough to exceed the elongation limits of the metal if formed by stretch wrapping, and for bending
sections too heavy for the capacity of the available stretch wrap machinery.
Compression forming can generally be done in the same machine as stretch wrapping, but the hydraulic cylinder is used
to apply pressure instead of tension to the workpiece. The cylinder is locked in place to keep it from swiveling, and the
ram head is furnished with a roller or a shoe to press the workpiece against the form block. A clamp or table gripper holds
the end of the workpiece against the form block, and as the table rotates, the shoe or roller on the hydraulic cylinder
presses the workpiece into the contour of the block, as shown in Fig. 1(d).
Compression forming can often make bends to a smaller radius than stretch wrapping in a part that has a deep cross
section. If the same bend were produced by stretch wrapping, fracturing or overstressing of the outer fibers would result.
The total load needed to form large-section pieces, such as crossrails and bumpers, can be as little as 2% of that needed to
form them in a punch press. The total energy applied to the workpiece would of course be the same (neglecting
efficiency); the smaller compression-forming force is applied for a longer period of time. The wiping shoe or roller can
hold the cross-sectional size and shape to close tolerance throughout the contour. Parts that are too heavy in cross section
for stretch wrapping can often be compression formed.
Blanks for stretch forming are usually made longer than the finished part so that the surface damaged by the gripper jaws
can be trimmed off. However, end details, locating surfaces, and other considerations occasionally necessitate the use of a
blank cut to the length of the finished part, and dimensional tolerances still must be met, as in the following example.
Example 4: Use of an Adjustable Form Block to Compression Form a Developed
Blank.
Because both ends of the piece shown in Fig. 10 had previously produced details, the part could not be trimmed after
forming. Instead of a table gripper or clamp, the blank was fastened to the form block by bolts through two 21 mm (
in.) diam holes pierced in one end. The blank was cut slightly shorter than the required length because the length
increased from 3.602 to 3.613 m (141.81 to 142.25 in.) during forming.