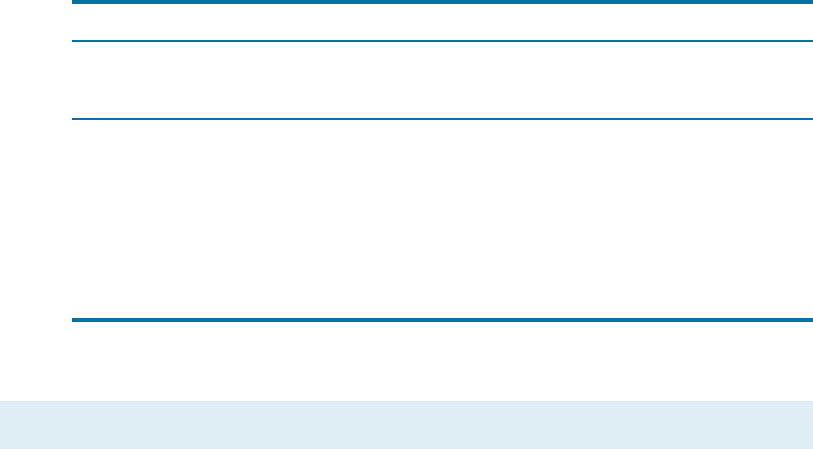
15-3 Synthesis and Processing of Ceramic Powders
Ceramic materials melt at high temperatures and they usually exhibit a brittle behavior
under tension. As a result, the casting and thermomechanical processing, used widely
for metals, alloys, and thermoplastics, cannot be applied when processing ceramics.
Inorganic glasses, though, make use of lower melting temperatures due to the formation
of eutectics and are made using the float-glass process. Since melting, casting, and
thermomechanical processing is not a viable option for polycrystalline ceramics, we
typically process ceramics into useful shapes starting with ceramic powders. A powder is
a collection of fine particles. The step of making a ceramic powder is defined here as the
synthesis of ceramics. We begin with a ceramic powder and get it ready for shaping by
crushing, grinding, separating impuritie s, blending di¤erent powders, and spray drying
to form soft agglomerates. Di¤erent techniques such as compaction, tape casting, ex-
trusion, and slip casting are then used to convert properly processed powders into a
desired shape to form what is known as a green ceramic. A green ceramic is a ceramic
that has not yet been sintered. The steps of converting a ceramic powder (or mixture of
powders) into a useful shape are known as powder processing. The green ceramic is then
consolidated further using a high-temperature treatment known as sintering or firing. In
this process, the green ceramic is heated to a high temperature, using a controlled heat
treatment and atmosphere, so that a dense material is obtained. The ceramic may be
then subjected to additional operations such as grinding, polishing, or machining as
needed for the final application. In some cases, leads will be attached, electrodes will be
deposited, or coatings may have to be deposited. These general steps encountered in the
synthesis and processing of ceramics are summarized in Figure 15-1.
Ceramic powders prepared using conventional or chemical techniques are shaped
using the techniques shown in Figure 15-2. We emphasize that very similar processes
are used for processing metal and alloy powders, a route known as powder metallurgy.
Powders consist of particles that are loosely bonded, and powder processing involves
the consolidation of these powders into a desired shape. Often, the ceramic powders
prepared need to be converted into soft agglomerates by spraying a slurry of the pow-
der through a nozzle into a chamber (spray dryer) in the presence of hot air. This
process leads to the formation of soft agglomerates that flow into the dies used for
powder compaction; this is known as spray drying.
TABLE 15-3 9 Mechanical properties of selected advanced ceramics
Material
Density
(g/cm
3
)
Tensile
Strength
(MPa)
Flexural
Strength
(MPa)
Compressive
Strength
(MPa)
Young’s
Modulus
(MPa)
Fracture
Toughness
(MPa
ffiffiffiffi
m
p
)
Al
2
O
3
3.98 207 552 3025 386 10
3
5.5
SiC (sintered) 3.1 172 552 3860 414 10
3
4.4
Si
3
N
4
(reaction bonded) 2.5 138 241 1030 207 10
3
3.3
Si
3
N
4
(hot pressed) 3.2 552 896 3450 310 10
3
5.5
Sialon 3.24 414 965 3450 310 10
3
9.9
ZrO
2
(partially stabilized) 5.8 448 690 1860 207 10
3
11.0
ZrO
2
(transformation
toughened)
5.8 345 793 1725 200 10
3
12.1
CHAPTER 15 Ceramic Materials472