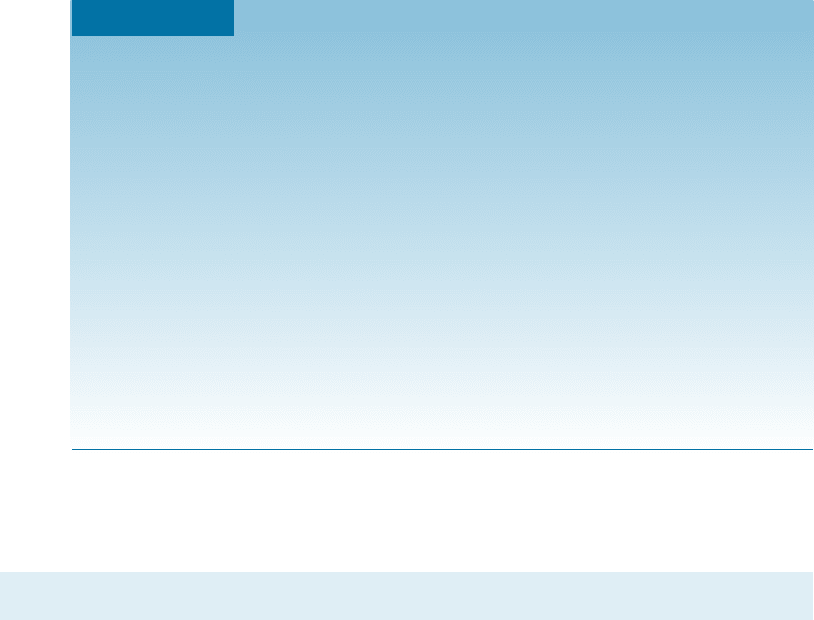
EXAMPLE 14-3 Design/Materials Selection for a Cryogenic Tank
Design the material to be used to contain liquid hydrogen fuel for the space
shuttle.
SOLUTION
Liquid hydrogen is stored below 253
C; therefore, this tank must have good
cryogenic properties. The tank is subjected to high stresses, particularly when
the space shuttle enters into orbit, and it should have good fracture toughness
to minimize the chances of catastrophic failure. Finally, it should be light in
weight to permit higher payloads or less fuel consumption.
A lightweight aluminum alloy would appear to be a good choice. Alumi-
num does not show a ductile to brittle transition. Because of its good ductility,
we expect aluminum to also have good fracture toughness, particularly when
the alloy is in the annealed condition.
One of the most common cryogenic aluminum alloys is 5083-O.
Aluminum-lithium alloys are also being considered for low-temperature appli-
cations to take advantage of their even lower density.
14-2 Magnesium and Beryllium Alloys
Magnesium, which is often extracted electrolytically from concentrated magnesium
chloride in seawater, is lighter than aluminum with a density of 1.74 g/cm
3
, and it melts
at a slightly lower temperature than aluminum. In many environments, the corrosion
resistance of magnesium approaches that of aluminum; however, exposure to salts, such
as that near a marine environment, can cause rapid deterioration. Alloys of magnesium
that are resistant to corrosion have been developed. Although magnesium alloys are not
as strong as aluminum alloys, their specific strengths are comparable. Consequently,
magnesium alloys are used in aerospace applications, high-speed machinery, and
transportation and materials handling equipment.
Magnesium, however, has a low modulus of elasticity (44:8 10
3
MPa) and poor
resistance to fatigue, creep, and wear. Magnesium also poses a hazard during casting
and machining, since it combines easily with oxygen and burns. Finally, the response of
magnesium to strengthening mechanisms is relatively poor.
Structure and Properties Magnesium, which has the HCP structure, is less ductile
than aluminum. However, the alloys do have some ductility because alloying increases
the number of active slip planes. Some deformation and strain hardening can be
accomplished at room temperature, and the alloys can be readily deformed at elevated
temperatures. Strain hardening produces a relatively small e¤ect in pure magnesium
because of the low strain-hardening coe‰cient (Chapters 6 and 8).
As in aluminum alloys, the solubility of alloying elements in magnesium at room
temperature is limited, causing only a small degree of solid-solution strengthening.
However the solubility of many alloying elements increases with temperature, as shown
in the Mg-Al phase diagram (Figure 14-4). Therefore, alloys may be strengthened
CHAPTER 14 Nonferrous Alloys444