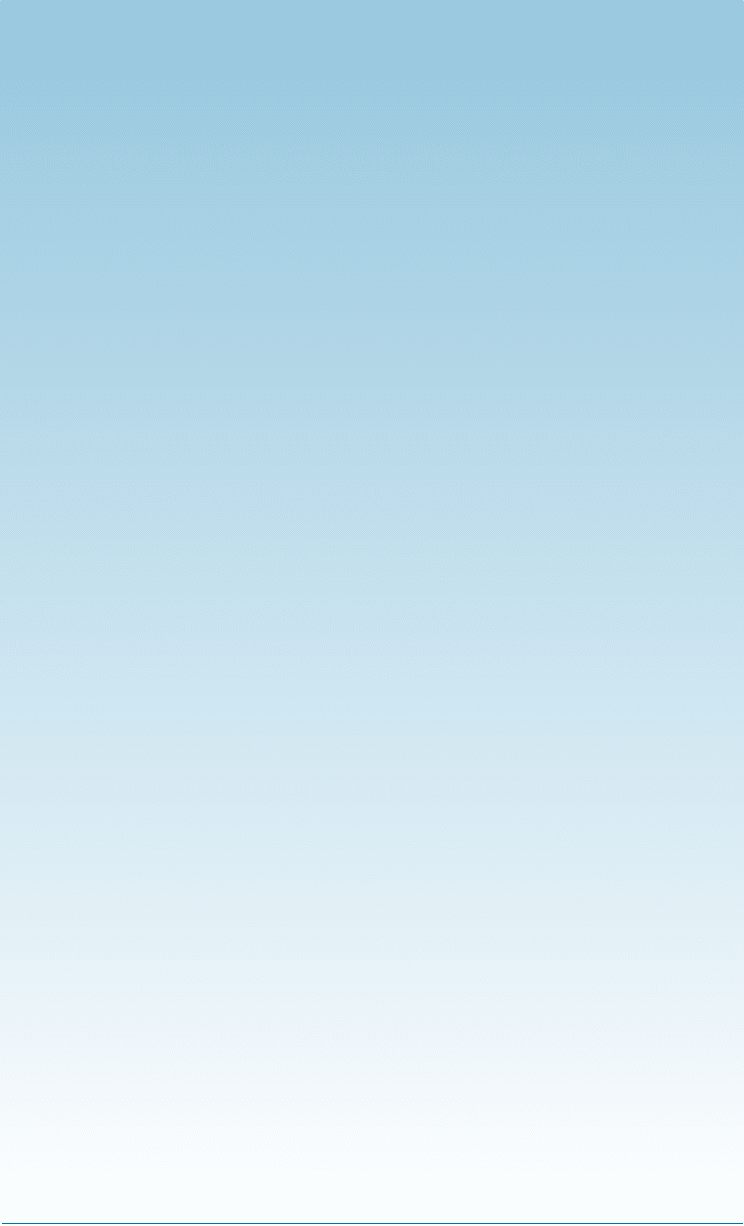
Strength–Toughness Combination of a New 700 MPa Nb-Microalloyed Pipe-
line Steel Materials Science and Engineering: A.S. Shanmugam, N.K. Ram-
isetti, R.D.K. Misra, J. Hartmann and S.G. Jansto (in press, 2007).] (a) What
other factors must be considered for high-strength steels for oil pipelines? (b)
Based on what you have learned in terms of mechanisms of strengthening, how
can you choose the best possible alloying elements for this application? Assume
that you can conduct whatever experiments are necessary.
SOLUTION
(a) O ne of the first considerations is that when we increase strength signifi-
cantly, is there a loss of ductility? The trick to developing such materials
is that they provide not just strength but also an adequate level of ductility
such that forming (e.g., rolling, extrusion, etc., Chapter 8) is still possible.
Another consideration is the possibility of these steels becoming brittle due
to incorporation of hydrogen or sulfur. We can also choose such alloying
elements as chromium, nickel, and copper, because they have been known
to provide adequate strength even in a corrosive environment (Sec-
tion 13-10). An additional consideration would be the weldability of the
steels and the microstructure both of the steel and of the area surrounding
the weld region (Section 13-9).
(b) We can get some strengthening due to solid-solution formation (Chap-
ter 10) and the formation of second phases (Chapter 12). We can also proc-
ess the steel so as to get a fine grain size to get the Hall-Petch strengthening
e¤ect (Chapter 4). The primary grain size of the ferrite that will form from
austenite is controlled by the grain size of the recrystallized austenite. We
can minimize the primary austenite grain size by using niobium. It is known
that niobium is a good carbide former. Fine precipitates of niobium carbides
will pin the boundaries of austenite and prevent it from grain growth
(Chapter 5).
To get exceptionally high strengths, we can resort to the formation of
nano-sized precipitates of a second phase in a soft matrix such as ferrite. The
choice of alloying elements that could be added can be guided by knowing
what forms of precipitates can form so as to get a significant level of precip-
itation strengthening. This strengthening mechanism can be achieved by
additions of not only niobium but also of titanium and vanadium. Care
must be taken to ensure that such precipitates are fine (<10 nm), coherent,
and high in number concentrations (Chapter 5). We can also study how such
an alloy is a¤ected as a result of the exposure to heat from the welding
processes that will be used. Will there be a heat-a¤ected zone (Chapter 9)
in which any precipitates formed may grow in size and thereby become in-
e¤ective in providing strengthening? Another important consid eration is the
cost and amounts of alloying elements needed; this must be optimized.
This example is meant to illustrate how the principles of what you have
learned so far are applied in an integrated fashion for developing a material
suitable for a given real-life application. Obviously, even with a team of expe-
rienced researchers and engineers from many disciplines, experimentation and
field testing are almost always required to develop a suitable and cost-e¤ective
material. It is not the inten t of this example to expect someone to just develop a
material simply by reading about the concepts.
C HA P T E R 1 3 Heat Treatment of Steels and Cast Irons414