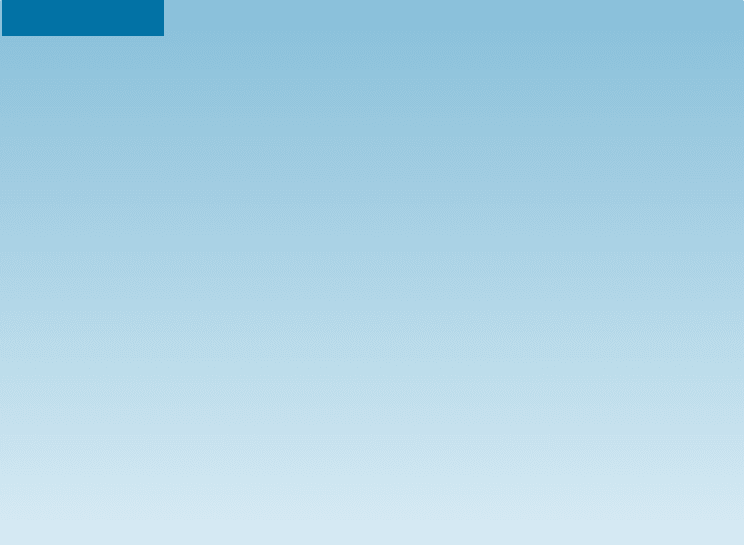
describe isothermal heat treatments (i.e., we assume that the sample begins and completes
heat treatment at a given temperature). Thus, we cannot exactly describe heat treat-
ments by superimposing cooling curves on a TTT diagram such as those shown in
Figure 13-6.
Effect of Changes in Carbon Concentration on the TTT Diagram In either a hypo-
eutectoid or a hypereutectoid steel, the TTT diagram must reflect the possible formation
of a primary phase. The isothermal transformation diagrams for a 1050 and a 10110
steel are shown in Figure 13-7. The most remarkable change is the presence of a ‘‘wing’’
which begins at the nose of the curve and becomes asymptotic to the A
3
or A
cm
tem-
perature. The wing represents the ferrite start (F
s
) time in hypoeutectoid steels or the
cementite start (C
s
) time in hypereutectoid steels.
When a 1050 steel is austenitized, quenched, and held between the A
1
and the A
3
,
primary ferrite nucleates and grows. Eventually, an equilibrium amount of ferrite and
austenite result. Similarly, primary cementite nucleates and grows to its equilibrium
amount in a 10110 steel held between the A
cm
and A
1
temperatures.
If an austenitized 1050 steel is quenched to a temperature between the nose and
the A
1
temperatures, primary ferrite again nucleates and grows until reaching the equi-
librium amount. The remainder of the austenite then transforms to pearlite. A similar
situation, producing primary cementite and pearlite, is found for the hypereutectoid
steel.
If we quench the steel below the nose of the curve, only bainite forms, regardless of
the carbon content of the steel. If the steels are quenched to temperatures below the M
s
,
martensite will form. The following example shows how the phase diagram and TTT
diagram can guide development of the heat treatment of steels.
EXAMPLE 13-3
Design of a Heat Treatment for an Axle
A heat treatment is needed to produce a uniform microstructure and hardness
of HRC 23 in a 1050 steel axle.
SOLUTION
We might attempt this task in several ways. We could austenitize the steel, then
cool at an appropriate rate by annealing or normalizing to obtain the correct
hardness. By doing this, however, we find that the structure and hardness vary
from the surface to the center of the axle.
A better approach is to use an isothermal heat treatment. From Figure
13-7, we find that a hardness of HRC 23 is obtained by transforming austenite
to a mixture of ferrite and pearlite at 600
C. From Figure 13-1, we find that
the A
3
temperature is 770
C. Therefore, our heat treatment is:
1. Austenitize the steel at 770 þ (30 to 55) ¼ 805
C to 825
C, holding for
1 h and obtaining 100% g.
2. Quench the steel to 600
C and hold for a minimum of 10 s. Primary
ferrite begins to precipitate from the unstable austenite ðg
u
Þ after about 1.0 s.
After 1.5 s, pea rlite begins to grow, and the austenite is completely transformed
to ferrite and pearlite after about 10 s. After this treatment, the micro-
constituents present are:
C HA P T E R 1 3 Heat Treatment of Steels and Cast Irons400