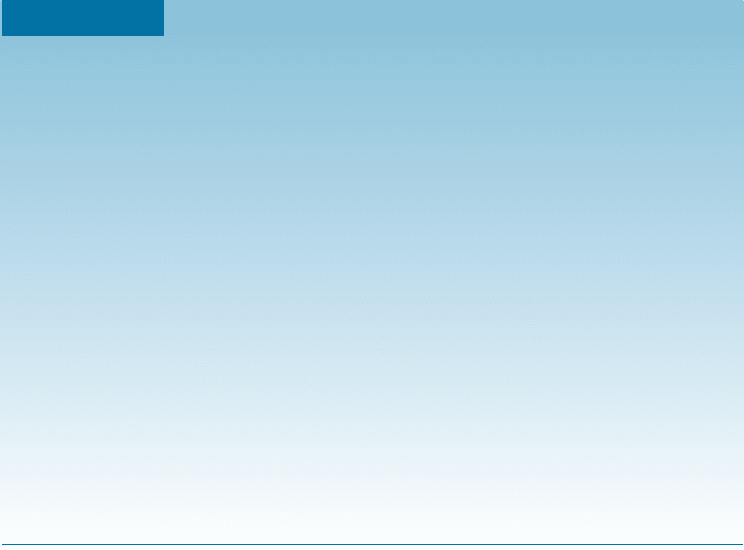
In Example 12-5, we saw that most of the pearlite is composed of ferrite. In fact, if
we examine the pearlite closely, we find that the Fe
3
C lamellae are surrounded by a.
The pearlite structure therefore provides dispersion strengthening—the continuous
ferrite phase is relatively soft and ductile and the hard, brittle cementite is dispersed.
The nex t example illustrates the similarity and di¤erences between composites and
pearlites.
EXAMPLE 12-6
Tungsten Carbide (WC)-Cobalt (Co) Composite and Pearlite
Tungsten carbide-cobalt composites, known as cemented carbides or carbides,
are used as bits for cutting tools and drills (Chapter 1). What features are sim-
ilar between these ‘‘cemented carbides’’ and pearlite, a microconstituent in
steels? What are some of the major di¤erences?
SOLUTION
Pearlite is very similar to the tungsten carbide-cobalt (WC-Co) composites
known in industry as carbides. You may recall from earlier chapters that WC-
Co are ceramic-metal composites (known as cermets) and used as cutting tools,
drill bits, etc. In both materials, we take advantage of the toughness of one
phase (ferrite or cobalt metal, in the case of pearlite in steel and WC-Co, respec-
tively) and the hard ceramic-like phase (WC and Fe
3
C, in WC-Co and steel,
respectively). The metallic phase helps with ductility and the hard phase helps
with strength. The di¤erence is, WC and Co are two separate compounds that
are sintered together using the powder metallurgy route. Pearlite is a micro-
constituent made up of two phases derived from same two elements (Fe-C).
Another di¤erence is in pearlite, the phases are formed via a eutectoid reaction.
No such reaction occurs in the formation of WC-Co composites. Typically,
WC-Co microstructure consists mainly of WC grains that are ‘‘glued’’ by co-
balt grains. In pearlite, the metal-like ferrite phase dominates.
Primary Microconstituents Hypoeutectoid steels contain less than 0.77% C, and hy-
pereutectoid steels contain more than 0.77% C. Ferrite is the primary or proeutectoid
microconstituent in hypoeutectoid alloys, and cementite is the primary or proeutectoid
microconstituent in hypereutectoid alloys. If we heat a hypoeutectoid alloy containing
0.60% C above 750
C, only austenite remains in the microstructure. Figure 12-13 shows
what happens when the austenite cools. Just below 750
C, ferrite nucleates and grows,
usually at the austenite grain boundaries. Primary ferrite continues to grow until the
temperature falls to 727
C. The remaining austenite at that temperature is now sur-
rounded by ferrite and has changed in composition from 0.60% C to 0.77% C. Sub-
sequent cooling to below 727
C causes all of the remaining austenite to transform
to pearlite by the eutectoid reaction. The structure contains two phases—ferrite and
cementite—arranged as two microconstituents—primary ferrite and pearlite. The
final microstructure contains islands of pearlite surrounded by the primary ferrite [Figure
12-14(a)]. This structure permits the alloy to be strong, due to the dispersion-strengthened
pearlite, yet ductile, due to the continuous primary ferrite.
In hypereutectoid alloys, the primary phase is Fe
3
C, which forms at the austenite
grain boundaries. After the austenite cools through the eutectoid reaction, the steel
contains hard, brittle cementite surrounding islands of pearlite [Figure 12-14(b)].
Now, because the hard, brittle microconstituent is continuous, the steel is also brittle.
12-9 The Eutectoid Reaction 373