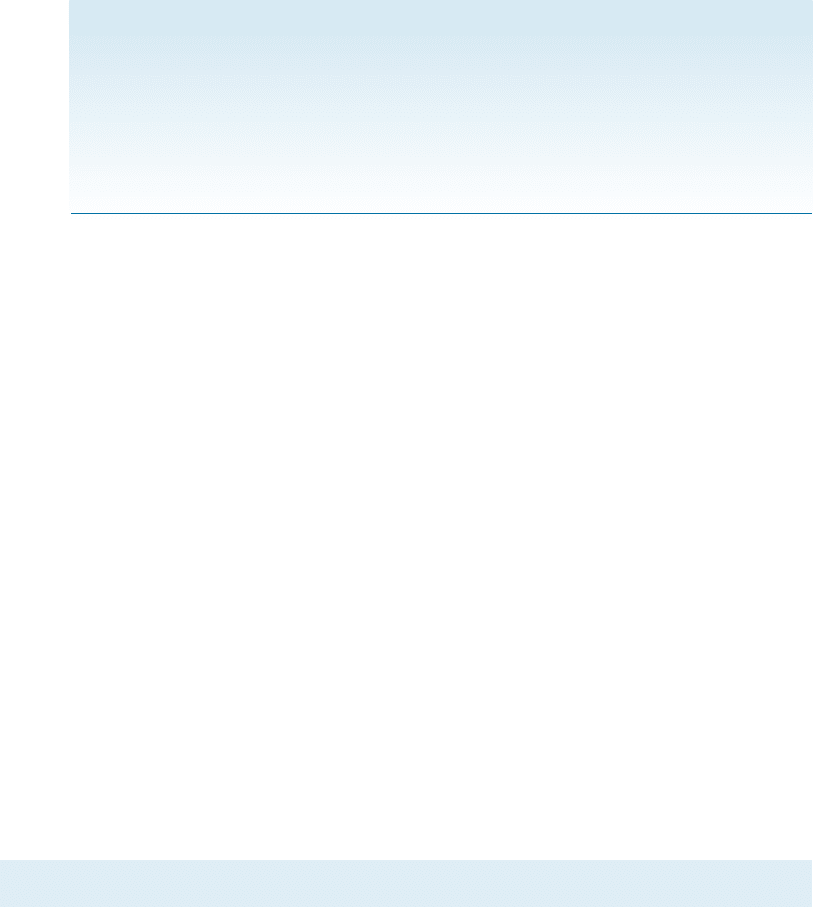
SOLUTION
Step 1: Solution-trea t at a temperature between the solvus and the eutectic to
avoid hot shortness. Thus, heat between 340
C and 451
C (Figure 12-8).
Step 2: Quench to room temperature fast enough to prevent the precipitate
phase b from forming.
Step 3: Age at a temperature below the solvus, that is, below 340
C, to form a
fine dispersion of b phase.
Nonequilibrium Precipitates during Aging During aging of aluminum-copper alloys,
a continuous series of other precursor precipitate phases forms prior to the formation of
the equilibrium y phase. This is fairly common in precipitation-hardened alloys. The
simplified diagram in Figure 12-7 does not show these intermediate phases. At the start
of aging, the copper atoms concentrate on f100g planes in the a matrix and produce
very thin precipitates called Guinier-Preston (GP) zones. As aging continues, more
copper atoms di¤use to the precipitate and the GP-I zones thicken into thin disks, or
GP-II zones. With continued di¤usion, the precipitates develop a greater degree of
order and are called y
0
. Finally, the stable y precipitate is produced.
The nonequilibrium precipitates—GP-I, GP-II, and y
0
—are coherent precipitates.
The strength of the alloy increases with aging time as these coherent phases grow in size
during the initial stages of the heat treatment. When these coherent precipitates are
present, the alloy is in the aged condition. This important development in the micro-
structure evolution of precipitation-h ardened alloys is the reason the time for heat
treatment during aging is very important. Since the changes in the structure occur at a
nano-scale, no change is seen in the structure of the alloy at a micro-s cale. This is one
reason why the mechanisms of precipitation hardening were established more firmly
only in the 1950s, (when electron microscopes were starting to be used), even though
the phenomenon was discovered earlier.
When the stable noncoherent y phase precipitates, the strength of the alloy begins
to decrease. Now the alloy is in the overaged condition. The y phase still provides some
dispersion strengthening, but with increasing time, the y phase grows larger and even
the simple dispersion-strengthening e¤ect diminishes.
12-6 Effects of Aging Temperature and Time
The properties of an age-hardenable alloy depend on both aging temperature and aging
time (Figure 12-9). At 260
C, di¤usion in the Al-4% Cu alloy is rapid, and precipitates
quickly form. The strength reaches a maximum after less than 0.1 h (6 minutes) ex-
posure. Overaging occurs if the alloy is held for longer than 0.1 h.
At 190
C, which is a typical aging temperature for many aluminum alloys, a longer
time is required to produce the optimum strength. However, there are benefits to using
the lower temperature. First, the maximum strength increases as the aging temperature
decreases. Second, the alloy maintains its maximum strength over a longer period of
time. Third, the properties are more uniform. If the alloy is aged for only 10 min at
260
C, the surface of the part reaches the proper temperature and strengthens, but the
center remain s cool and ages only slightly. The example that follows illustrates the e¤ect
of aging heat treatment time on the strength of aluminum alloys.
12-6 Effects of Aging Temperature and Time 367