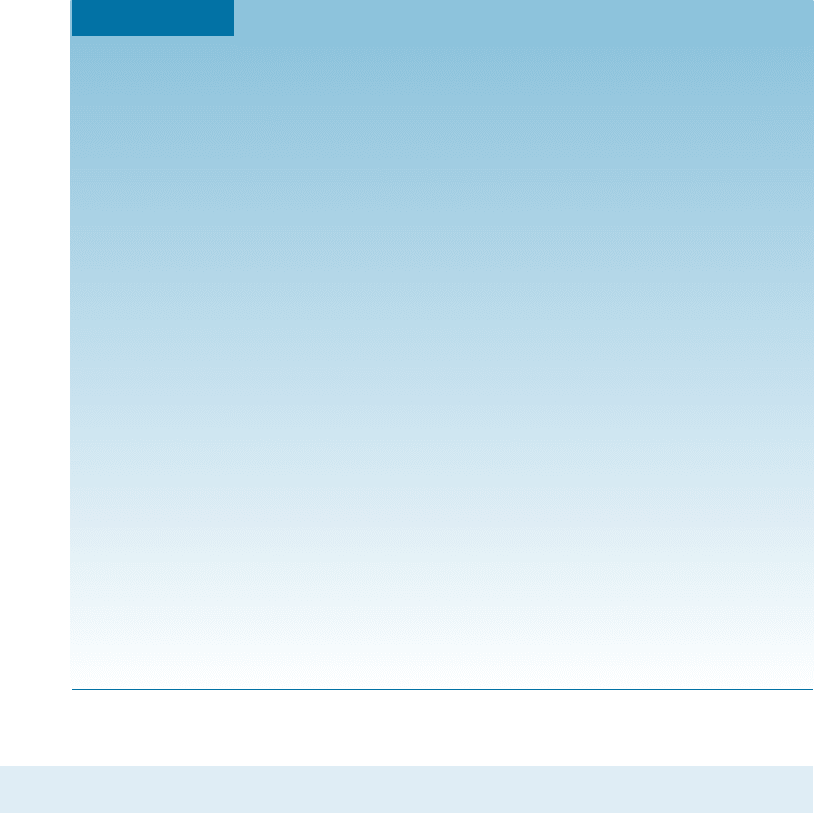
EXAMPLE 14-7 Design/Materials Selection for a High-Performance Jet Engine
Turbine Blade
Design a nickel-based superalloy for producing turbine blades for a gas turbine
aircraft engine that will have a particularly long creep-rupture time at temper-
atures approaching 1100
C.
SOLUTION
First, we need a temperature stable microstructure. Addition of aluminum or
titanium permits the precipitation of up to 60 vol% of the g
0
phase during heat
treatment and may permit the alloy to operate at temperatures approaching
0.85 times the absolute melting temperature. Addition of carbon and alloying
elements such as Ta and Hf permits the precipitation of alloy carbides that pre-
vent grain boundaries from sliding at high temperatures. Other alloying elements,
including molybdenum and tungsten, provide solid-solution strengthening.
Second, we might produce a directionally solidified or even single-crystal
turbine blade (Chapter 9). In directional solidification, only columnar grains
form during freezing, eliminating transverse grain boundaries that might
nucleate cracks. In a single crystal, no grain boundaries are present. We might
use the investment casting process, being sure to pass the liquid superalloy
through a filter to trap any tiny inclusions before the metal enters the ceramic
investment mold.
We would then heat treat the casting to assure that the carbides and g
0
precipitate with the correct size and distribution. Multiple aging temperatures
might be used to assure that the largest possible volume percent g
0
is formed.
Finally, the blade might contain small cooling channels along its length. Air
for combustion in the engine can pass through these channels, providing active
cooling to the blade, before reacting with fuel in the combustion chamber.
14-5 Titanium Alloys
Titanium is traditionally produced from TiO
2
by the Kroll process. The TiO
2
is con-
verted to TiCl
4
(titanium tetra chloride, also informally known as tickle!), which is
subsequently reduced to titanium metal by sodium or magnesium. The resultant tita-
nium sponge is then consolidated, alloyed as necessary, and processed using vacuum
arc melting. Recently, a new electrochemical process for the production of titanium
sponge directly from TiO
2
has been reported. Titanium provides excellent corrosion
resistance, high specific strength, and good high-temperature properties. Strengths up to
1380 MPa, coupled with a density of 4.505 g/cm
3
, provide excellent mechanical prop-
erties. An adherent, protective TiO
2
film provides excellent resistance to corrosion and
contamination below 535
C. Above 535
C, the oxide film breaks down and small
atoms such as carbon, oxygen, nitrogen, and hydrogen embrittle the titanium.
Titanium’s excellent corrosion resistance provides applications in chemical process-
ing equipment, marine components, and biomedical implants such as hip prostheses.
Titanium is an important aerospace material, finding applic ations as airframe and jet
engine components. When it is combined with niobium, a superconductive intermetallic
compound is formed; when it is combined with nickel, the resulting alloy displays the
CHAPTER 14 Nonferrous Alloys454