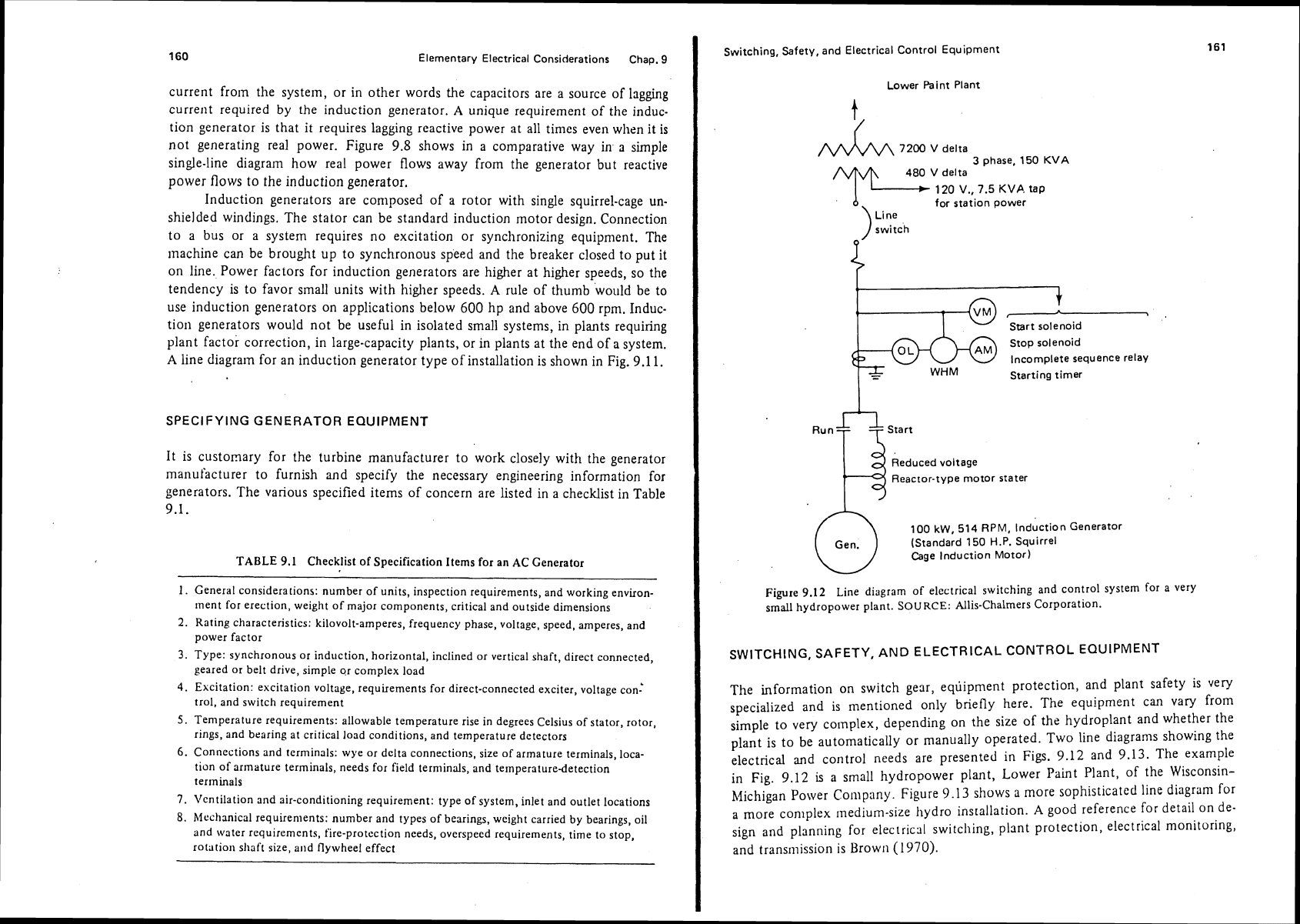
160
Elementary Electrical Considerations Chap.
9
current from the system, or in other words the capacitors are a source of lagging
current required by the induction generator.
A
unique requirement of the induc-
tion generator is that it requires lagging reactive power at all
times even when it is
not generating real power. Figure 9.8 shows in a comparative way in
a
simple
single-line diagram how real power flows away from the generator but reactive
power flows to the induction generator.
Induction generators are composed of a rotor with single squirrel-cage
un-
shielded windings. The stator can be standard induction motor design. Connection
to a bus or a system requires no excitation or synchronizing equipment. The
machine can be brought up to synchronous speed and the breaker closed to put
it
on line. Power factors for induction generators are higher at higher speeds, so the
tendency is to favor small units with higher speeds.
A
rule of thumb would be to
use induction generators on applications below
600
hp and above
600
rpm. Induc-
tion generators would not be useful in isolated small systems, in plants requiring
plant factor correction, in large-capacity plants, or in plants at the end of a system.
A
line diagram for an induction generator type of installation is shown in Fig. 9.1 1.
SPECIFYING GENERATOR EQUIPMENT
It is customary for the turbine manufacturer to work closely with the generator
manufacturer to furnish and specify the necessary engineering information for
generators. The various specified items of concern are listed in a checklist in Table
9.1.
TABLE 9.1 Checklist of Specification Items for an AC Generator
1.
General considerations: number of units, inspection requirements, and working environ-
ment for erection, weight of major components, critical and outside dimensions
2. Rating characteristics: kilovolt-amperes, frequency phase, voltage, speed, amperes, and
power factor
3.
Type: synchronous or induction, horizontal, inclined or vertical shaft, direct connected,
geared or belt drive, simple
gr complex load
4.
Excitation: excitation voltage, requirements for direct-connected exciter, voltage con:
trol, and switch requirement
5.
Temperature requirements: allowable temperature rise in degrees Celsius of stator, rotor,
rings, and bearing at critical load conditions, and temperature detectors
6.
Connections and terminals: wye or delta connections, size of armature terminals, loca-
tion of armature terminals, needs for field terminals, and temperature-detection
terminals
7.
Ventilation
and air-conditioning requirement: type of system, inlet and outlet locations
8.
hfechanical requirements: number and types of bearings, weight carried by bearings, oil
and
water requirements, fire-protection needs, overspeed requirements, time to stop,
rotation sliaff size, and flywheel effect
Switching, Safety, and Electrical Control Equipment
Lower Paint Plant
4-
7200
V
delta
3
phase. 150
KVA
480
V
delta
1
120
V.,
7.5
KVP.
tap
for station power
\
Line
)
switch
?
w
Start solenoid
stop solenoid
Incomplete sequence relay
Starting timer
Run
start
.#'
Reduced voltage
Reactor-type motor stater
100
kW,
514 RPM, Induction Generator
(Standard 150
H.P.
Squirrel
Cage Induction Motor)
Figure 9.12 Line diagram of electrical switching and control system for a very
small hydropower plant.
SOURCE:
Allis-Chalmers Corporation.
SWITCHING, SAFETY, AND ELECTRICAL CONTROL EQUIPMENT
The information on switch gear, equipment protection, and plant safety is very
specialized and is mentioned only briefly here. The equipment can vary from
simple to very complex, depending on the size of the hydroplant and whether the
plant is to be automatically or manually operated. Two line
diagrams showing the
electrical and control needs are presented in Figs.
9.12
and 9.13. The example
in Fig.
9.12
is
a small hydropower plant, Lower Paint Plant, of the Wisconsin-
hlichigan Power Company. Figure 9.13 shows a more sophisticated line diagram for
a
more conlplex medium-size hydro installation.
A
good reference for detail on de-
sign and planning for electrical switching, plant
protection,
electrical monitoring,
and transmission
is Brown (1970).