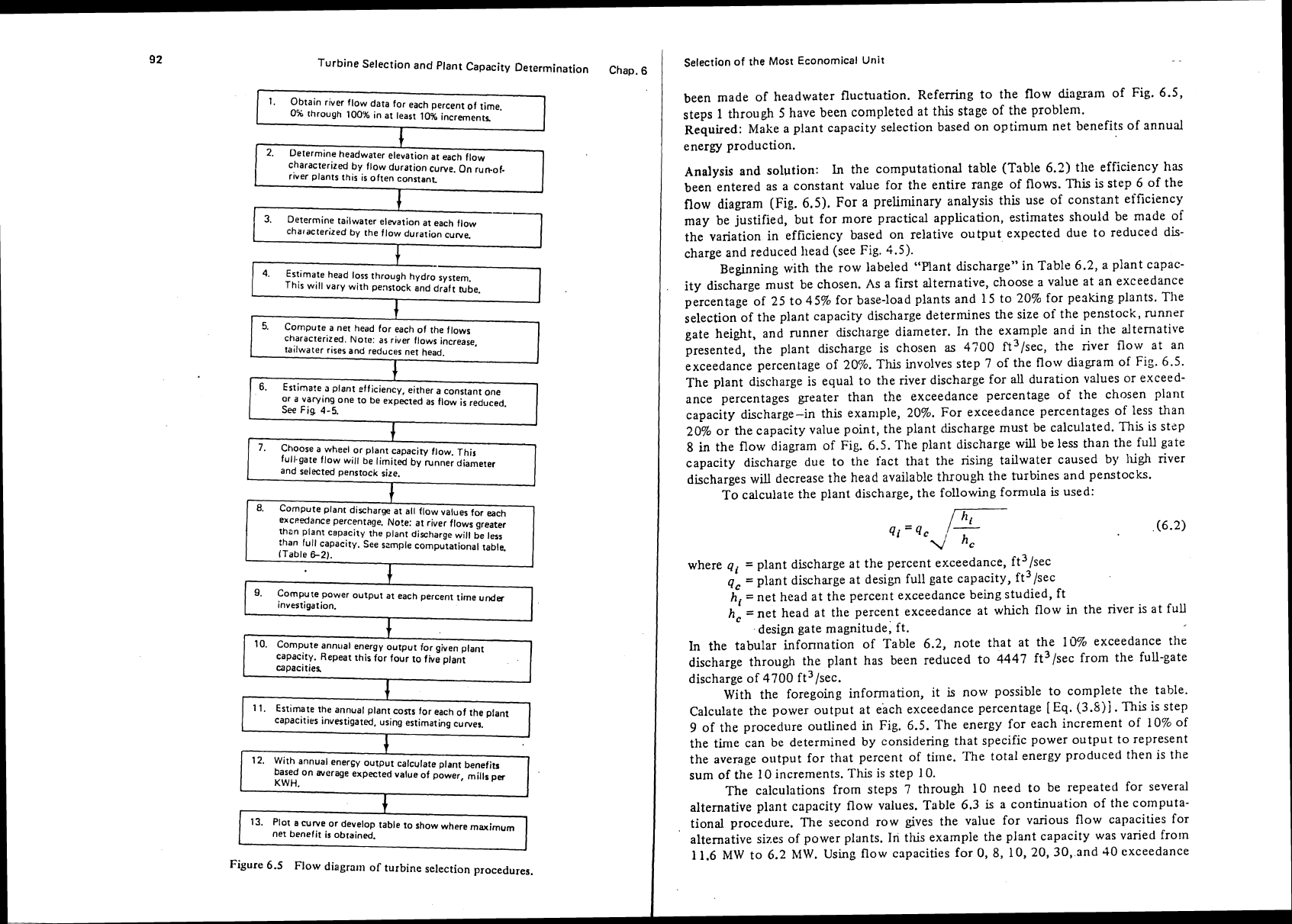
Turbine Selection and Plant Capacity Determination
1.
Obtain river flow data for each percent of time.
0%
through
100%
in at least
10%
increments
1
1
2.
Determine headwater elevation at each flow
characterized by flow duration curve. On
ruwoF
river plants this is often constant
1
3.
Determine tailwater elevation at each flow
characterized by the flow duration curve.
Estimate head loss through hydro system.
This will vary with penstock and draft tube.
characterized.
Note: as river flows increase,
t
6.
Ertina!e
a
plant efficiency, either a constant one
or a varying one to be expected as flow is reduced.
See
Fig
4-5.
f
7.
Choose a wheel or plant capacity flow. This
full-gate flow will be limited by runner diameter
and selected penstock sire.
I
exceedance percentage. No!e: at river flows greater
than plant capacity the plant
discharge will be less
than full capacity. See
szmple computational table.
(Table
62).
9.
Compute power output at each percent time
under
investigation.
I
Figure
6.5
Flow
diagmrn
of
turbine
selection
procedures.
Chap.
E
Selection of the Most Economical Unit
. .
been made of headwater fluctuation. Referring to the flow diagram of Fig.
6.5,
steps 1 through
5
have been completed at this stage of the problem.
Required: Make a plant capacity selection based on optimum net benefits of annual
energy production.
Analysis and solution:
ln
the computational table (Table
6.2)
tlie efficiency has
been entered as a constant value for the entire range of flows.
This
is step
6
of the
flow diagram
(Fig.
6.5).
For
a preliminary analysis this use of constant efficiency
may be justified, but for more
practical application, estimates should be made of
the variation in efficiency based on relative output expected due to reduced dis-
charge and reduced
head (see Fig.
4.5).
Beginning with the row labeled "Rant discharge" in Table
6.2,
a plant capac-
ity discharge must be chosen. As a first alternative, choose a value at an exceedance
percentage of
25
to
45%
for base-load plants and 15 to 20% for peaking plants. The
selection of the plant capacity discharge determines the size of the penstock, runner
gate height, and runner discharge diameter. In the example and
in
the alternative
presented, the plant discharge is chosen
as
4700 f13/sec, the river flow at an
exceedance percentage of
20%.
This
involves step
7
of the flow diagram of Fig.
6.5.
The plant discharge is equal to the river discharge for all duration values or exceed-
ance percentages greater than the exceedance percentage of the chosen plant
capacity discharge-in this
example, 20%. For exceedance percentages of less than
20%
or the capacity value point, the plant discharge must be calculsted.
This
is step
8
in
the flow diagram of Fig.
6.5.
The plant discharge will be less than the full gate
capacity discharge due to the fact that the rising tailwater caused by
high
river
discharges
will
decrease the head available through the turbines and penstocks.
To calculate the plant discharge, the following formula
is
used:
where
qi
=
plant discharge at the percent exceedance, ft3/sec
qc
=plant discharge at design full gate capacity, ft3/sec
hi
=
net head at the percent exceedance being studied, ft
h,
=net head at the percent exceedance at which flow in the river is at full
design gate magnitude; ft.
In the tabular infonnation of Table
6.2,
note that at the 1070 exceedance the
discharge through the plant has been reduced to 4447 ft3/sec from the full-gate
discharge of 4700 ft3/sec.
With the foregoing
information, it
is
now possible to complete the table.
Calculate the power output at
each exceedance percentage [Eq.
(3.S)j.
This
is step
9
of the procedure outlined in Fig.
6.5.
The energy for each increment of
10%
of
the time can be determined by considering that specific power output to represent
the average output for that percent of
tirne. The total energy produced then is the
sum of the 10 increments.
This
is step 10.
The calculations from steps
7
through 10 need to be repeated for several
alternative plant capacity flow values. Table 6.3 is a continuation of the
cornputa-
tional procedure. The second row gives the value for vaious
flow
capacities for
alternative
sizes of power plants. In this example the plant capacity was varied from
11.6 MW to
6.2
hlW.
Using flow capacities for
0,
8,
10,
20,
30, and 40 exceedance