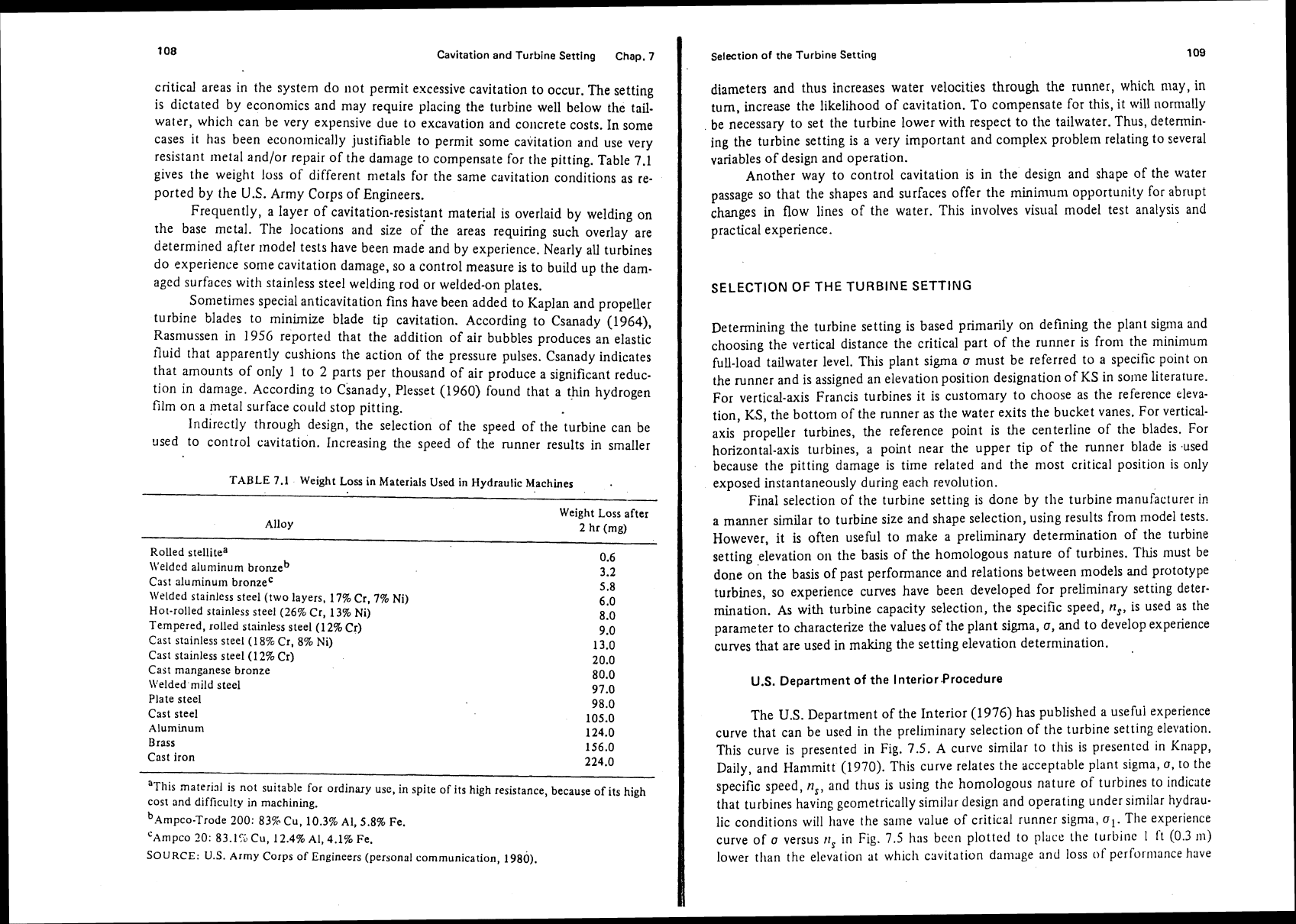
108
Cavitation
and
Turbine Setting Chap.
7
critical areas in the system do not permit excessive cavitation to occur. The setting
is dictated by
econonlics and may require placing the turbine well below the tail-
water, which can be very expensive due to excavation and collcrete costs. In some
cases it has been
economically
justifiable to permit some cavitation and use very
resistant metal and/or repair of the damage to compensate for
the pitting. Table 7.1
gives the weight loss of different
nietals for the same cavitation conditions as
re-
ported by the
U.S.
Army Corps
of
Engineers.
Frequently, a layer of cavitation-resistant material is overlaid by welding on
the base metal. The locations and size of the areas requiring such overlay are
dzterrnined after
model tests have been made and by experience. Nearly all turbines
do experience
some cavitation damage, so a control measure
is
to build up the darn-
a2cd surfaces with stainless steel welding rod or welded-on plates.
Sometimes special anticavitation fins have been added to Kaplan and propeller
turbine blades to minimize blade tip cavitation. According to Csanady
(1964),
Rasn~ussen in 195G reported that the addition of air bubbles produces an elastic
fluid that apparently cushions the action of the pressure pulses. Csanady indicates
that amounts of only 1 to
2
parts per thousand of air produce a significant reduc-
tion in damage. According to Csanady, Plesset (1960) found that a thin hydrogen
film on a
~netal surface could stop pitting.
Indirectly through design, the selection of the speed of the turbine can be
~lsed to control cavitation. Increasing the speed of the runner results in smaller
TABLE 7.1 Weight Loss in Materials Used in Hydraulic Machines
.
-
Weight Loss after
Alloy
2 hr (mg)
Rolled stellitea
0.6
\Veldcd alunlinum bronzeb
3.2
Cast aluminum bronzeC
5.8
Welded stainless steel (two layers, 17% Cr, 7% Ni)
6.0
Hot-rolled stainless steel (26% Cr, 13% Ni)
8.0
Tempered, rolled stainless steel (12%
Cr)
9.0
Cast stainless steel
(18%
Cr,
8%
Ni)
13.0
Cast stainless steel (12% Cr)
20.0
Cast manganese bronze
80.0
\\'elded mild steel
97.0
Plate steel
98.0
Cast steel
105.0
Aluminum
124.0
Brass 156.0
Cast iron
224.0
"This
materid is not suitable for ordinary use, in spite of its high resistance, because of its high
cost and difficulty in machining.
b.4mpco-~rode 200: 83% Cu, 10.3% Al, 5.8% Fe.
'Ampco 20: 83.15 cu, 12.4% Al, 4.1% Fe.
SOURCE:
U.S.
Army Corps of Engineers (personal communication, 1980).
Selection
of
the
Turbine Setting
109
diameters and thus increases water velocities through the runner, which may, in
turn, increase the likelihood of cavitation. To compensate for this, it will normally
be necessary to set the turbine lower with respect to the tailwater. Thus, detennin-
ing the turbine setting is a very important and complex problem relating to several
variables of design and operation.
Another way to control cavitation is in the design and shape of the water
passage so that the shapes and surfaces offer
the minimum opportunity for abrupt
changes in flow lines of the water. This involves visual model test analysis and
practical experience.
SELECTION OF THE TURBINE SETTING
Determining the turbine setting is based primarily on defining the plant signla and
choosing the vertical distance the critical part of the runner is
from the minimum
full-load tailwater level. This plant sigma
o
must be referred to a specific point on
the runner and is assigned an elevation position designation of KS in
some literature.
For vertical-axis Francis turbines it is customary to choose as the reference eleva-
tion,
KS,
the bottom of the runner as the water exits the bucket vanes. For vertical-
axis propeller turbines, the reference point is the centerline of the blades. For
horizontal-axis turbines, a point near the upper tip of the runner blade is
.used
because the pitting damage is time related and the most critical position is only
exposed instantaneously during each revolution.
Final selection of the turbine setting is done by the turbine manufacturer in
a manner similar to turbine size and shape selection, using results from model tests.
However, it is often useful to make a preliminary determination of the turbine
setting elevation on the basis of the homologous nature of turbines.
This must be
done on the basis of past
performance and relations between models and prototype
turbines, so experience curves have been developed for preliminary
setring deter-
mination. As with turbine capacity selection, the specific speed,
n,,
is used as the
parameter to characterize the values of the plant sigma,
a,
and to develop experience
curves that are used in making the setting elevation determination.
U.S.
Department of the Interior Procedure
The
U.S.
Department of the Interior (1976) has published a usefui experience
curve that can be used in the preliminary selection of the turbine setting elevation.
This curve is presented in Fig. 7.5.
A
curve similar to this is presented in Knapp,
Daily, and
Hammitt (1970). This curve relates the acceptable plant sigma,
o,
to the
specific speed,
n,,
and thus is using the homologous nature of turbines to indicate
that turbines having geometrically similar design and operating under similar hydrau-
lic conditions will
have the same value of critical runner sigma,
a,.
The experience
curve of
a
versus
r~,
in Fig. 7.5 h:is bccn plotted to place the lurbinc
1
ft
(0.3 ~n)
lower than the elevation at which cavitation damage and loss
of
performance have