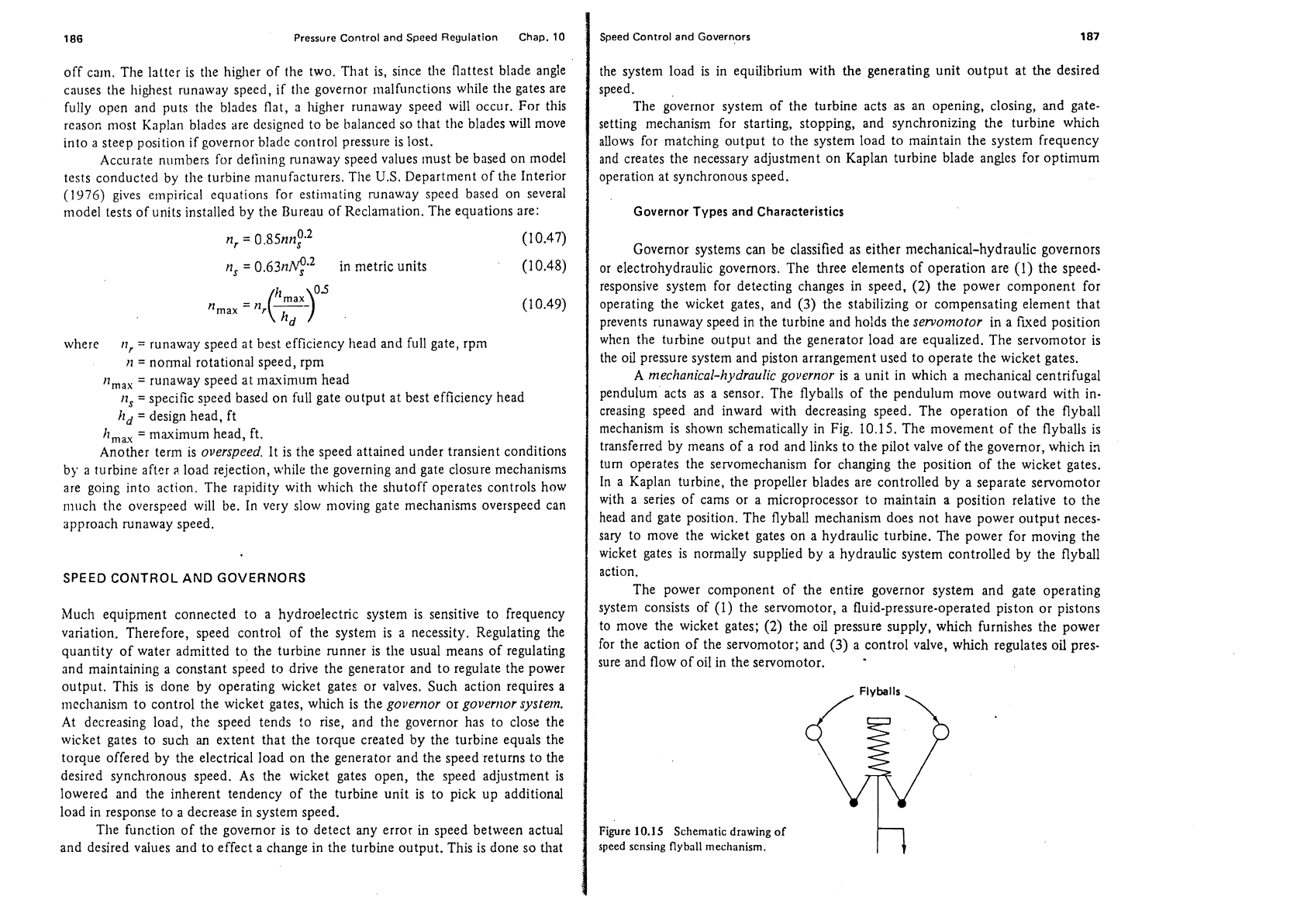
186
Pressure Control and Speed Regulation Chap.
10
Speed Control and Governors
187
off cam. The latter is the higher of the two. That is, since the flattest blade angle
causes the highest runaway speed, if the governor
~iialfunctions wliile the gates are
fully open and puts the blades flat, a
higher runaway speed will occur. For this
rcasor, most Kaplan blades are designed to be balanced so that the blades will move
into a steep position if governor blade control pressure is lost.
Accurate
numbers for defining runaway speed values must be based on model
tests conducted by the turbine manufacturers. The
U.S.
Department of the Interior
(1976)
gives empirical equations for esti~nating runaway speed based on several
model tests of units installed by tlie Bureau of Reclamation. The equations are:
n,
=
0.85nnf.~
(10.47)
n,
=
0.63ne2
in rnetric units
where
11,
=
runaway speed at best efficiency head and full gate, rpin
n
=
nonnal rotational speed, rpm
rim,,
=
runaway speed at ~nauimum head
11,
=
specific speed based on full gate output at best efficiency head
hd
=
design head, ft
h,,
=
maximum head, ft.
Another term is
overspeed.
It is the speed attained under transient conditions
by a turbine after
;l
load rejection, while tlie governing and gate closure mechanisms
are going into action. The rapidity with which the shutoff operates controls how
much the
overspced will be. In very slow moving gate mechanisms overspeed can
approach runaway speed.
SPEED
CONTROL
AND
GOVERNORS
Much equipment connected to a hydroelectric system is sensitive to frequency
variation. Therefore, speed control of the system is a necessity. Regulating the
quantity of water admitted to the turbine runner is the usual means of regulating
and maintaining a constant speed to drive the generator and to regulate the power
output. This is done by operating wicket
gates or valves. Such action requires a
mechanism to control the wicket gates,
wluch is the
govertzor
or
govertlor system.
At decreasing load, the speed tends to rise, and tlie governor has to close the
wicket gates to such an extent that the torque created by the turbine equals the
torque offered by the electrical load on the generator and the speed returns to the
desired synchronous speed. As the wicket gates open, the speed adjustment is
lowered and the inherent tendency of the turbine unit is to pick up additional
load in response to a decrease in system speed.
The function of the governor is to detect any error in speed between actual
and desired values and to effect a change in the turbine output. This is done so
that
the system load is in equilibrium with the generating unit output at the desired
speed.
The governor system of the turbine acts as an opening, closing, and
gate-
setting mechanism for starting, stopping, and synchronizing the turbine which
allows for matching output to the system load to maintain the system frequency
and creates the necessary adjustment on Kaplan turbine blade angles for optimum
operation at synchronous speed.
Governor Types and Characteristics
Governor systems can be classified as either mechanical-hydraulic governors
or electrohydraulic governors. The three elements of operation are (1) the
speed-
responsive system for detecting changes in speed,
(2)
the power component for
operating the wicket gates, and
(3)
the stabilizing or compensating element that
prevents runaway speed in the turbine and holds the
servomotor
in a ftved position
when the turbine output and the generator load are equalized. The servomotor is
the oil pressure system and piston arrangement used to operate the wicket gates.
A
mechanical-hydraulic governor
is a unit in which a mechanical centrifugal
pendulum acts as a sensor. The
flyballs of the pendulum move outward with in-
creasing speed and inward with decreasing speed. The operation of the
flyball
mechanism is shown schematically in Fig.
10.15.
The movement of the flyballs is
transferred by means of a rod and links to the pilot valve of the governor, which
in
turn operates the servomechanism for changing the position of the wicket gates.
In a Kaplan turbine, the propeller blades are controlled by a separate servomotor
with a series of cams or a microprocessor to maintain a position relative to the
head and gate position. The
flyball mechanism does not have power output neces-
sary to move the wicket gates on a hydraulic turbine. The power for moving the
wicket gates is normally supplied by a hydraulic system controlled by the
flyball
action.
The power component of the entire governor system and gate operating
system consists of
(1)
the servomotor, a fluid-pressure-operated piston or pistons
to move the wicket gates;
(2)
the oil pressure supply, which furnishes the power
for the action of the servomotor; and
(3)
a control valve, which regulates oil pres-
sure and flow of oil in the servomotor.
Figure
10.15
Schematic drawing of
speed sensing
flyball
mechanism.
h