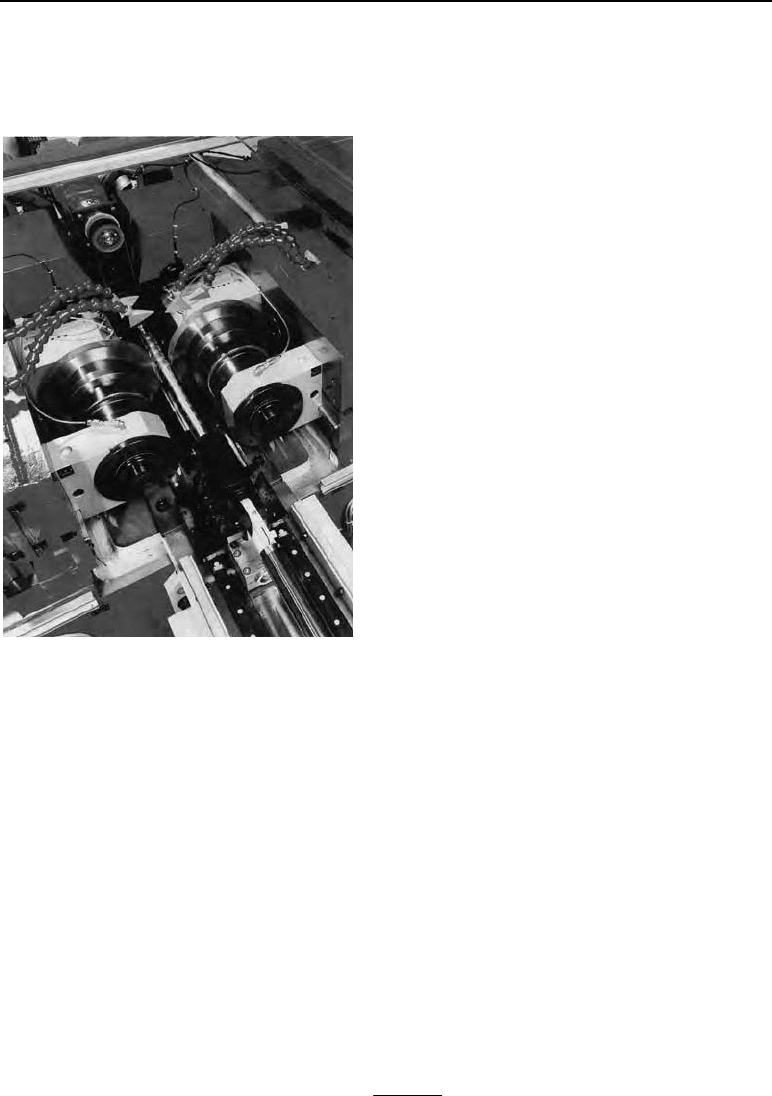
6.10 Methods and machines for rolling gears 75
Two main spindles, driven synchronously in the same direction, are used to take up the rolling
dies. One of the two rolling spindles is fixed, the other is moved mechanically or hydraulically
so that the rolling dies penetrate the rotationally symmetric blank.
Using CNC control it is possible to control
and visualise the processing of the values
involved in the rolling and their functions,
in a reproducible manner.
When rolling large profile depths with
cylindrical dies, forces of up to 800 kN can
be used in the deformation (PRZ80, Profi-
roll, Bad Düben, Germany). Gear tooth
profiles with a standard modulus are for-
med using forces in the region of 200 kN
depending on the workpiece.
Figure 6.24
The working area of a two-die machine (Profi-
roll Technologies, Bad Düben, Germany)
6.10.4 Rolling defects in processing
During the rolling process, the complicated kinematics mean that the following rolling defects
typical to the rolling of gear teeth profiles occur:
– undercut in the tooth root area of the gear,
– deviations in the shape of the flank,
– deviations in the flank alignment,
– spacing defects,
– deviations in radial runout.
Radial runout, spacing, flank shape and alignment affect the quality of the rolled part and the
optimising of the gear tooth profile.
6.10.4. a) Undercut in the gear tooth root area
Undercut occurs in the gear tooth root area if the tooth number limit, t
L
, is not reached in the
profile to be rolled.
– at an engagement angle of
D
0
= 20°:
L
2
0
2
sin
t
a