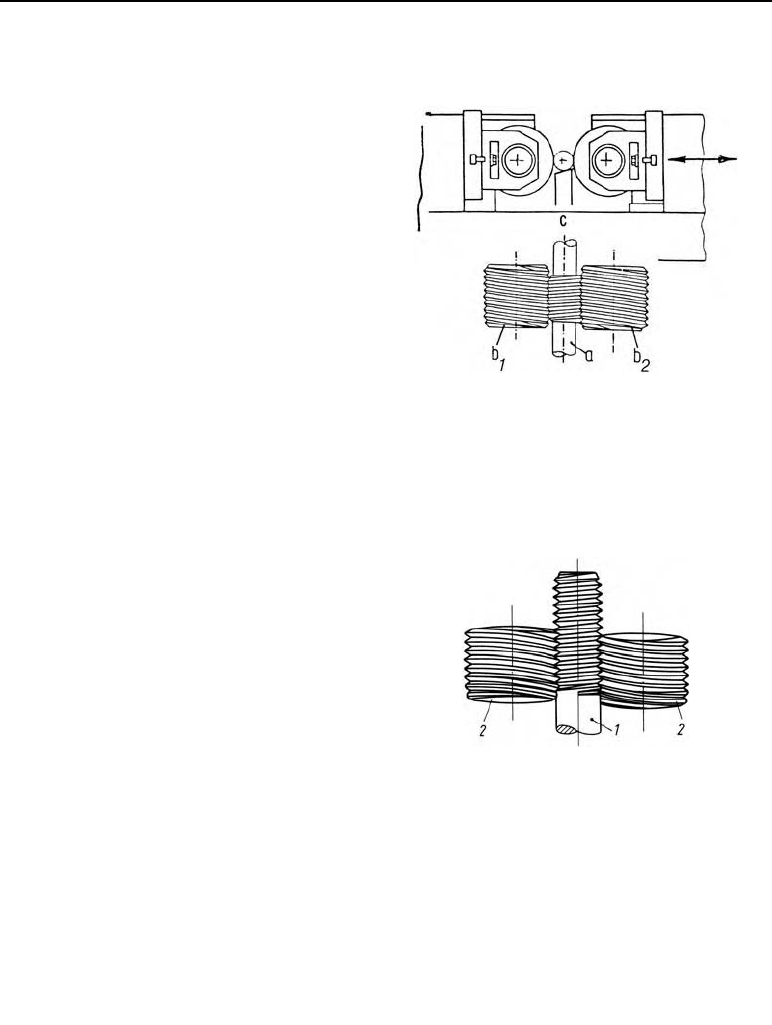
57
6.1.2 Dies with infinite work surfaces
a) Infeed process (Figure 6.3)
In the infeed process, the profile grooves
of the rolls have the pitch of the thread to
be produced. The rolls, driven at the same
speed, move in the same direction. Dur-
ing rolling, the workpiece moves due to
friction with no axial shifting. As the
thread produced by this means is an exact
copy of the rolling dies, threads of this
kind have a very high pitch accuracy. The
maximum length of the thread is limited
by the width of the rollers (30-200 mm).
Figure 6.3
Arrangement of the workpiece and the
tools during infeed process,a) work
iece,
b) dies, b
1
fixed, b
2
adjustable die, c)
work rest
b) Through-feed method (Figure 6.4)
Here, the rolling dies have grooves with
no pitch; the groove cross section is that
of the standard flank profile. The thread
pitch is produced by skewing the die axes
by the pitch angle of the thread. By this
means the workpiece is given an axial
thrust and moves one pitch length in axial
direction for every full revolution. As the
axial thrust kicks in immediately when
the workpiece enters the assembly, larger
threads are not formed to full depth in
one pass.
Figure 6.4
Arrangement of the workpiece and the
dies during the through-feed method
1 workpiece, 2 dies
c) Combined infeed-through-feed method
The combined infeed-through-feed method is a combination of both basic methods.
– Slow axial penetration with axial movement of the workpiece,
– change of direction of rotation when final axial position is reached
– process repeated until the required thread depth is achieved.