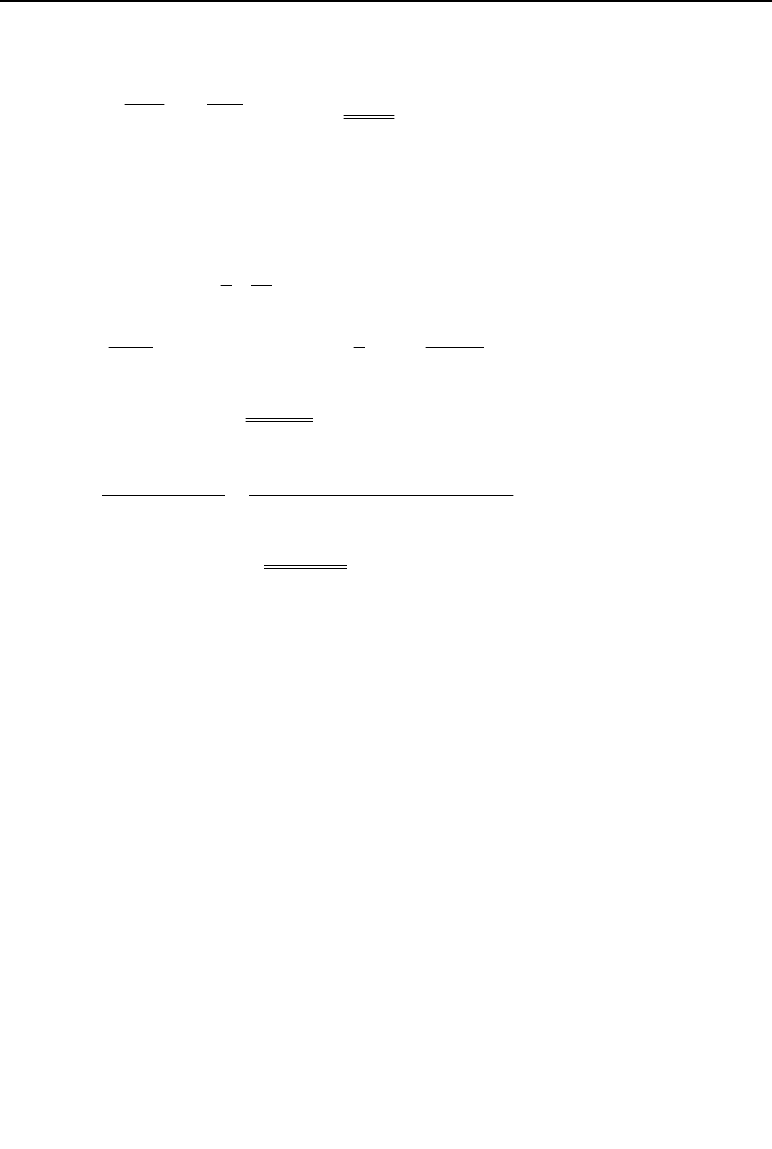
5.13 Shape classification 49
5. Upsetting (heading)
5.1
M
p
= ln
HD0
HD
66.1
ln 0.384 38.4%
45
h
h
o
M
p
= 150 %.
5.2
k
str
0
= 280, k
str
1
= 670, k
str
m
= 475 N/mm
2
5.3
F = A
1
· k
str
1
1
1
1
1
3
d
h
P
§·
¨¸
©¹
=
2
22
50 ʌ 150mm
mm 670 N/mm 1 0.15
4345mm
§·
¨¸
©¹
F = 1 387 896.7 N = 1388 kN
5.4 W =
m
32
HD str p
F
63617 mm 475 N / mm 0.384
0.7
Vk
M
K
W = 16 576 771 Nmm = 16.6 kN m
5.13 Shape classification
For operations scheduling, during which the sequence of operations plans for the extrusions
are produced, it is important to collect and record empirical values.
This is why a shape classification table is used in which the various extrusion shapes are or-
dered according to operating method, sequence of operations, degree of difficulty etc. Table
5.6 shows a shape classification table. The advantages of this kind of classification are:
– Production of sequence of operations plans for new parts.
If sequence of operations plans already exist in the shape classification table for similar
parts, this makes the production of a new sequence of operations plan easier as it can be ba-
sed on similar shapes.
This means the induction of new inexperienced workers is made far simpler and the need
for specialists is reduced.
– Furthermore, groups of the same shape have the same or a similar amount of difficulty
during pressing.
Depending on the group of shapes, the extent of the deformation efficiency to be expected
can also be deduced (see Table 5.7).
– There are also advantages for tool manufacture. Similar shapes also produce similar ele-
ments as concerns tools; these elements can be standardised within a company, simplified
and thus produced at less expense.