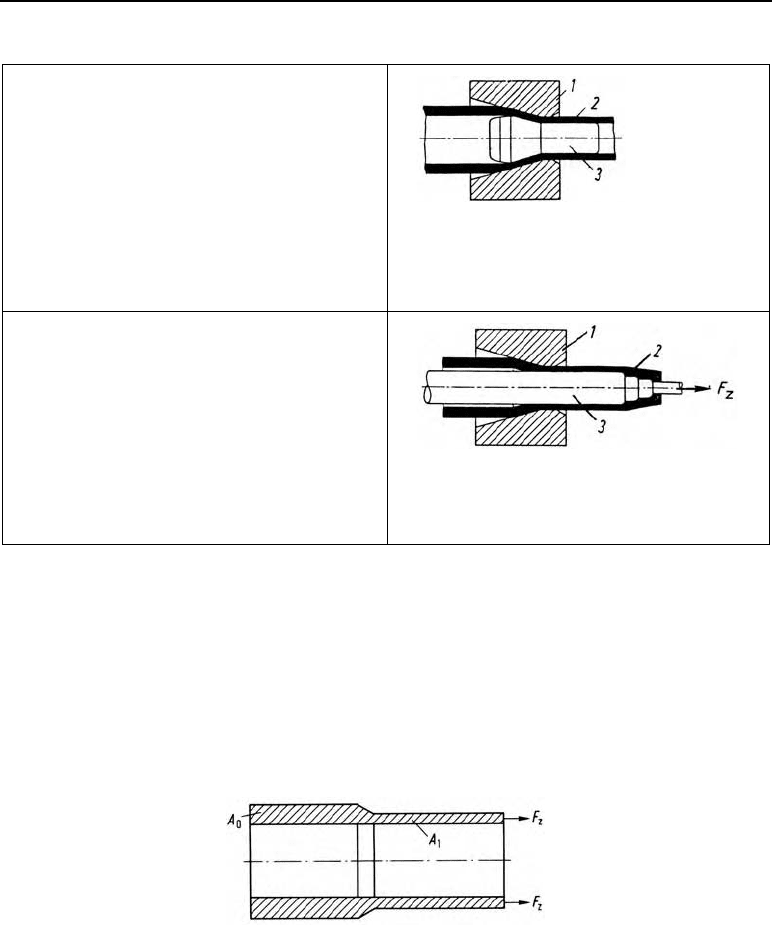
106 11 Tube drawing
Table 11.1 Tube drawing process (continued)
Drawing over a floating plug
The set-up is the same as with plug drawing.
Here, however, the plug is not attached to a man-
drel, but is pushed in before drawing takes place.
Because of its conical shape, during the drawing
process it is automatically drawn in the direction
of drawing, through the die.
Figure 11.3 The principle of drawing over a
floating plug.
1 Drawing ring, 2 workpiece, 3 floa-
ting plug
Drawing over a moving mandrel
Instead of a plug, here, a long rod (mandrel), re-
duced at the foremost end and with a cylindrical
shoulder, is pushed into the tube. The cylindrical
tip is pushed through the pointed end of the tube.
The drawing grip takes hold of this cylindrical
peg.
During the drawing operation, the rod and the
tube are then simultaneously moved in the draw-
ing direction.
Figure 11.4 The principle of drawing over a
moving mandrel. 1 Drawing ring,
2 workpiece, 3 moving mandrel
11.3 Principal strain and drawing force
The limits for the permissible principal strains come from the required drawing force.
As the drawing force must be carried by the tube cross-section A
x
(Figure 11.5) after deforma-
tion, it must remain lower than the tensile force.
F
dr
F
perm
Figure 11.5 Tube cross-sections A
0
before and A
1
after the draw
This provides the permissible deformations. If the required cross-sectional reduction can not be
achieved at one drawing, as F
dr
! F
perm
, then intermediate annealing must be carried out after
the first draw.
Table 11.2 shows how the drawing force F
dr
and the tensile force F
perm
can be calculated
mathematically.