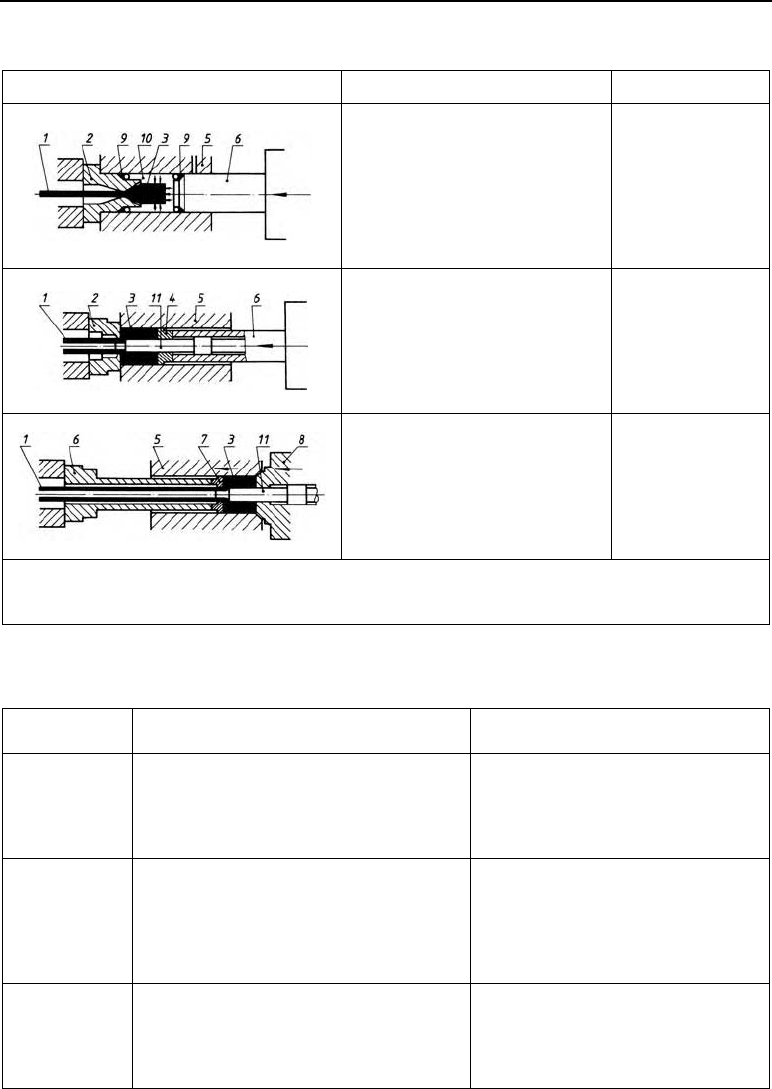
112 12 Extrusion
Table 12.1 The extrusion process (continued)
Basic schematic diagram Process Application
Direct hydrostatic extrusion: the
billet is formed by means of a
high-pressured liquid (12,000 bar)
The pressure is created by the
forwards movement of the punch.
Small, simple pro-
files made of ma-
terials which are
hard to extrude,
which can not be
extruded by other
processes.
Direct tube extrusion over a sta-
tionary mandrel: the blank is a
hollow billet. The stationary man-
drel and the die form the annular
gap. The hollow punch makes the
extrusion movement.
Tubes and hollow
profiles made from
hollow billets.
Indirect tube extrusion with sta-
tionary mandrel: the closed con-
tainer makes the extrusion move-
ment. The die is located on the
front of the stationary punch.
Tubes and solid
profiles made from
hollow billets or
solid billets which
are pierced in the
press.
1 Product, 2 die, 3 billet, 4 dummy block, 5 container, 6 punch, 7 dummy block with die, 8 plug, 9 seal-
ant, 10 extrusion liquid, 11 mandrel
Table 12.2 Advantages and disadvantages of extrusion processes
Process Advantages Disadvantages
Forward extru-
sion
Ease of operation, good product surface,
easy cooling of extrusion
High frictional heat between dummy
block and container, change in material
properties due to raised temperature,
lower extrusion speeds
Backward ex-
trusion
Higher extrusion speeds, lower deformation
resistance, lower residual materials as flow
patterns are optimal all the way into final
zone, lower wear in container
Extrusion diameter limited as passed
through the hollow punch.
Cooling down harder, requires good
dummy block surface (generally ma-
chined surface)
Hydrostatic
extrusion
Forming purely by pressure, ideal flow pat-
tern, brittle materials can also be formed,
highest degrees of deformation up to
M
= 900 % e.g. with Al materials
Problems with sealing due to high
working pressure necessary (up to
20,000 bar)