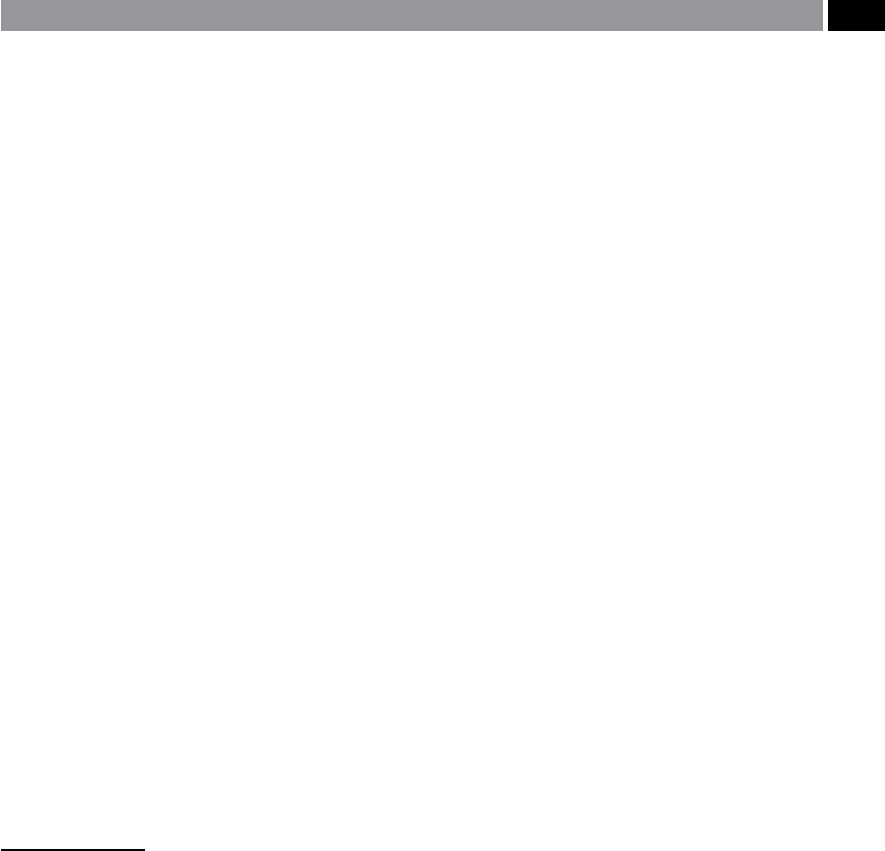
ponent’s strength and the mechanical strength of the
chip, illustrating that a complex metallurgical and cut-
ting tool geometric relationship exists whilst machin-
ing occurs.
In particular for turning operations, a convention-
ally-turned chip is a rather frail product of serrated
appearance (see Figs 25 and 34a and b). In order to
promote good chip-breaking tendencies, thus enabling
short elements to be formed, it is necessary to encour-
age this basic character by causing these serrations to
be as deep as possible and the chip sections in between
to be rigid. is chip occurrence causes the chip to be
inexible, which can then subsequently be broken.
ere are several distinct ways in which chips can then
be broken, these include:
•
Self-breaking – this is when the chip’s mechanical
strength is not great enough to hold the chip seg-
ments together and they consequently break upon
exiting the machining region (Fig. 31a),
•
Chip collision with the workpiece – as the chip is
steered towards an obstacle such as the workpiece’s
surface this provides the breaking force (see Figs.
33 and 34b),
•
Chip is stopped by the tool – here the chip-curling
behaviour comes into play, this being a function of
the: tool’s nose radius geometry, depth of cut and
feedrate employed (see Fig. 34 bottom le-hand
photograph), the latter two functions aecting the
chip cross-section, or chip thickness
31
.
31 Chip thickness is inuenced by the plan approach angle
utilised and the D
OC
, in association with the selected feedrate.
e chip thickness is measured across the cutting edge, per-
pendicular to the cut (i.e. along the main cutting edge). e
chip width and thickness are the dimensions that dene the
theoretical cut of the edge into the workpiece material. Hence,
the chip thickness will vary with the size of the plan approach
angle according to the relationships involving: feedrate, D
OC
and the eective cutting depth. e chip thickness is related to
the plan approach angle and this aects the amount of pressure
bearing upon the cutting edge. Hence, the thinner the chip,
the smaller the distributed pressure along the edge and the less
power consumed, conversely, the thicker the chip, the greater
will be the machine tool’s power consumption. A thicker chip
is generally advantageous for an increased tool life, because of
the improved contact between the chip and its cutting edge.
Furthermore, if the plan approach angle is too small and chip
thickness is thin, this will reduce tool life, however, this can
be compensated for by increasing the feedrate, to produce a
thicker chip.
NB e helical formation of this chip-curling behav-
iour will shortly be mentioned, but prior to this, chip-
breakers/formers will be discussed.
2.5.3 Chip-Breakers and Chip-Formers
Chip-breakers have been utilised on turning tools for
many years, initially introduced in the 1940’s in the
form of an abutment, or step, situated behind the rake
face of the tool. Hence, with this type of early chip-
breaker, as the continuous chip moves across the rake
face it collides with this step and breaks. is origi-
nal form of chip-breaker geomtery was relatively in-
ecient as the resultant force direction changed with
the programmed tool path, this meant that the step
would be approached by the chip from diering di-
rections making chip-breaking less controlled. Such
chip-breakers were superseded in the 1970’s by in-
built ‘wavy-shaped’ chip-breakers sintered into the in-
sert’s top face (Fig 34 bottom le-hand photograph).
Recent developments in designing chip-breaker geom-
etries by computer-generated (i.e. CAD) techniques,
has shown a signicant step-forward in both chip-
former design enabling chip control and reduction in
frictional forces across the rake face at a range of cut-
ting data to be achieved. Such ‘automatic’ chip breaker
geometry forces the chip to deect at a narrower angle,
causing it to break o, either immediately, or just aer
the free end of the chip has hit either the tool’s ank or,
the workpiece before the rst coil has formed. If such
a collision does not take place, the result would be a
smaller diameter spiral chip and, it can be anticipated
that the chip would still break, but only when it be-
came slightly longer – this later chip breakage is due to
the increasing chip mass and the eect of gravity upon
it, with, or without any further collision.
Chip ow direction will depend upon several fac-
tors, such as the: chip-breaker prole, back rake and
setting angles, nose radius, D
OC
and feedrate – these
latter three factors require further discussion. e
relationship between the nose radius, D
OC
and feedrate
will oen change during vectored tool paths in any
machining operation. Even though the insert’s nose
radius is preset, its inuence on the chip direction
diers for dierent D
OC
’s, depending on how much
corner rounding is represented by the total engaged
edge length (Fig. 34c). Further, the feedrate also af-
fects the chip thickness: at dierent D
OC
’s and with a
constant feedrate, the form of chip cross-section (i.e.
Turning and Chip-breaking Technology 69