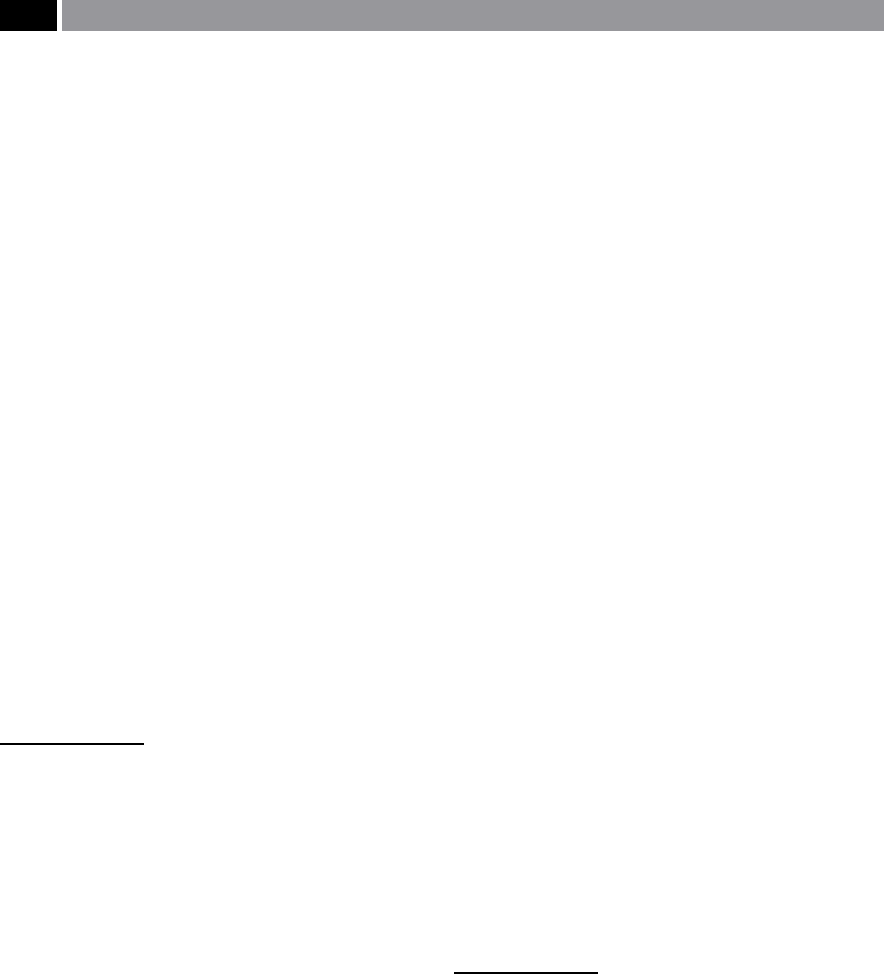
mensional accuracy and roundness, with some ‘helical
wandering’
2
as the drill passes through the workpiece.
Hole accuracy and in particular the ‘bell-mouthing ef-
fe
ct’
3
, is minimised by previously centre-drilling prior
to drilling to ‘size’. e main cause of such this ‘bell-
mouthing’ is probably the inconsistency in the drill
geometry. Such eects are exacerbated using Jobber
drills
4
, or even worse, by utilising longer-series drills,
which tend to either slightly ‘unwind’ ,
or bend as a re-
sult of lessening rigidity promoting some drill bend-
ing/deection.
It is worth noting that the rigidity of a tool such
as a drill will decrease by the ‘square of the distance’
5
.
erefore it follows that the greater the drill penetra-
tion into the workpiece, the progressively larger the
deection and, the further from the ‘true axis of rota-
tion’ will be the subsequent drill’s path. is deected
drilled hole slope angle ‘ϕ’ , can be dened in the fol-
lowing manner:
Drilled hole slope angle
‘φ’ = 3
/2 l × R/T (1 – I/k × tan k l)
Where:
l = length of deected tool,
2 ‘Helical wandering’ is the result of the drill’s geometry be-
ing ‘unbalanced’ , resulting from of diering lip lengths, or an
oset chisel point, causing the drill to ‘spiral-down’ through
the workpiece, as it progresses through the part (see Fig. 70).
‘Bell-mouthing’ of the drilled hole is attributable to the chisel
point and is produced by the line-of-contact, as the drill point
initially touches the component’s surface, causing it to ‘walk’
until the feed/penetration stabilises itself at the outer corners
(i.e. margins) entering the workpiece, whereupon, these mar-
gins guide the drill into the part.
3 ‘Bell-mouthing eect’ is produced by the drill chisel point’s
eccentric behaviour as it attempts to centralise its rotational
motion as it enters, or exit’s the workpiece.
4 ‘Jobber drills’ are considered to be ‘standardised drills’ that
are normally utilised for most drilling general operations, un-
less otherwise specied.
5 ‘Rigidity rule’: a drill, reamer, tap, or a milling cutter held in
a spindle will have its rigidity decreased by the ‘square of the
distance’ ,
namely, if a drill is twice as long it is four times less
rigid.
NB A cantilevered tool such as a boring bar has its rigidity de-
creased by the ‘cube’ or the distance – meaning that too much
tool overhang, will seriously reduce tooling rigidity.
R = ratio of the transverse reaction at the drill point,
T =
thrust force,
I =
system’s ‘moment of inertia’ ,
k =
√T/E I.
As suggested above, this ‘axis slope error’ is initiated
when the chisel edge begins to penetrate the workpiece
and unless the feed is discontinued, or in some man-
ner the error is corrected, the magnitude of deection
will increase as drill penetration continues. e drill’s
m
agnitude of deection can reach up to 60 µm, under
exaggerated drilling conditions.
e geometry of the point has been the subject
of considerable research and development for many
years, with some unusual departures from the ‘stan-
dard’ 118° drill point included angle. Typical of these
e
xtreme approaches were the so-called ‘Volvo point’ ,
having a negative 185° included angle – primarily
utilised to avoid ‘
frittering’
6
of drilled holes, or the
highly positive geometries such as 80° included an-
gle used for drilling some plastics. Not only can the
point angle be modied, but the shape and prole of
the chisel point, or web
7
oers numerously-ground
opportunities for detailed geometric modications,
with only some of which being shown in Fig. 47. Four
of the most commonly-ground drill point geometries
being:
•
Conventional – the ‘original’ Morse geometry, hav-
ing a straight chisel edge, with poor self-centring
drilling action (Fig. 46a),
•
Split-point
8
– there are a range of point-splitting
techniques available to alter the point prole, which
has the eect of modifying the chisel point to allow
a reasonable self-centring action (Fig. 47b),
6 ‘Frittering’ refers to the break-out at the hole’s edge as the drill
exit’s the part, on some brittle materials, such as on several
Powder Metallurgy compacts.
7 ‘Web’ refers to the internal core of the drill – which imparts
mechanical strength to the drill. e web increases in thick-
ness the further one gets from the chisel edge (i.e. shown in
Fig. 47 – in lower diagrams and with cross-sections). Hence,
if the drill is reground many times, the chisel point width will
obviously increase, this necessitates that the chisel point must
b
e ‘thinned’ , otherwise too high a thrust force occurs and an
inecient drilling action will result.
8 ‘Split-point’ ground drills are sometimes referred to as ‘Multi-
facet drills’.