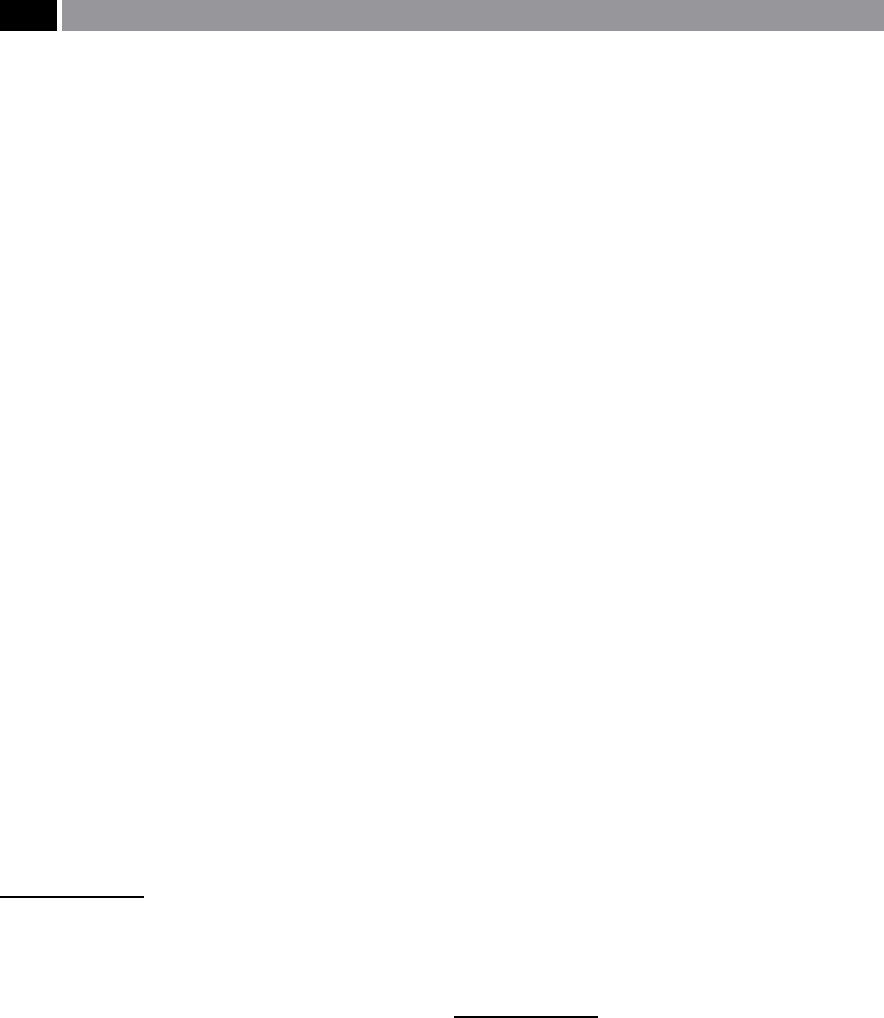
grooving, enabling the non-productive elements
42
in
the machining cycle to be minimised. In the original
multi-directional tooling concept, the top rake geom-
etry might include a three-dimensional chip-former,
comprising of an elevated central rib, with negative K-
lands on the edges. Such a top rake prole geometry
could be utilised for ecient chip-forming/-breaking
of the resultant chips. is tooling when utilised for
say, grooving operations, employed a chip-forming
geometry – this being extended to the cutting edge,
which both narrowed and curled the emerging chip
to the desired shape, thereby facilitating easy swarf
evacuation. A feature of this cutting insert concept,
was a form of eective chip management, extending
the insert’s life signicantly, thus equally ensuring that
adequate chip-ow and rapid swarf evacuation would
have taken place. When one of these multi-directional
tools was required to commence a side-turning opera-
tion, the axial force component
43
acting on the insert
caused it to elastically deect at the front region of the
toolholder. is tool deection enabled an ecient
feed motion along the workpiece to take place, be-
cause of the elastic behaviour of the toolholder created
a positive plan approach angle in combination with a
front clearance angle – see Fig. 39a and b (i.e. illus-
trating in this one of the latest ‘twisted geometry’ insert
multi-functional tooling geometries).
Any of today’s multi-functional tooling designs
(Figs. 39 and 40), allow a ‘some degree’ of elastic be-
haviour in the toolholder, enabling satisfactory tool
vectoring to occur, either to the right-, or le-hand
of the part feature being machined. ese multi-func-
42 Non-productive elements are any activity in the machining
cycle that is not ‘adding value’ to the operation, such as: tool-
changing either by the tool turret’s rotation, or by manually
changing tools, adjusting tool-osets (i.e. for either: tool wear
compensation, or for inputting new tool osets – into the ma-
chine tool’s CNC controller), for component loading/unload-
ing operations, measuring critical dimensional features – by
either touch-trigger probes, non-contact measurement, or
manual inspection with metrology equipment (i.e. microme-
ters, vernier calipers, etc.), plus any other additional ‘idle-time’
activities.
43 A
n Axial force component is the result of engaging the desired
feedrate, to produce features, such as: a diameter, taper, pro-
le, wide groove, chamfer, undercut, etc. – either positioned
externally/internally for the necessary production of the ma-
chined part.
tional tools are critically-designed so that for a specic
feedrate, the rate of elastic deection is both known
and is relatively small, being directly related to the ap-
plied axial force, in association with the selected D
OC
’s.
At the tool-setting stage of the overall machining cycle,
compensation(s) are undertaken to allow for minute
changes in the machined diameter, due to the dynamic
elastic behaviour of one of these tools in-cut. For a
specic multi-functional tool supplied by the tooling
manufacturer, its actual tool compensation factor(s)
will be available from the manufacturer’s user-manual
for the product.
In-action these multi-functional tools (Fig. 39b),
can signicantly reduce the normal tooling inventory,
for example, on average such tools can replace three
conventional ones, with the twin benet of a major
cycle-time reduction (i.e. for the reasons previously
mentioned) of between 30 to 60% – depending upon
the complexity of features on the component being
machined. Some other important benets of using a
multi-functional tooling strategy are:
•
Surface quality and accuracy improvements – due
to the prole of the insert’s geometry, any ‘machined
c
usps’
44
, or feedmarks are reduced, providing excel-
lent machined surface texture and predictable di-
mensional control,
•
Turret utilisation improved – because fewer tools
are need in the turret pockets, hence ‘sister tooling’
can be adopted, thereby further improving any un-
tended operational performance,
•
Superior chip control – breaks the chips into man-
ageable swarf, thus minimising ‘
birds nests’
45
and
entanglements around components and lessens au-
tomatic part loading problems,
•
Improved insert strength – allows machining at sig-
nicantly greater D
OC
’s to that of conventional in-
44 ‘Machined cusps’ the consequence of the insert’s nose geom-
etry coupled to the feedrate, these being superimposed onto
the machined surface, once the tool has passed over this sur-
face.
45 ‘Birds nests’ are the rotational entanglement and pile-up
of continuous chips at the bottom of both trough and blind
holes, this work-hardened swarf can cause avoidable damage
in the machined hole, furthermore, it can present problems in
coolant delivery for additional machining operations that may
be required.