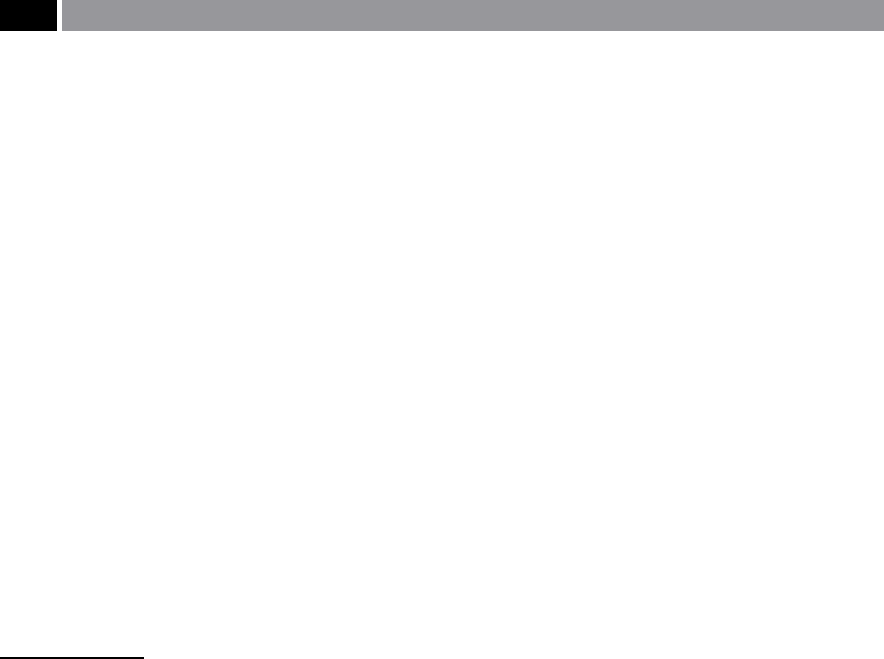
mentioned. Feedrates are normally around 50% of
parting-o values, with the proviso that for material
which is subject to work-hardening, minimum feeds
are necessary.
In transversal grooving operations, a unique chip
form occurs, because the chip is longer the further
away it is from the workpiece’s centre line of rotation.
is results in the chip which no longer ows in a
straight line across the insert’s edge, instead it moves
at an angle. Such a naturally curved chip is dicult to
exhaust from the face groove, particularly if it is bro-
ken. Hence, no attempt should be made to break the
chip. For deep and narrow grooves, the best solution
is to retract the tool at short intervals, to check that
the blade shows no signs of rubbing, this is to guard
against any likely breakage that might occur when
machining outside the blade’s range. Due to the fact
that transversal grooving tooling is susceptible to chat-
ter
34
, any excessive overhang of the tool should be mi-
nimised. e chip should never be allowed to become
entangled within the transversal groove and should be
ejected speedily, otherwise the tool is likely to break.
34 Chatter is a form of self-excited vibration and such vibrations
are due to the interaction of the dynamics of the chip-removal
process, together with the structural dynamics of the machine
tool. Such chatter, tends to be at very high amplitude, which
can result in either damage to the machine tool, or lead to pre-
mature tool failure. Typically, chatter is initiated by a distur-
bance in the cutting zone, for several reasons, such as:
Lack of homogeneity – in the workpiece material (i.e. typi-
cally a porous component, such as is found in a Powder
Metallurgy compact),
Workpiece surface condition (i.e. typically a hard oxide scale
on a hot-rolled steel component, utilsing a shallow D
OC
),
Workpiece geometry (i.e. if the component shape produces
either a variation in the D
OC
– for example, because of un-
even depth of casting material being machined, or light cuts
on interrupted shapes, such as hexagon, square, or rectan-
gular bar stock),
Frictional conditions (i.e. tool/chip interface frictional
variations, whilst machining).
Regenerative chatter is a type of self-excited vibration, result-
ing from the tool cutting a workpiece surface that has either
signicant roughness, or more likely the result of surface dis-
turbances from the previous cut. ese disturbances in the
workpiece surface, create uctuations in the cutting forces,
with the tool being subjected to vibrations with this process
continuously repeating, hence the term ‘regenerative chatter’.
Self-excited vibrations can be alleviated by either increas-
ing the dynamic stiness of the system, or by increasing the
damping.
NB Dynamic stiness can be dened as the ratio of the am-
plitude of the force to the vibrational amplitude.
–
–
–
–
For any face grooving of workpiece material that is
subject to a continuous chip formation, always use
copious amounts of coolant and at high-pressure – if
possible, to not only lubricate the cutting zone, but to
aid in chip ushing from this groove.
Par ting-off
e parting-o process is normally considered to be a
separate machining operation, but it simply consists of
cutting a groove to centre of rotation of the workpiece,
to release it from the bar stock, or to ‘part-o ’ to a pre-
viously formed internal diameter (shown in Fig. 40 for
le-hand side operations). Essentially in a parting-o
operation, two time-periods are worthy of mention,
these are:
(
i) At separation from the bar stock – a lower spindle
speed than was previously used on the workpiece, will
prevent the ‘released part’ from hitting the machine
and potentially damaging its surface. Moreover, it al-
lows an operator – if present – to hear the change in
the lower spindle speed tone, as it is about to separate
from the bar stock, avoiding the parting-o tool from
getting ‘pinched’ between the stock and the soon-
to-be-released component. Oen, ‘Part-catchers’ are
utilised to reduce any surface damage to the falling
component, once it has been parted-o.
N
B If the component to be parted-o is held in a co-
axial/sub-spindle, at component release, the additional
spindle supports the workpiece and under these con-
ditions, the parting-o operation is virtually identical
to that of found in a grooving cycle.
(
ii) Surface speed reduction – this eectively oc-
curs when the machine’s spindle attains its maximum
speed. For example, on a machine tool having a maxi-
m
um speed of 3,000 rpm, 90 m min
–1
would only be
achievable until the parting diameter has reached
a
bout 8.6 mm. When parting to a smaller diameter
than 8.6 mm, the surface speed would decrease at a
xed spindle speed. As the parting diameter reaches
5
.8 mm the surface speed would be 55 m min
–1
, or 60%
of the ideal, thus signicantly increasing the chip load-
ing as the tool approaches the workpiece’s centreline.
In order to alleviate the increasing tool loading, lower-
ing the feedrate by about 50% until separation is just
about to occur, then nally dropping the surface speed
to almost zero at this point, reduces the tendency for a
‘pip’ to be present on the workpiece. On a CNC driven
spindle, it is not advisable for parting-o operations,