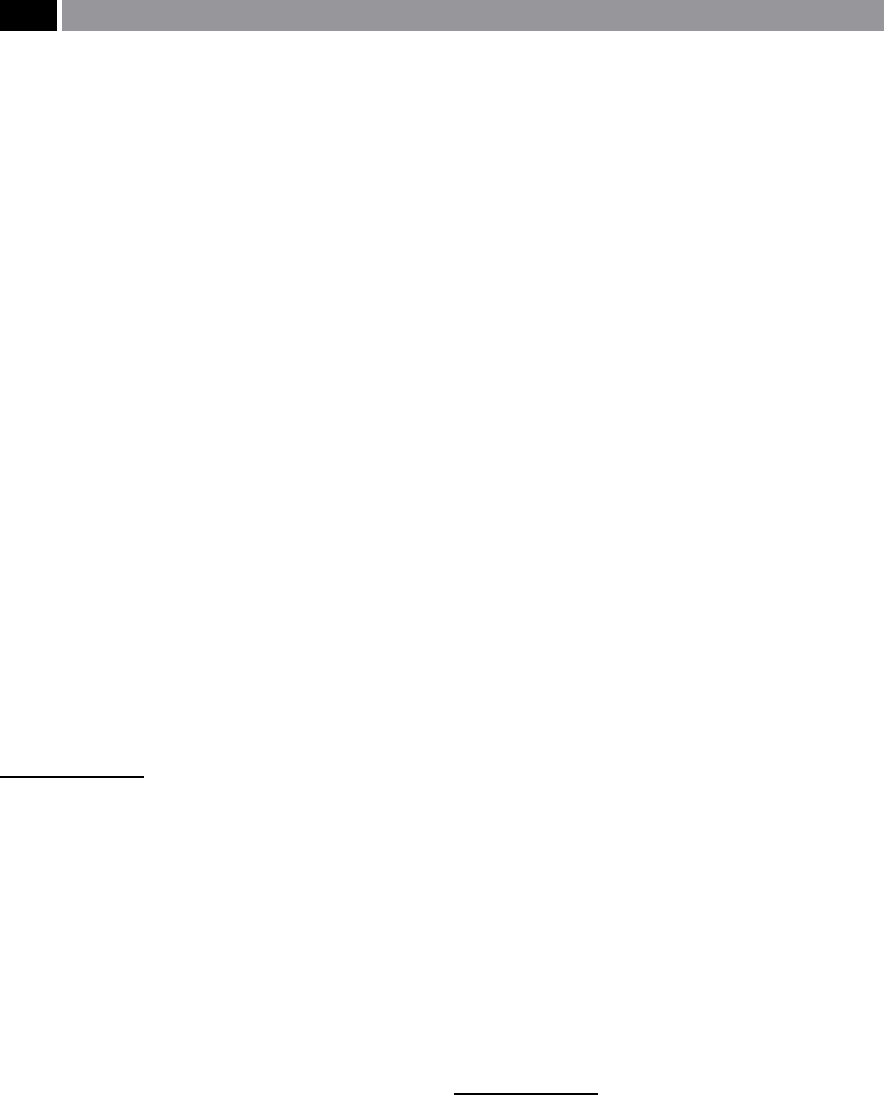
ing machined
20
. Once the chip deformation begins, it
will continue within this ‘zone’ , as though here in this
vicinity, the workpiece material is exhibiting a form of
negative strain-hardening.
e oblique cutting process
21
presents a dierent
and much more complex analytical problem, which has
been the subject of a lot of academic interest over the
years. Even here, the whole cutting dynamics change,
when the tool’s top rake surface is not at, which is the
normal status today, with the complex contoured chip-
breaker geometries nowadays employed (typically il-
lustrated in Figs. 4, 10 and 27a).
Actual chips are normally severely work-hardened,
in particular with any strain-hardening materials (for
example: high-strength exotic alloys employed for
heat-resistance/aerospace applications) as they evolve,
by the combined action of: elevated interface tempera-
tures, great pressures and high frictional eects. Such
machined action of the combined eects of mechanical
and physical work, produce a ‘compressive chip thick-
n
ess’
22
, which is on average, dimensionally wider than
the original undeformed chip thickness (see Fig. 26).
e rake angle depicted in Fig. 26 is shown as posi-
tive, but its geometry can tend to the neutral, right
through to the negative in its inclination. As the rake
angle changes, so will the complete dynamic cutting
behaviour also change, modifying the mechanical and
20 As the shear plane passes through a particular stress concen-
tration point, it will deform more readily and at a lower stress
value, than when one of these ‘points’ is not present.
21 Oblique machining, is when the rake face has a compound an-
gle, that is it is inclined in two planes relative to the workpiece,
having both a top and side rake to the face, creating a three-
force model (see Fig. 19a), where the cutting force mathemati-
cal dynamics are extremely complex and are oen produced
by either highly involved equations, or by cutting simulations.
is latter simulated treatment is only briey mentioned later
and is outside the remit of this current book. However, this
information on dynamic oblique cutting behaviour can be
gleaned, from some of the more academic treatment given in
some of the selected books and papers listed at the end of this
chapter.
22 Compressive chip thickness is sometimes known as the: chip
thickness ratio (r)* – being the dierence between the unde-
formed chip thickness (h
1
)
and the width/chip thickness of the
chip (h
2
).
*Chip thickness ratio (r) = h
1
/h
2
** (i.e. illustrated in Fig. 26).
** h
2
= W/ρwl
Where: W = weight of chip, ρ = density of (original) work-
piece material – prior to machining, w = chip width (i.e D
OC
),
l = length of chip specimen.
physical properties within the chip/tool region, as the
various deformation zones are distinctly altered. In ef-
fect, due to rake angle modication (i.e. changing the
rake’s inclination), this can have a profound aect on
the: cutting forces, frictional eects, power require-
ments and machined surface texture/integrity.
e chips formed during machining operations can
vary enormously in their size and shape (see Fig. 35a).
Chip formation involves workpiece material shearing,
from the vicinity of the shear zone extending from the
tool point across the ‘shear plane’ to the ‘free surface’
at the angle (ϕ) – see Fig. 26. In this region a consider-
able amount of strain occurs in a very short time in-
terval, with some materials being unable to withstand
this strain without fracture. For example, grey cast
iron being somewhat brittle, produces machined chips
that are fragmented (i.e. termed ‘discontinuous’), con-
versely, more ductile workpiece materials and alloys
such as steels and aluminium grades, tend to produce
c
hips that do not fracture along the ‘shear plane’ , as
a result they are continuous. A continuous chip form
may adopt many shapes, either: straight, tangled, or
with dierent types of curvature (i.e. helices – see Fig.
35a). As such, continuous chips have been signicantly
worked, they now have considerable mechanical
strength, therefore eciently controlling and dealing
with these chips is a problem that must be overcome
(see the section on Chip-breaking Technology). Chip
formation can be classied in a number of distinct
ways
23
, these chip froms will now be briey reviewed:
•
Continuous chips – are normally the result of high
cutting speeds and/or, large rake angles (see Figs.
26 and 27b). e deformation of workpiece mate-
rial occurs along a relatively narrow primary shear
zone, with the probability that these chips may de-
velop a secondary shear zone at the tool/chip inter-
face, caused in the main, by frictional eects. is
secondary zone is likely to deepen, as the tool/chip
friction increases in magnitude. Deformation can
also occur across a wide primary shear zone with
23 One of the major cutting tool manufacturer classies chips in
seven basic types of material-related chip formations, these
are: Continuous, long-chipping – mostly steel derivatives, La-
mellar chipping – typically most stainless steels, Short-chip-
ping – such as many cast irons, Varying, high-force chipping
– many super alloys, So, low-force chipping – such as alu-
minium grades, High pressure/temperture chipping – typied
by hardened materials, Segmental chipping – mostly titanium
and titanium-based alloys.