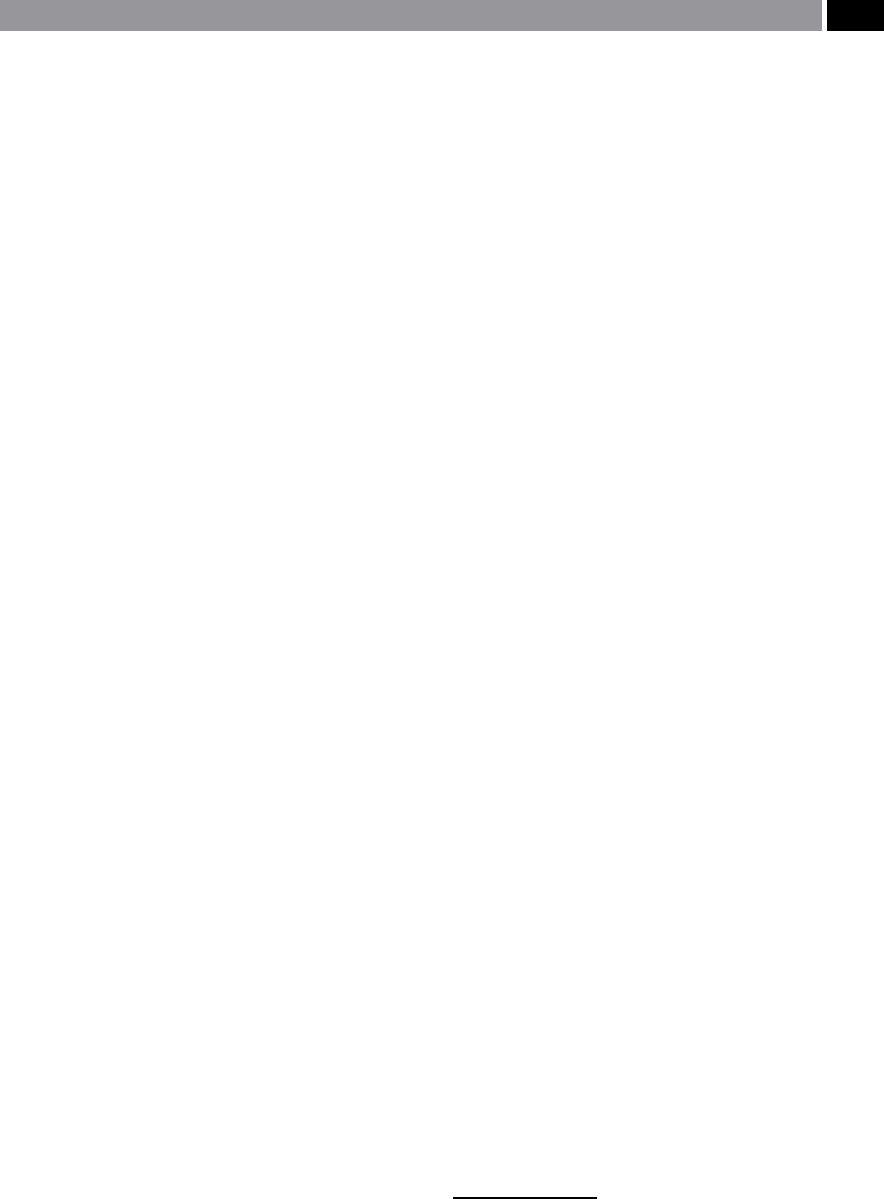
not take place when machining many non- ferrous and
non-metallic workpiece materials. Although CBN is
synthesised in a similar fashion to that of PCD cutting
tool products, it is not as hard as PCD and is therefore
less reactive with ferrous metals, as long as the cut-
ting temperature is less than 1,000°C, it will not revert
to its soer hexagonal form and oxidise in air. is
means that CBN can machine many ferrous parts and
cast iron grades. e complementary nature of both
CBN and PCD is clearly depicted in Fig. 14, where the
‘cross-over’ between these ultra-hard cutting tool ma-
terials is shown.
In both CBN and PCD machining applications,
an excellent machined surface nish can be obtained
(see Figs. 15a and b). In the case of many PCD opera-
tions, the cutting tool must not only machine widely
diering materials that are situated adjacent to one
another in many passes over such a diverse material
workpiece, but produce an excellent machined surface
nish, which really ‘challenges’ the tool. Tool life can
be extended greatly by utilising either CBN, or PCD
tooling, oen tool lives can be increased by 50 to 200
times that of the previous cemented carbide alterna-
tives. is boost in output, makes their additional
purchase price irrelevant, when considered against the
massive productive gains that are to be made by their
adoption.
Today, both CBN and PCD can oen be found
as either thin-coated layers on tooling (see Fig. 3 for
their relative tool insert hardnesses/toughnesses), or
as a ‘sandwich’ between metallic backing layers. ese
‘sandwiched’ tool edges, permit brazing on both sides
of the hardened product, which are then accurately
positioned and held onto a tungsten carbide shank,
making them an ideal alternative for many micro-
drilling operations. Such compound drilling edge
technology, gives considerably improved edge reten-
tion and resistance to any abrasive particles present in
the workpiece and its severely work-hardened swarf,
typically found with the latest metal matrix composites
(MMC’s). Such ultra-hard tooling, can be readily used
on high-silicon aluminium alloys used in the automo-
tive industries, while not discounting the wide range
of workpiece composites employed by the aerospace
industries and the resin-based components utilised in
the furniture industry.
1..11 Natural Diamond
Monolithic, or single-crystal diamond (SCD), is the
hardest material available today. If such natural dia-
mond is used correctly in a very rigid machine-tool-
workpiece setup for materials that require the best
possible surface nish, then there is simply no alterna-
tive. By way of illustration of this fact, if production
turning high-silicon content aluminium pistons with
polycrystalline diamond (PCD) tooling, the best sur-
face nish that can be obtained will be in the region
o
f 0.4 µm, conversely using an SCD tool this will give
a surface nish of better than 0.15 µm. If one really
wants the ultimate surface nish currently obtainable
b
y machining – in the ‘nano-range’ , then a monolithic
diamond tool, mounted in a special-purpose diamond
turning lathe is the only manner in achieving such su-
perb ‘mirror-nish’ surfaces. SCD tool edges are pro-
duced as either razor sharp edges, or are made with
a perfect radius being chip-free, imparting machined
‘mirror-nishes’ of just a few angströms (i.e. 10
–10
m).
e optical industries in particular nd that the latest
blemish-free ultra-sharp cutting edges of SCD, means
that diamond (paste) polishing aer machining has
been virtually, if not completely eliminated, this fact in
particular being a very big production cost for the -
nal manufacture of large monolithic astronomical mir-
rors. A cautionary note, is that to use SCD tooling for
anything other than as a nishing cut is totally uneco-
nomic, as these precision components to be machined,
should have been roughly congured to the desired
shape, prior to diamond machining. erefore, SCD
tools should be employed for exceedingly light nish
cuts of no deeper than 0.0008 m.
Natural diamond is a truly remarkable material,
that exhibit’s a diverse range of mechanical and physi-
cal properties. For example diamond has the highest
known: bulk hardness, thermal conductivity, while
having a very low coecient of friction and will not
corrode, these properties make it an ideal tool material
for the highest precision and accuracy machined com-
ponents. Of these properties, hardness is probably the
most important characteristic in machining operations
and, when measured by the Knoop indentor
15
. By way
of comparison of ultra-hard cutting tool materials, the
following two examples may prove informative:
15 Knoop indentors produce a wedge-shaped indentation in the
form of a parallelogram, with one diagonal seven times lon-
ger than the adjacent one. e Knoop test method is generally
considered the optimum technique, for crystalline solids –
having crystallographic directionality (i.e. anisotropy).
Cutting Tool Materials