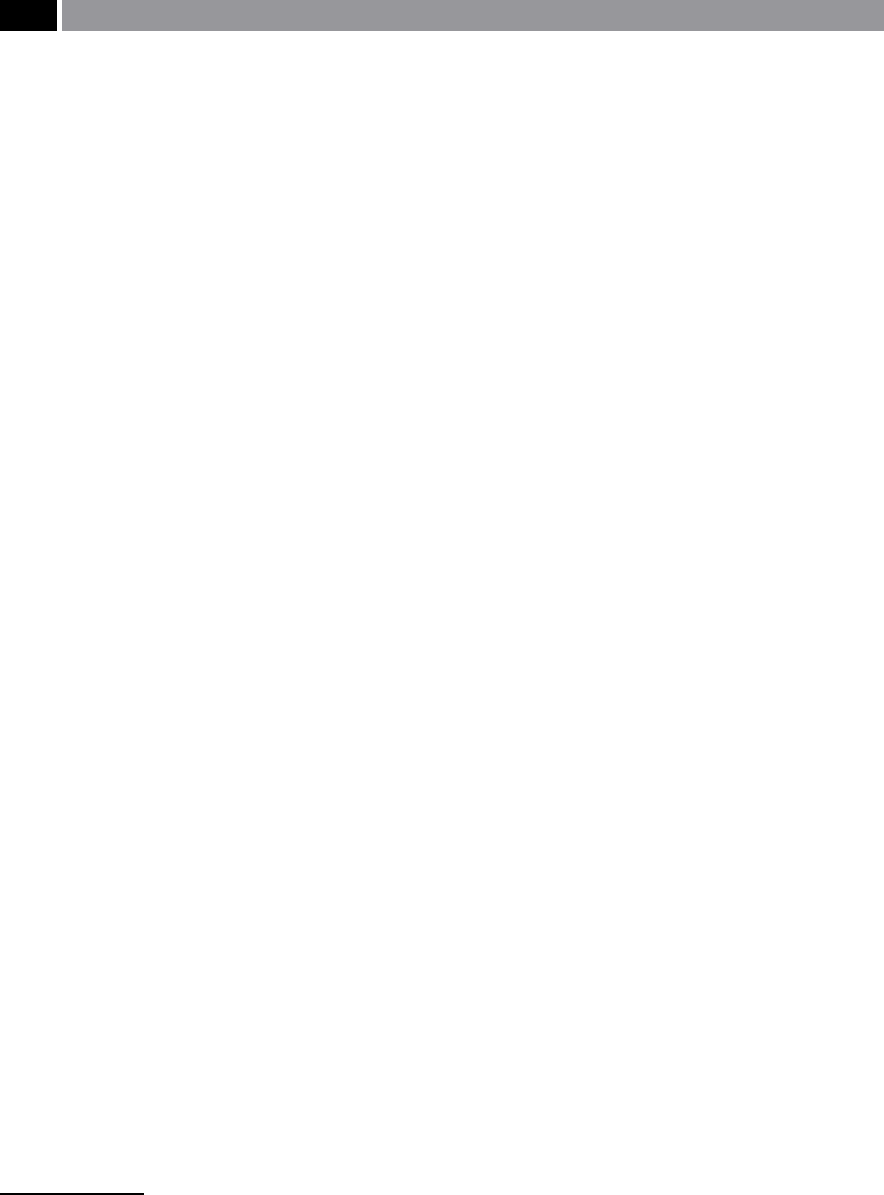
•
Natural diamond – has a hardness of 9,000 kg mm
–2
(ie diamond orientation and test conditions): Dia-
mond (111) surface, <110> direction, 500g load,
•
Cubic boron nitride (CBN) – has a hardness of
4,500 kg mm
–2
, (111) surface, <110> direction, 500g
load.
One of the main limitations of natural diamond is that
it has distinct cleavage planes (111)
16
. is consistent
cleavage plane makes it ideal for jewellery-makers to
cleave the beautiful facets demanded of diamond jew-
ellery, but this means that monolithic diamonds must
be mounted in their respective tool holders in exactly
the correct orientation/plane, so avoiding any poten-
tial cleavage in-cut.
SCD tool cost is a draw-back, because these tools
cost in the region of four times more than the equiva-
lent PCD tool. However, despite this very high cost
dierence, SCD can reduce the overall operating costs
and signicantly improve productivity, when applied
to the correct machining process. Expensive tooling
such as SCD, must be handled with care, because al-
though it is the hardest material known, it is also very
brittle and subject to thermal shock, the problem being
exacerbated with its very sharp tool edges. erefore,
it is essential that sudden impacts to the tool’s edge
must be avoided, through either inappropriate cutting
applications, or by rough handling.
References
Journal and Conference Papers
Boller, R. Crystal Clear – DLCoatings. Cutting Tool Engg.,
36–40, May 2002.
Craig, P. Behind the Carbide Curtain. Cutting Tool Engg.,
26–41, Aug., 1997.
Dzierwa, R. Slippery when Blue – Coatings. Cutting Tool
Engg., 36–41, Jan., 2003.
Eastman, M. Inserts Show their True Colors. Cutting Tool
Engg., 30–36, April 1999.
Feir, M. Post-treatment of PM Parts. Metal Powder Report,
28–30, Jan., 1981.
16 Miller indices determine the crystalline orientation for a plane
in an atomic structure and for natural diamond it is normally
on the (111) plane, although some cleavage has been observed
on the (110) plane.
Fretty, P. Grade Wise. Cutting Tool Engg., 46–50, Feb.,
2000.
Gough, P. Tool Life Boosted by Titanium Nitride Coat. Ma-
chinery and Prod. Engg., 52–53, Feb. 1983.
Gummeson, P.U. and Stosuy, A. Iron-carbon Behaviour dur-
ing Sintering. In: Source Book on Powder Metallurgy,
ASM Pub., 49–61, 1979.
Hanson, K. Lowering your Grades. Cutting Tool Engg.,
54–60, Jan., 2000.
Heath, P.J. Ultra-hard Materials. European J. of Engg. Ed.,
Vol. 12 (1), 5–20, 1987.
Israelsson, J. A Progress Report on Cutting Tool Materials.
American Machinist, 39–40, Dec., 1992.
Jindal, P.C. et al., PVD Coatings for Turning, Cutting Tool
Engg., 42–52, Feb., 1999.
Kennedy, B. Making the Grade – PCBN Applications. Cut-
ting Tool Engg., 22–30, June 2002.
Lewis, B. Fast Times in HSS. Cutting Tool Engg., 28–32,
July 2001.
Lewis, B. Condence Game – Grades and Geometries. Cut-
ting Tool Engg., 46–52, Dec., 2002.
Mielert, W. Coating for Speed. Cutting Tool Engg., 40–44,
Feb., 1996.
Mirchandani, P.K. Making a Better Grade – Composite Car-
bide Substrates. Cutting Tool Engg., 58–61, Jan., 2005.
Mitoraj, L. e Coating Edge. Cutting Tool Engg., 51–55,
Feb., 2000.
Novak, D. Single Minded – Single Crystal Diamond. Cutting
Tool Engg., 38–41, June 2002.
Raymond, M.K. Ceramics Ease Up the Machining of High-
hardness Parts, American Machinist, May 1996.
Raymond, M.K. Coatings Keep Cutting Tools Sharp. Ameri-
can Machinist, 40–42, May 1996.
Richter, A. Raising Al – AlTiN Coatings. Cutting Tool Engg.,
42–46, Jan., 2003.
Richter, A. Top Coat. Cutting Tool Engg., 36–41, Dec.,
2003.
Sanders, E.H. Understanding Coated Carbides. Cutting Tool
Engg. 3–7, Sept./Oct., 1977.
Sprout, W. PVD Today. Cutting Tool Engg., 52–4057, Feb.,
1994.
Taylor, F.W. On the Art of Cutting Metals. Trans. of ASME
28, 31–350, 1907.
almann, R. Cracking the Code – Carbide Classications.
Cutting Tool Engg., 34–43, June 1995.
Vasilash, G.S. e Superfard Coatings: More than Meets the
Eye. 52–54, Production, Dec., 1995.
Weiner, M. Coatings Move Forward. Cutting Tool Engg.,
22–29, Feb., 1999.
Woods, S. Coat, Please. Cutting Tool Engg., 50–56, Oct.,
2004.