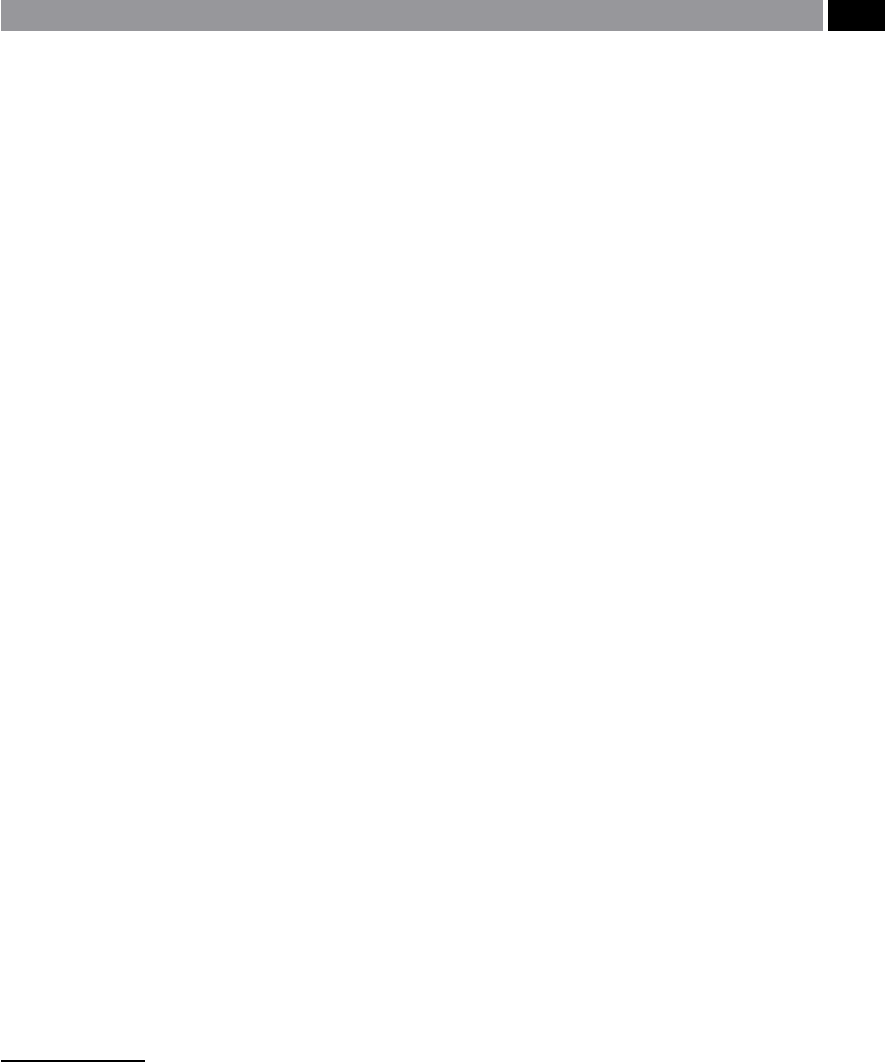
•
Minimal uid-ow disturbance – giving consis-
tent/regular ow-rate to drill-head,
•
Minimum of uid-turbulence – allowing chips to
be easily evacuated from the cutting region.
Typically, cemented carbide heads, have an external V-
shaped chip-ute which extends along the shank, the
angle of this chip-ute has been experimentally-deter-
mined to be 110°, providing the following advantages:
•
Optimum ute cross-section – allowing the most
rapid cutting uid return and chip transportation,
•
Facilitates an extra support pad – this is necessary
when drilling through crossing holes,
•
Provides optimal torsional strength – important
for workpieces having very long length-to-diameter
ratios,
•
Facilitates tool clamping – enabling the tool to be
held in a three-jaw chuck for convenient regrinding
on a suitable cutter-grinder.
Gun-Drill Failure
One of the main reasons for Gun-drills to fail in op-
eration, is through an excessive misalignment of the
drill bushing and this will be in relation to the drill’s
rotational axis (i.e. see Fig. 58a). is type of align-
ment failure mode is termed a ‘balk-crash’ – caus-
ing the tool to fracture into numerous pieces
33
. If the
drill is rotated rather than the workpiece, the stress is
re-applied to diering portions of the tip and, at the
weakest point, namely the drill’s corner, the tip will
most likely fracture in this region. A potential failure
mode is related to the Gun-drill’s length, which has its
rigidity decreased with increased length
34
. e shank
of a longer Gun-drill will not transmit a large amount
of bending force to the cutting tip – when misaligned
– however, the tip does not fracture, but instead, any
axis misalignment causes the shank to ex with each
revolution, a situation that is ideal for a fatigue fail-
33 ‘Balk-failure’ of Gun-drills is the result of the ‘brittle’ carbide
tip being unable to withstand the bending stresses created by
its unintentional axis misalignment.
34 Gun-drill ‘rigidity rule’: as the drill’s length increases, its ri-
gidity decreases by the ‘cube’ of the distance. For example, if
two identical Gun-drill diameters are employed for drilling
the same workpiece material, then if one drill is twice as long
as the other, then its rigidity will 8 times less rigid than its
counterpart (i.e. namely: 2
3
).
ure mode. Yet another Gun-drill failure situation may
arise if there is excessive clearance between the drill
bush and the drill’s tip. Under these circumstances, the
Gun-drill’s edge cuts a signicant volume of workpiece
material and, as this edge is not designed to cut – hav-
ing a zero clearance angle (i.e. created by the circular
margin at this edge) – the excessive cutting forces
cause the edge to prematurely fracture.
If insucient coolant ow occurs, this is also a typ-
ical factor in subsequent Gun-drill failure. is lack of
coolant causes the chips to pack in the V-ute, forming
a plug, which then creates excessive torque in the Gun-
drill and, this plug allows the tip to separate away from
the shank. Occasionally, end-users blame the Gun-drill
tooling manufacturer for poor brazing, if the tool’s tip
separates from the shank. However, when analysis of
the brazed fractured surfaces occurs, invariably, small
carbide particles are adhered to the shank, this being
evidence of the fact that the braze was stronger than
the tip, clearly demonstrating that the brazing was not
at fault.
In many circumstances, the Gun-drill tool manu-
facturer is blamed by the customer for its failure dur-
ing machining, but when investigated, it is usually
premature failure being the result of a poor tooling
installation and operation. One of the major causes of
Gun-drill failure, is via the coolant distribution sys-
tem, where inconsistent delivery of the uid can either
‘starve’ the Gun-drill’s cutting edge, or ‘over-ood’ the
system. One of the major factors contributing to this
over-/under-supply of coolant delivery, is due to the
fact that in the main, coolant pressure is being moni-
tored, rather than the measurement of coolant ow-
r
ate. If holes are Gun-drilled < φ4 m
m, then high-pres-
sure coolant ow-rate to the point is essential, but in
many cases of coolant systems tted to ‘standard’ ma-
chines, they are of relatively low-pressure delivery. Re-
cently, one machine tool manufacturer, has designed
and developed a coolant intensier pump coupled to
a special high-pressure union, which gives variable
pump pressures of over 200 bar, with special-purpose
couplings to overcome the problems of poor coolant
ow-rates to the cutting vicinity.
3.1.8 Double-Tube Ejector/Single-
Tube System Drills
Double-tube Ejector drills (i.e. oen just termed ‘Ejec-
tor Drills’), are designed around a twin tube system
Drilling and Associated Technologies 115