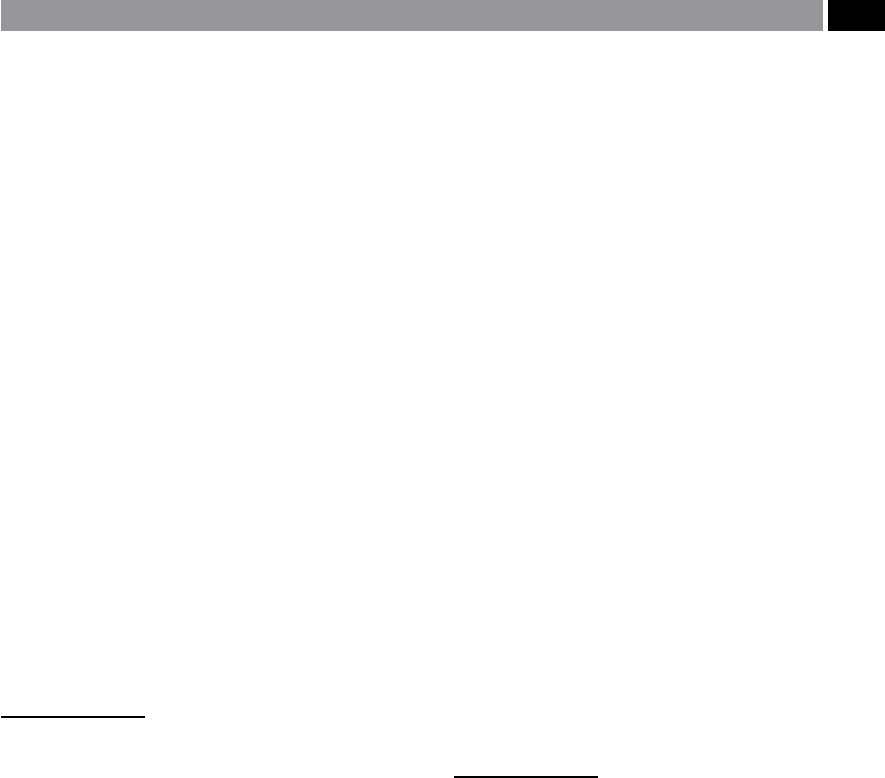
Prior to beginning the reaming process
53
, holes
have to be either pre-drilled, or holes cored-drilled
54
.
Due to the nature of the role of the burnishing pads on
the hole’s machined and highly-compressed surface in
Gun-drilling operations, it is not particularly suitable
for reaming.
Machine reamers can be divided into several cat-
egories, these are: multi-point reamers with either
a straight, or Morse taper
55
shank, these reamers are
usually either manufactured from: HSS, Tungsten
carbide (Solid), or with carbide tips. Typically, the
Tungsten carbide (solid) reamers can be run at 10%
higher feedrates, to their HSS equivalents and can
ream workpiece materials up to a tensile strength of
1
200 N mm
–2
.
Machine reamers are available with: straight utes,
le-hand (LH) spirals, or 45° LH ‘quick’ spirals this lat-
ter reamer version is oen termed a ‘Roughing reamer’
and is oen used for ‘long-chipping’ workpiece mate-
rials. Reamers with straight utes are usually utilised
to ream blind holes, but with the absence of chip space
at the bottom, this means that swarf must be evacuated
by the utes. For virtually all other machining tasks,
such as holes with keyways, or intersecting holes, etc.,
53 ‘Hand-reamers’ , are available for the reaming both cylindrical
and tapered holes.
NB A basic rule to be observed when hand-reaming, is to
only turn the tool in the cutting direction and, never reverse
it (e.g. is is the standard practice in cutting a thread with
hand taps), as the reamer’s cutting edges will immediately be-
come blunt.
54 ‘Core-drilling’ ,
this is normally undertaken with a multi-
uted drill, as the hole already exists in the cast component
and in the main, the drill cuts on its periphery, so needs more
cutting edges in contact with the cored hole. Coring is result
of employing a core, prior to casting and it stays in the cavity
as the molten metal is gently poured to cast the part (i.e. cores
are normally made from an appropriate sand and binder, or
another suitable material, that can be removed at the ‘fettling
stage’ – leaving the hole), hence, its name: cored hole.
55 ‘Morse taper’ ,
was developed in the USA in the mid-to-late
1800’s by Steven Morse (i.e famed for his design and develop-
ment of the original geometry for the Twist drill). e Morse
taper is a ‘self-holding taper’ , which can be suitable sleeved ei-
ther upward, or downward in ‘ioned diameter’ to t the inter-
nal taper for the machine tool’s spindle/tailstock, requiring a
‘dri’ to separate the matching tapers upon completion of the
work. e Morse taper’s included angle varies marginally, de-
pending upon its Number (i.e ranging from 0 to 6). Typically,
a ‘No. 1’ is: 2° 58´ 54´ ´, with a ‘No. 6’ being: 2° 59´ 12´ ´.
LH spiral reamers are employed. e chip direction is
always in the feed direction and, for this reason, the
spiral ute geometry is virtually exclusively used for
through hole reaming operations.
3.3.1 Reaming – Correction
of Hole’s Roundness Profiles
Machine Reaming
In the ‘classical’ reaming operation, it is centre-drilled,
then the hole is through-drilled possibly producing
a variety of hole form harmonic out-of-roundness
errors present (i.e. see Fig. 70 ‘polar plots’ – bottom
le), including ‘
bell-mouthing’
56
at the entry and exit
of through drilled holes. Not only is there a possibil-
i
ty of ‘bell-mouthing’ , but a serious likelihood of the
drill following a helical path through the part, this is
termed: ‘helical-wandering’ (
i.e. see ‘Footnote No. 3’ ,
for an explanation of this drilling condition). By a fol-
lowing boring operation, this will correct for any prole
errors, while improving both the part’s overall out-of-
roundness
57
as exhibited by the ‘polar plots’ (ie. as il-
lustrated in Fig. 70 middle-le), but the hole’s ‘cylin-
d
ricity’
58
. Finally, the machine reamer is used to full
several functions: improve both the harmonic out-of-
56 ‘Bell-mouthing’ , is the result of the unsupported drill (i.e.
the margins as yet, not in contact with the drilled hole’s side
walls), producing the so-called ‘bell-mouth prole’ , upon hole
entry. At exit, if the drill is allowed to feed too far past the un-
derside of the hole, the drill has a ‘whipping-tendency’ , which
could introduce a smaller ‘bell-mouthing eect’ beneath the
part’s lower face.
57 ‘Out-of-roundness’ ,
was a term previously utilised, but today,
the term used has been changed to: ‘Departures from round-
ness’ , moreover, the term ‘polar plot’ has also been super-
seded by the term ‘displayed prole’ , however, in the current
context the former terms will be used.
58 ‘Cylindricity’ ,
is the term dened as: ‘Two, or more roundness
planes used to produce a cylinder where the radial dierences
are at a minimum’.
NB A more easily-understood appreciation of what ‘cylindric-
ity’ is, can hopefully be gained by the following ‘working ex-
planation’: If a perfectly at plate is inclined at a shallow angle
and, a parallel cylindrical component is rolled down this plate,
then if it is ‘truly round’ as it rolls there should be no discern-
ible radial/longitudinal motion apparent. In other words, the
component is a truly round cylinder, which can be equated to
a hole, or indeed, to a turned, or ground diameter.
Drilling and Associated Technologies 135