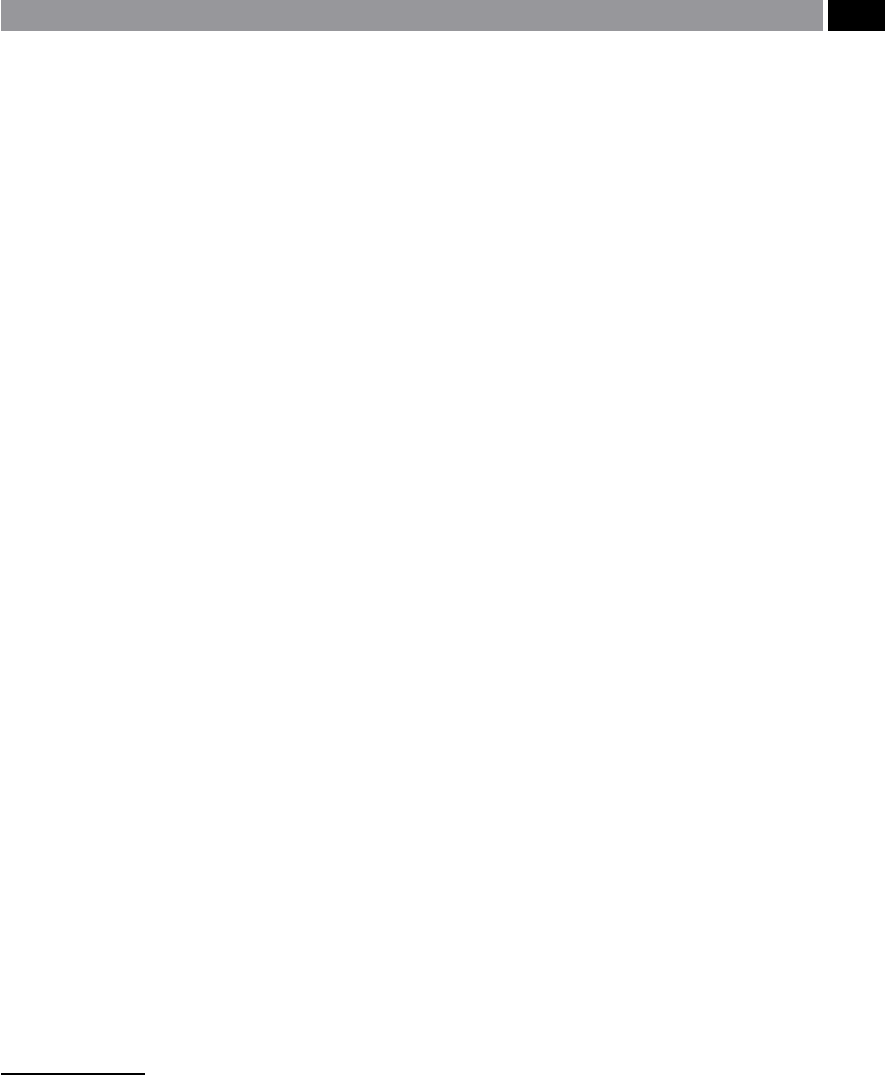
also be reduced by utilising a dierent boring bar ma-
terial, as this will improve its coecient of elasticity
45
.
In boring-out roughing operations, any vibrations
present are only a problem if they lead to insert dam-
age. For nish-boring operations, vibrational condi-
tions that may occur could be the dierence between
success and failure for the nished machined part.
So, the boring bar’s ability to dampen any vibrational
source becomes imperative, once a ne-boring opera-
tion is necessary. Vibrations can occur in any number
of ways that could aect the boring operation, from
the constructional elements of the machine tool,
through to slideways, or their recirculating ball bear-
ings, etc.. Hence, the joints in a machine tool can be
regarded as a complicated dynamic system, with any
slideway motion of vibrating contact faces, necessitat-
ing lubricating oil to not only reduce any stiction and
frictional eects, but to help dampen these structural
elements. Machine tool builders are acutely aware that
certain machine tool materials ‘damp’ more readily
than others. Cast iron and in particular ‘Granitan’ (i.e.
a product of crushed granite and epoxy resin), can pre-
dominantly act as built-in dampening media for any
vibrational sources present. e main source for any
vibrations in boring, results from the long overhangs,
necessary to machine the hole depth of the compo-
nent’s feature. erefore, the magnitude of vibrations
in the overall system result from the dampening capa-
bilities of the actual boring bar.
Tuned Boring Bars
A boring bar that has been ‘tuned’ , has the ability to
dampen any generated vibrations between the work-
piece and the cutting edge while machining. e
‘dampening eect’ is achieved through a vibration ab-
sorbing device (i.e see Figs. 61a and 62b), this has the
consequence of increasing the bar’s dynamic stiness,
giving it the ability to withstand oscillating forces. e
45 Coecient of elasticity, for a steel boring bar composition,
E = 21 × 10
4
(N mm
–2
), conversely, using a cemented carbide
material for an identical boring bar, E = 63 × 10
4
(N mm
–2
), giv-
ing three times greater stiness, allowing much greater boring
bar overhangs.
NB In reality, the boring bar’s deection will be higher than
the values given in these examples, as the formula is based
upon the assumption that the bar is absolutely rigidly clamped,
which is impossible to achieve.
method of achieving this bar damping has already been
mentioned in Section 3.2.1, with the relationships be-
tween the size of the bar’s body, suspension, viscosity
of the liquid media, being carefully designed by the
tooling manufacturer. During the boring operation,
the vibrations set the body in oscillation. Hence, the
body and the liquid alternate, taking each others place
in the space within the actual boring bar. A pattern is
established during boring, where the oscillations of the
body are not in harmony with the vibrations resulting
from machining. is out-of-harmony, means that the
vibrations are virtually neutralised – to an acceptable
level – via the kinetic energy being transformed by the
‘system damping’. Any vibrations present during bor-
ing, are relative to the amount of bar overhang, there-
fore on longer boring bar lengths, they are normally
tted with some means of adjustment, so that they can
be ‘tuned’ to the frequency occurring within its range.
e simplest manner of achieving adjustment, is by
a rotation of a lockable set screw, which when either
tightened, or slackened, aects the suspension of the
body in the liquid, thus ‘tuning’ the boring bar to the
actual machining conditions present.
3.2.5 ‘Active-suppression’
of Vibrations
As has been stated at the beginning of Section 3.2.4, if
boring bars have an L/D ratio >5:1, then vibrational ef-
fects may result in tool chatter. It has been observed in
experimental work, that the boring bar’s tip produces
a vibration motion that follows an elliptical path in the
plane normal to the longitudinal axis of the bar. e
ratio of the amplitude of vibration along the major and
minor axes varies with cutting conditions, further-
more, the inclination of these axes to the ‘radial line’
of the tool also varies. Of signicance, is the fact that
the build-up of chatter will begin almost immediately,
even before one revolution of the workpiece has oc-
curred. is build-up continues almost evenly until
some limiting amplitude occurs, which suggests that
the well-known ‘Orthogonal mode coupling’ is pres-
ent, further, with the phase dierence between the vi-
brations causing an elliptical tool tip path, the vibra-
tional energy is fed into the tool-workpiece system,
promoting self-excitation.
As has been suggested, the dynamic stability of the
boring bar is of prime importance, with the onset of
self-excited chatter, being governed by the ‘Multiple
r
egenerative eect’ , which is a function of the so-called
Drilling and Associated Technologies 127