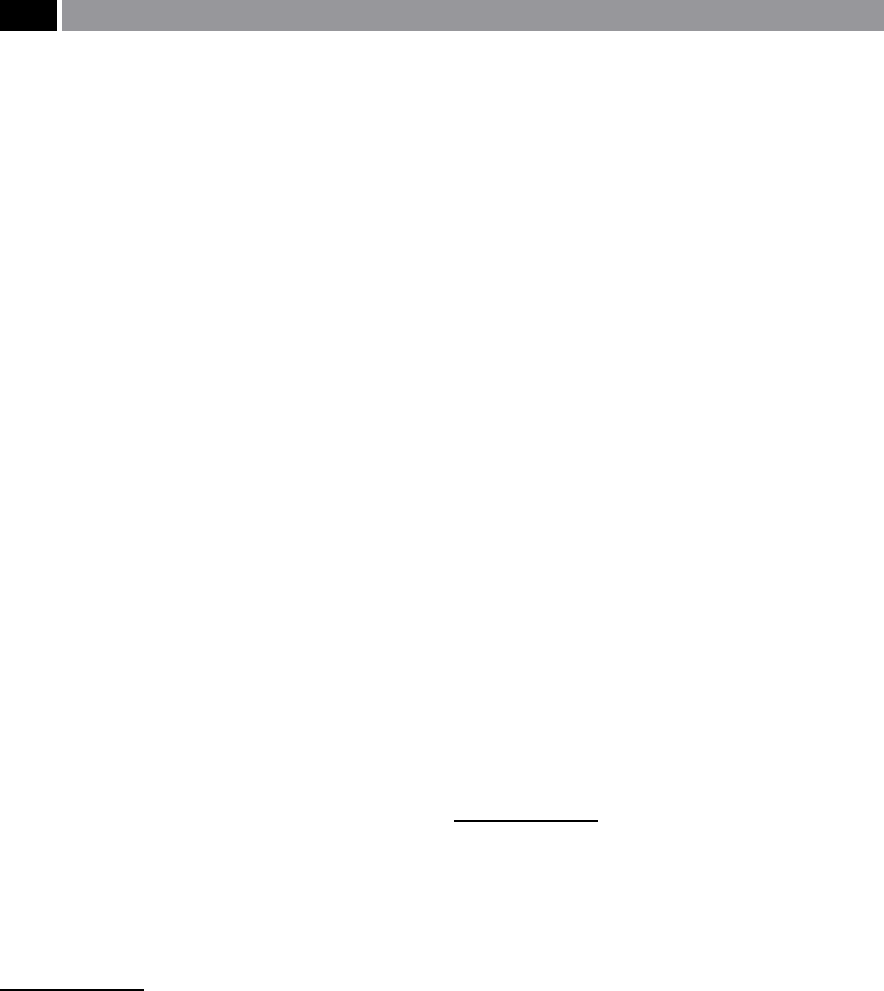
face cutter, face-mill, end mill
12
, slot-drill, etc. e
helix angle brings the cutting edge progressively into
c
ut, resulting in ‘quieter running’ , but instead of an
orthogonal cutting action (i.e. with two component
forces – tangential and radial – acting on the cutting
edge), an oblique cutting action occurs (i.e having an
additional axial force component present). is axial
force component resulting from the geometry of the
helix, has a tendency to either ‘pull’ the cutter out of
the spindle, or push it towards it, depending upon
whether it is of a le- or right-hand helix.
For all of the designs for Endmills and Slotdrills
currently available, there are basically three types of
axial and rake angled cutting edge geometries, theses
are:
•
Double-positive cutting edges (i.e shown in Fig.
80C) – normally employs a single-sided insert,
as this geometry allows a relatively ‘free’ cutting/
shearing action. Here, the positive axial and rake
geometries, produce low cutting forces, owing to
the reduced chip thickness and a shorter length of
contact at the chip/tool interface. As a result, less
spindle power is necessary, enabling a lower insert
strength requirement enabling high-shear cutting
availability, when compared to either of the fol-
lowing insert geometries. e manner in which
the chip formation occurs is benecial, in that spi-
ral chips are formed, which can easily be broken
and exhausted from their respective chip pockets.
When milling ductile materials such as grades of:
aluminium, steel, as well as some stainless and heat-
resistant steels, where there is a tendency to form
BUE, the double-positive geometry is the only suc-
cessful solution to machining such workpiece ma-
terials. If the workpiece has a tendency to be some-
what unstable, perhaps due to either its fragility, or
12 ‘Endmills’ , can not only have the cutting edges designed with
a helix angle, but for the ‘solid’ end-milling varieties, they may
have either their cutting edge land lengths interrupted by a
groove this feature being a long-lead spiral groove – to act as
a form of chip-breaker (i.e. they are oen called ‘Rippa-cut-
ters’ – utilised for high stock removal rates), for long-chipping
materials. For some cutter designs, such as: ‘Roller-, or Slab-
mills’ , they can have cutting inserts staggered along the tool’s
periphery covering the length of the body, to disrupt the long-
chipping swarf (i.e. see Fig. 76). For Endmills versions of this
inserted-toothed design, they are oen termed ‘Porcupine
cutters’ (i.e. an example of a ball-nosed version, is depicted in
Fig. 79b).
clamping method, then the double-positive insert
geometry is once again, the most suitable milling
geometry to use.
•
Double-negative cutting edges (Fig. 80B – shown
here with either a round insert – bottom-le, or
square insert – top-right) – in this case, the radial
and axial angles are both negative. When a double-
negative insert is used, the required clearance is ob-
tained by tilting the insert. is ‘tilt’ of the insert,
has the added economical benet of allowing both
sides of the insert to be utilised, enabling the avail-
ability of more cutting edges coupled to stronger
edges, when compared to the former insert geom-
etry. is double-negative milling cutter insert ge-
ometry, is most suitable for machining conditions
involving heavy impact stresses, associated with
workpieces produced from: hard steels, certain
cast iron matrices and on some of their ‘chilled-sur-
faces’
13
, or ‘induction-hardened surfaces’
14
– nor-
mally using the ultra-hard PCBN-grades of inserts.
With these ‘Double-negative’ insert cutting geom-
etries, the demands on spindle power requirement
and its stability are considerable, owing to the large
cutting forces and chip thickness factors associated
with this type of geometry.
•
Positive/negative cutting edges (Fig. 80A – illus-
trating a square insert – top-le, or an inclined
and chamfered square insert – middle-le). For ex-
ample, in the case of Fig.79a (top-le), the insert
13 ‘Chilled cast iron surfaces’ , are used in order to produce a
hard-wearing surface, this being necessary for example on the
Vee-and-at slideways’ for cast lathe beds. Here, a ‘chill’ (i.e.
normally a metallic interface) is for example strategically-po-
sitioned in the cavity, prior to pouring the liquid melt. is
‘metallic chill’ acts as a ‘heat-sink’ to quickly allow solidica-
tion at the liquid/wall interface, producing a high tempera-
ture/cooling gradient and subsequent crystalline growth of
small grains, that have become both locally hard and wear re-
sistant, but are surrounded by a graphite-based matrix that of-
fers excellent ‘damping’ qualities to the overall cast structure.
14 ‘Induction-hardened surfaces’ ,
are usually obtained by a trav-
elling electric resistance induction heating/cooling unit. is
equipment, once it has locally heated the surface, will be im-
mediately quenched*, as the apparatus slowly moves along the
required surface to be heat-treated, imparting a surface-hard-
ened layer to the cast iron.*is induction-hardened surface
now consists (i.e. metallurgically) of a very hard ‘white-iron’ ,
appearance – aer suitable metallographical preparation
– with a white surface layer, once it has been suitably acid-
etched.