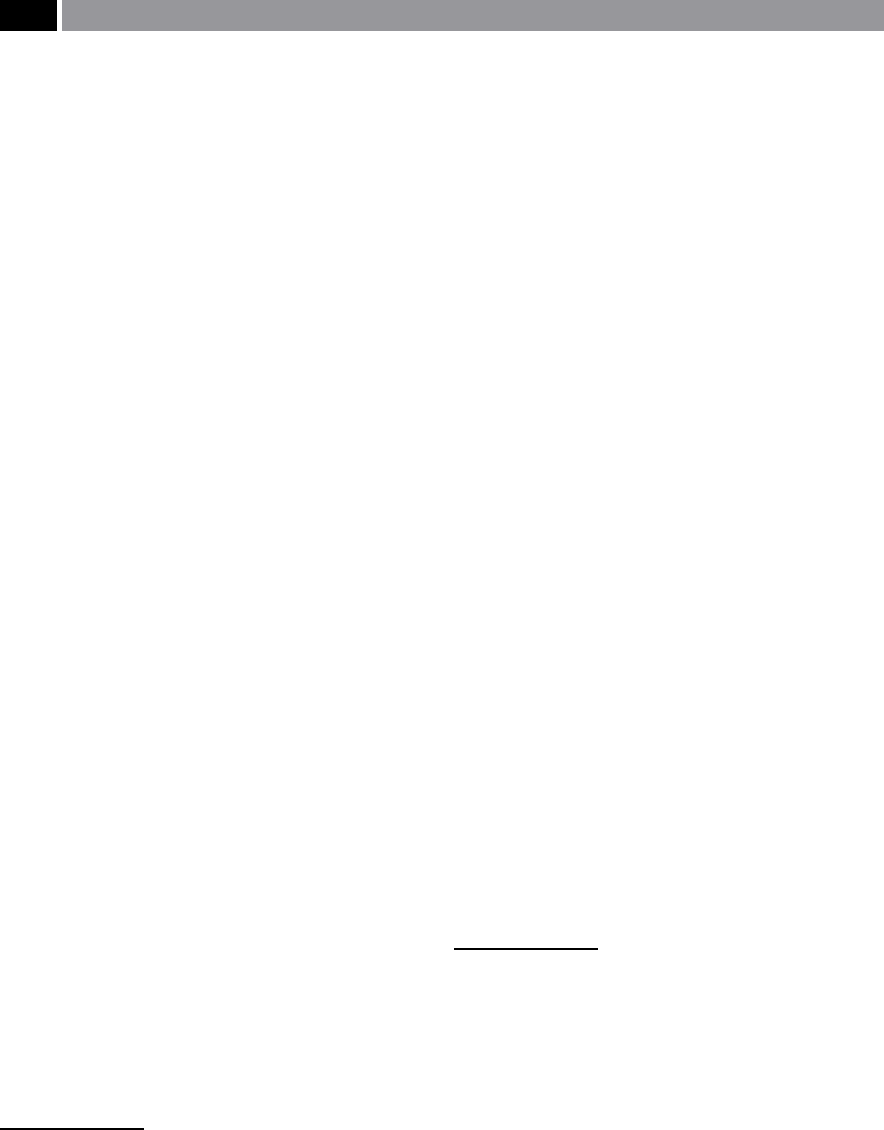
5.1 Threads
An Introduction
e originator of the rst thread was Archimedes
(287–212 BC), although the rst modern-day thread
can be credited to the Engineer and inventor Joseph
Whitworth in 1841, where he developed the Stan
-
d
ards for today’s screw thread systems. Whitworth’s
55° included angled V-form thread, became widely
established enabling thread-locking and unlocking
precision parts and of sub-assemblies – paving the
way to the build-up of precise and accurate modern-
day equipment and instruments. Standardisation of
Imperial thread forms in the USA, Canada, UK, and
elsewhere, allowed for the interchangeablity of parts
to become a reality. Around this time, both in France
and Germany metric threads were in use, but it took
until 1957 before both the common 60° included an
-
g
led ISO M-thread and Unied thread proles to be-
c
ome widely accepted and established (Fig. 95). Along
with these and other various V-form threads that have
been developed (Fig. 95i), they include quick-release
threads such as the Buttress thread: this being a modi
-
ed form of square thread, along with the 29° included
angled truncated Acme form which is a hybrid of a V-
form and Square thread. Tapered: gas, pipe and petro
-
l
eum-type threads, were developed to give a mechani-
c
al sealing of the uid, or gas
m
edium, with many
other types, including multi-start threads that are now
in use throughout the world.
V-form screw threads are based upon a triangle
(Fig. 95 – top diagram), which has a truncated crest and
root, with the root either having a at (as depicted), or
a more likely, a radius
1
– depending upon the speci-
cation. If screw threads have an identical pitch
2
, but
dierent diameters, it follows that they would have
dissimilar lead angles. Usually, threads have just one
start, where the pitch and the lead are identical – more
will be mentioned on multi-start threads later in this
1 ‘Root radius’ , is usually a stronger thread form, as it is less
prone to any form of shear-type failure mode in-service.
2 Pitch, r
efers to the spacing, or distance between any two cor-
responding points on adjacent threads, normally taken at the
thread’s eective pitch diameter.
NB e reciprocal of this pitch, is the threads per inch (i.e.
for Imperial units).
chapter. Referring to Fig. 95, the angle enclosed by
the thread anks is termed the included thread angle
(β – a
s illustrated in Fig. 95 – middle right). is thread
form is uniformly spaced along an ‘imaginary cylin-
d
er’ , its nominal size being referred to
a
s the major
diameter (d)
. e eective pitch diameter (d
2
) is the
diameter of a theoretical co-axial cylinder whose outer
surface would pass through a plane where the width of
the groove, is half the pitch. erefore, the pitch (
p) i
s
normally associated with this ‘eective’ diameter (i.e.
see Fig. 95 – middle right). e minor diameter (d
1
),
is the diameter of another co-axial cylinder the outer
surface of which would touch the smallest diameter.
read clearance is normally achieved via truncating
the thread at its crest, or root – depending upon where
the truncation is applied.
ese are the main screw thread factors that con
-
t
ribute to a V-form thread, which has similar geom-
e
try and terminology for its mating nut – for a thread
having single-start.
5.2 Hand and Machine Taps
Hand Taps
Most ‘solid’
3
taps come in a variety of shapes and sizes
(Fig. 94), with hand taps normally found in sets of
three: taper, plug and bottoming (Fig. 96). e pro-
c
ess of tapping a hole rstly requires that a specic-
sized diameter hole is drilled in the workpiece, this is
termed its
‘tapping size’
4
. e taper tap along with its
wrench are employed in producing the tapped thread.
3 ‘Solid taps’ , are as their name implies, but it is possible to use
‘collapsible taps’. ese ‘collapsing taps’ have their cutting ele-
ments automatically inwardly collapsing when the thread is
completed – allowing withdrawal of the tap – without having
to unscrew it, moreover, these ‘collapsible taps’ can be self-set-
ting ready for the next hole to be tapped. ey are ‘sized-re-
stricted’ by their major diameter.
4 ‘Tapping size’ , r
efers to the diameter of hole to be drilled that
will produce sucient thread depth for the threaded section
to be inserted and screwed down, for a particular engineering
application. For example, the alpha-numeric notation: M6x1,
refers to a metric V-form screw thread of φ6 mm with a pitch
of 1mm. It is not necessary to state whether the thread is le-,
or right-handed, as the convention is it will be a right-handed
single-start thread. In this case, for an M6x1 thread, the tap-
ping size can be obtained from the tables, as having a drill size
of φ5 mm.