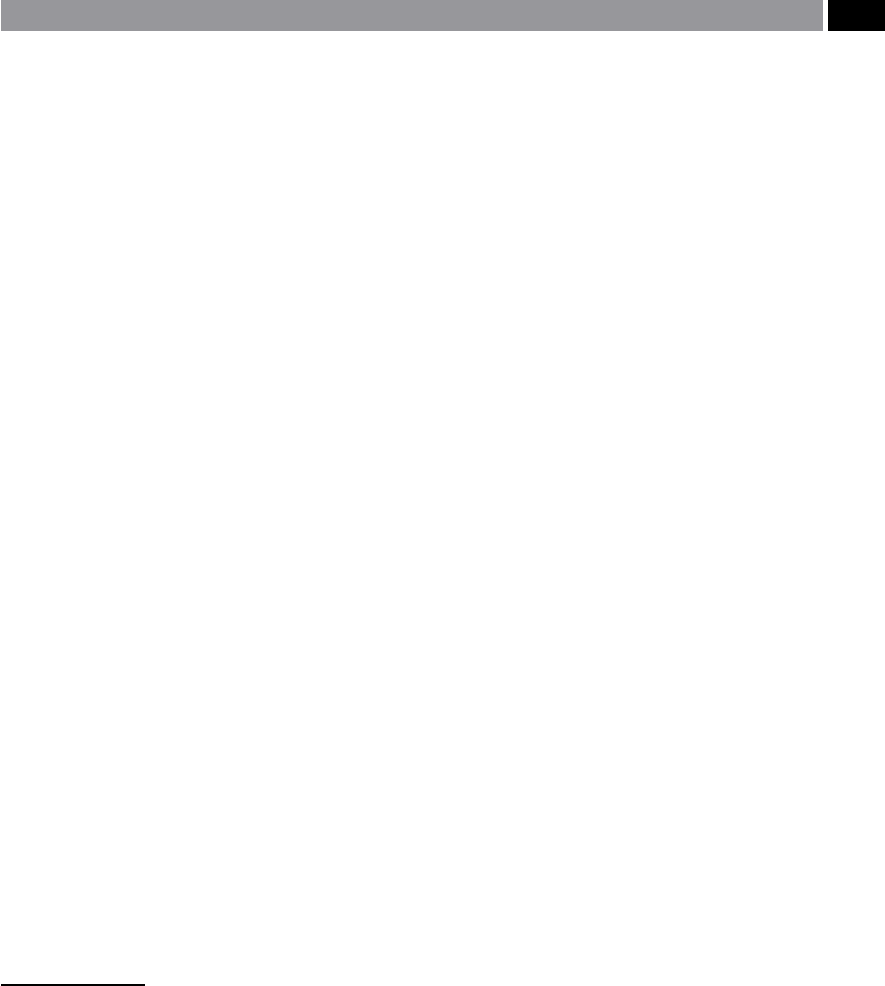
tial economic savings as a result
23
. e main benets
of thread rolling on CNC machine tools, is that due
to this cold-working process, rolled threads have high
strength, are smoother and more wear resistant then
there machined counterparts. e thread rolling pro
-
d
uction rates are fast, typically a complete thread can
be formed in a second, with the thread quality being
consistently high.
A principal characteristic of a thread rolling op
-
e
ration is that the rolled thread’s diameter is always
greater t
han the original blank diameter. If the pro-
spective thread must have an accurate ‘class of t’ , then
its blank diameter is marginally increased by 0.05 mm
with respect to the thread pitch diameter. When it is
desired to have say, the body of a bolt larger than the
outside diameter of the rolled thread, then the thread’s
blank diameter is produced smaller than the body.
5.7.1 Thread Rolling Techniques
In Fig. 111, can be seen the three basic techniques
used to thread roll employed on CNC machine tools,
these are:
•
Two-roll tangential rolling (Fig. 111a), is a similar
process to that of ‘knurling’
24
. As the spindle turns,
the workpiece’s pre-rolled diameter is progressively
raised to its nal shape, normally over the course
of between
2
0 to 30 revolutions. e tangential
thread rolls are fed from the X-axis, at a tangent
to the workpiece. When the centreline of the rolls
line-up with that of the centreline of the workpiece,
the process is complete. Usually rolling a
φ2
0 mm
thread at 1200 rpm, takes about 1 second, con-
v
ersely, a single-point turned thread would require
23 read rolling, is known as a ‘chipless operation’ and as a re-
sult of the ‘cold rolling’ production process , the operation is
cleaner and material savings in blank stock weight are of the
order of between 15% to 20% – depending upon the size and
length of the threaded feature manufactured.
24 Knurling (
i.e not illustrated), utilises either two, or three
hardened rotating knurls which are pressed into the previ-
ously turned outside diameter, thereby giving a ‘gripping’ sur-
face pattern – and hence aids in purchase for one’s grip, with
normally either a straight-, or diamond-shaped knurl.
NB It is possible to utilise tangential sliding knurls to impart
the desired ‘imprinted patterned surface’ onto the workpiece’s
periphery.
10 times longer to manufacture the same threaded
feature,
•
ree-roll radial rolling (Fig. 111b), is similar in
operation to tangential heads, in so far as the work-
p
iece is normally approached from the side, per-
p
endicular to the major thread’s axis. e radial
rolls are sprung-loaded and when they are brought
over the workpiece, the tension is released, causing
the rolls to rotate and produce a thread. Flats on
the rolls allow for work to be inserted and removed.
In both the tangential and radial rolling techniques,
they are limited to thread lengths that are no greater
than the thread roll widths. e principal dierence
between these two heads, is that with
radial heads
t
he form is completed in just one r
evolution, as op-
posed to the 20 to 30 revolutions necessary with
tangential rolling methods. is fact, makes the ra-
dial rolling t
he fastest of all rolling techniques. For
example, if the workpiece spindle is rotating at 1200
rpm, and a φ1
0 mm thread is to be rolled, it would
take just 0.5 seconds to complete,
•
Two-roll axial rolling (Fig. 111c), these rolls engage
the workpiece from its front, along the workpiece’s
centreline (i.e. Z-axis). is rolling action is analo-
g
ous to a threading die, or thread-chaser, traversing
from one end of the workpiece to the other. Hence,
this rolling arrangement is capable of producing
very long threads, or threaded portions on the
workpiece, moreover, the axial heads support the
part during the thread’s manufacture, eliminating
the need of a supporting tailstock.
In all these thread rolling processes, the operation of
thread rolling remains primarily identical in its nal
rolled threaded feature on the workpiece and the pro
-
c
ess of imparting threads on ductile and to a lesser
extent some work-hardening materials, should be en-
c
ouraged. ere are other techniques for the produc-
t
ion of rolled threads that have not been shown here,
including: reciprocating and at die designs, planetary
rolling, etc., they have not been incorporated into this
review, because of the diculty of utilising them on
CNC machine tools.
References
Journals and Conference Papers
Bolden, A. Tapping Troubles: the Hidden Causes. Cutting
Tool Eng’g., 20–25, April 1990.
Threading Technologies 209