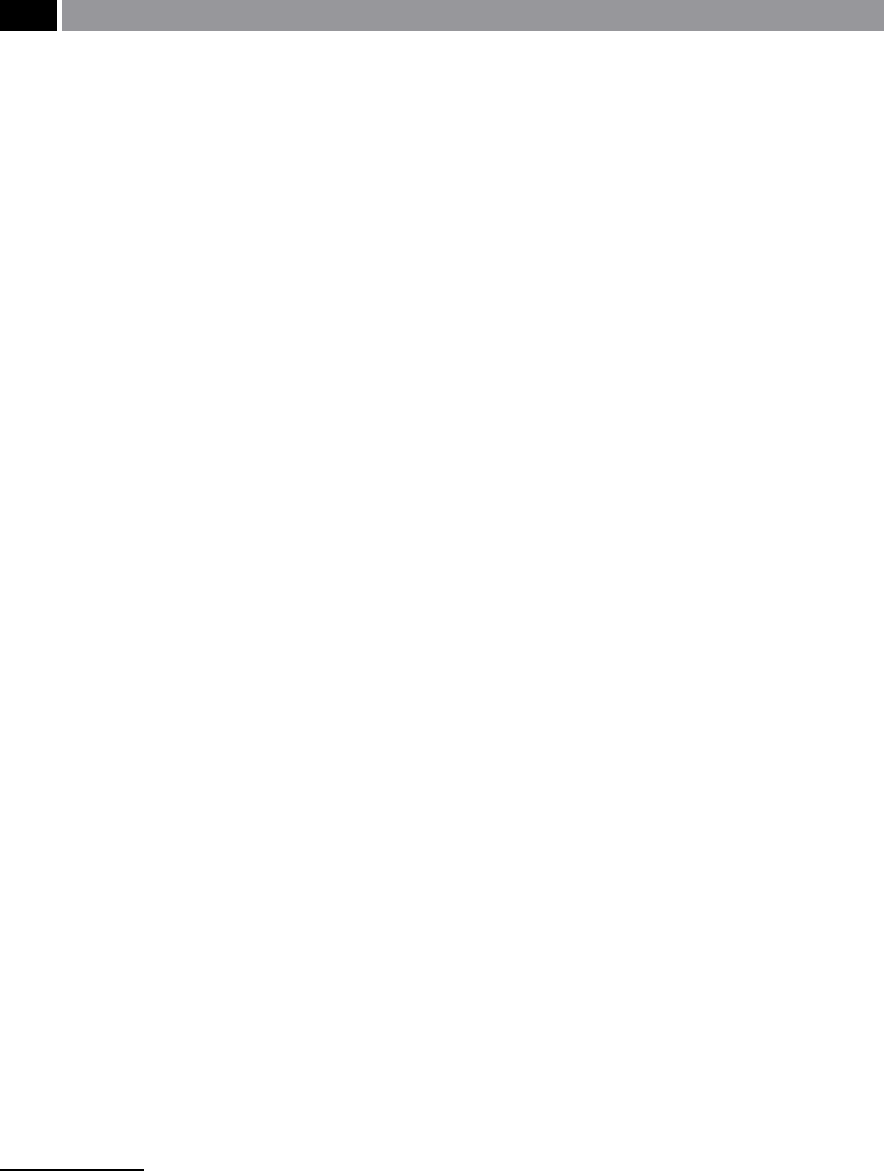
pre-machined workpiece – when producing external
threads – has the exact size for the major diameter re-
qu
ired, conversely, for internal threads this must be
the minor diameter that is pre-machined. Due to the
sharpness of the thread produced by this technique, it
is oen necessary to
‘chase the thread’
17
aerward.
In the case of proled t
hreading inserts, the com-
plete thread prole is cut from a slightly oversized
b
lank. Usually, three distinct proling inserts could be
used in thread production, these are:
•
V-form (Fig. 106bi) – has the ability to machine a
range of thread proles, with the nose radius pre-
c
isely and accurately ground
f
or the smallest pitch
to be cut. As a result of this tightly ground nose
radius, the insert’s life is shorter than with other
proling insert versions, as its size has not been
optimised for individual thread geometries. From
an economic viewpoint, due to the V-form prol
-
i
ng insert’s ability to cut a wide variety of thread
pitches, less inserts need to be stocked,
•
Full-form (Fig. 106bii) – has the ability to prole
the thread’s crest and is therefore manufactured to
exactly the specication of the required thread pro-
le. Such full-prole inserts simplify thread pro-
d
uction, as no prole is deeper than its
s
pecica-
t
ion, allowing them to be a stronger insert thereby
resulting in improved tool life,
•
Multi-point form (Fig. 106biii) – with this multiple-
pointed proling insert, the rst tooth roughs-out
the thread and is therefore slightly set back in com-
p
arison to the second tooth on the insert, which acts
almost like a ‘chaser’ which fully-forms and blends
the various thread proling elements upon the nal
threading pass. Cutting conditions need to be rigid
and stable for this type of insert to operate correctly
– due to its longer cutting edge length. It is essential
to ensure that the recommended in-feed values are
used, to ensure that cutting forces are balanced for
both of the cutting teeth. One advantage of utilising
these multi-point threading inserts is that the num
-
b
er of threading passes can be reduced by almost
50% – as it cuts deeper than its counterparts, when
compared to the single-proling insert forms.
17 ‘Chasing a thread’ , refers to using a chasing tool with the ex-
act thread prole which is utilised to follow the thread along,
thereby deburring and forming the desired prole simultane-
ously.
5.5.5 Threading Turning –
Cutting Data and Other
Important Factors
Whatever type of thread to be cut, whether it is a:
V-form, Multi-start, Trapezoidal, or Tapered, it is gen-
e
rally quite dicult to vary such factors as the: cutting
speed, feed and, to a lesser extent the D
OC
, indepen-
dently of one another, without certain consideration of
some limiting factors. e typical limitations imposed
when cutting a thread, will now be discussed.
Cutting Speed
Typical limitations imposed by the action of cut-
ting a thread include, reducing
t
he cutting speed by
25% – compared to ordinary turning, as the insert’s
shape limits heat dissipation. If a high a chip load
occurs due too great a cutting speed selected, then
the cutting temperature can approach that of say, a
cemented carbide’s original sintering temperature.
As a result of this elevated temperature, the binder
phase may soen, causing potential cutting edge
plastic deformation. e remedy here seems quite
easy, simply reduce the cutting speed, but this may in
-
c
rease the risk of BUE. is BUE may cause the chips
to become welded onto the cutting edge from which
they are
s
hortly fragmented and continuously carried
away – taking a minute portions of the insert’s edge
along with them. e problem can be minimised by
specifying a tougher grade of carbide for the threading
insert, or choosing a multi-coated insert. Normally,
the cutting speeds for any threading operation should
not be less than 40 m min
–1
, when machining with any
cemented carbides.
Feed and D
OC
e feed in millimetres per revolution, must coincide
with the desired pitch, or lead – when cutting multi-
start threads. Hence, if the cutting speed is modied,
the feedrate will also have to be increased, or de
-
c
reased, so that the
f
eed per revolution is constantly
maintained. So, the critical factor here is to achieve
some f
orm of control over the D
OC
when threading.
Each threading pass along the workpiece causes an in-
c
reasingly larger portion of the insert’s cutting edge to
become in contact in the threading operation, accord-
i
ngly, tool forces will proportionally increase. If the
D
OC
is kept constant during several passes, the chip-