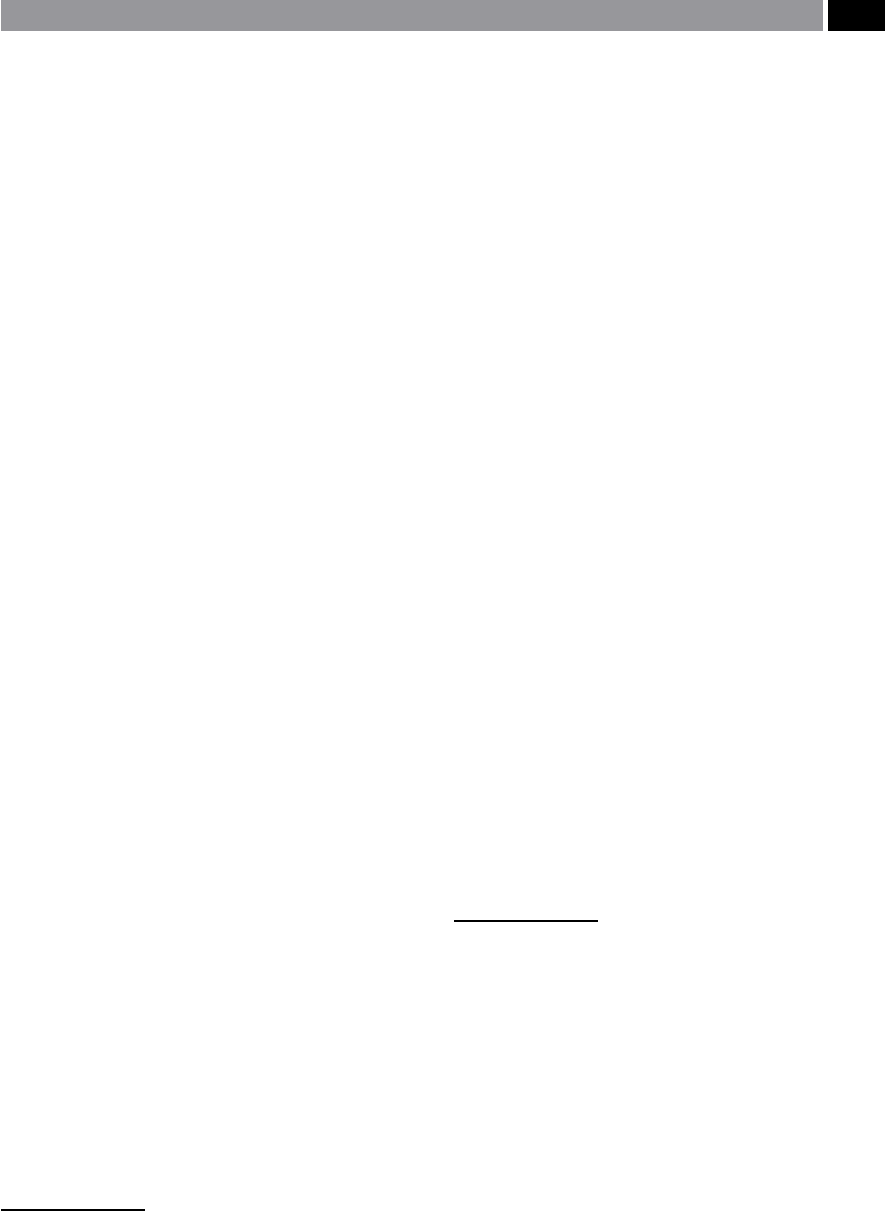
cutting edges should be in-cut at all times. Tooling
manufacturers design and test their cutters during
engagement, carefully determining both the feed and
speed of a milling operation, ensuring that the cutting
forces are eectively balanced-out around all of the
teeth. e machining objective here, is to discover the
optimal chip thickness. As has been previously shown,
milling cutter utes can be either helical, or straight,
with the replaceable cutting inserts being located and
secured by either a wedge, or screw clamp. With each
adjacent cutting edge around the cutter’s periphery be-
ing referred to as its pitch. During a face-milling oper-
ation, a chip is formed at the two cutting edges, where-
upon, it slides up the tooth face and into the ute,
striking the llet, or rounded corner of this ute.
e approach angle is a key milling geometry fac-
tor, being formed the tool’s axis and by the peripheral
edges of either a solid cutter, or its cutting inserts. is
approach angle describes how far the top of the insert
inclines away, from that of being parallel to the cutter’s
axis (i.e. as shown in Fig. 83a). In most general milling
operations, the ‘approach’ ranges from 0° for creating
square shoulders (Fig. 83a-le), to 45° in nish-mill-
ing (Fig. 83a-right). Usually, milling cutter approach
angles ranging between 15° to 45° are the norm, with
a 15° approach enabling deeper cuts to be taken. As
the approach angle of the cutting edge inclination in-
creases, the chip becomes both longer and thinner for
the same D
OC
, or ‘a
e
’ (Fig. 83b), with the load being
spread over longer edge length – resulting in smoother
cutting. Larger insert inclination, enable higher fee-
drates to be employed, although it must be empha-
sised, with shallow cuts (Fig. 83a-bottom).
Taking a dierent milling operational premise, the
o
bjective when ‘rough-milling’ , is to remove the maxi-
mum workpiece stock in the shortest possible time.
e material removal rate being limited by the ‘avail-
able’ spindle power, although this condition can be op-
timised by ‘radial chip-thinning’
19
. e chip thickness
is based upon the calculated feed per tooth (f
z
) and it
diminishes as the radial width decreases and in reality,
creating a lighter actual ‘f
z
’. is ‘lessening eect’ of the
chip thickness, causes the cutting edges to rub, rather
than cut the workpiece material, as a result, the feed
per tooth (f
z
) should be increased as the radial depth
19 ‘Radial chip-thinning’ , is the eect of taking a radial D
OC
(a
e
)
of less than 25% of the milling cutter’s diameter.
decreases. is cutting strategy ‘boost’ in the eective
feed per tooth, provides the twin benets of longer
tool life, with shorter cycle-times.
For any operation in milling involving a ‘chip-thin-
n
ing exercise’ , of paramount importance is the cutter’s
approach/inclination angle (χ). erefore, as the ap-
proach angle (χ) become more inclined from say, 90°
to 45°, the chip thickness, its ‘h-value’
20
decreases (i.e. as
schematically-demonstrated in Fig. 83b). e optimal
chip thickness for a given set of cutting data, can be
entered into a machine tool’s CNC program, by utilis-
ing the following formula:
f
z
= h
m
/sinχ
e chip thickness (f
z
) is always constant, regardless of
the approach angle inclination, be it operated at 90°, or
down to 30°, or indeed, at a atter approach (see Fig.
83b). e exception to this ‘chip thickness rule’ be-
ing when utilising a round, or button-type insert (Fig.
83b-right), as it does not have either a top geometry, or
an edge chamfer, thereby creating the strongest type of
cutting edge. Round inserts without the straight cut-
ting edges associated with other milling inserts, cre-
ate chips that increase in thickness as the D
OC
becomes
deeper. Hence, for round inserts, the average chip
thickness (i.e. its ‘h
m
’ – value
21
), relates to the thickness
of cut this being based upon the insert’s radial engage-
ment of the workpiece via the milling cutter’s diam-
eter. If a comparison is made between a round milling
insert to that of an insert with a 90° approach (i.e. Fig.
83b-right and Fig. 83b-le, respectively), an identical
volume of chips will be removed for both at a set feed
20 ‘h-values’ , for a material group are represented as a range,
with a lower number being the starting value. For example, if
utilising a machining centre with a 35 kW spindle power avail-
ability for the milling of non-ferrous, or aluminium alloys,
the ‘h-value’ , or chip thickness ranges between 0.050 mm to
0.076 mm. Alternatively, using this same machine tool to mill,
either: stainless steels, titanium alloys, or heat-resistant super-
alloys, the ‘h-values’ will range from 0.076 mm to 0.152 mm,
whereas, for: plain carbon steels, cast-/nodular-cast irons the
range will be between 0.152 mm to 0.254 mm.
NB Do not attempt to mill thicker chips than is recommended
in the literature, as this action could result in over-loading the
cutting inserts and breaking their edges.
21 ‘h
m
value-ranges’ for various workpiece materials are identical
to those ‘h-value ranges’ previously mentioned.
Milling Cutters and Associated Technologies 165