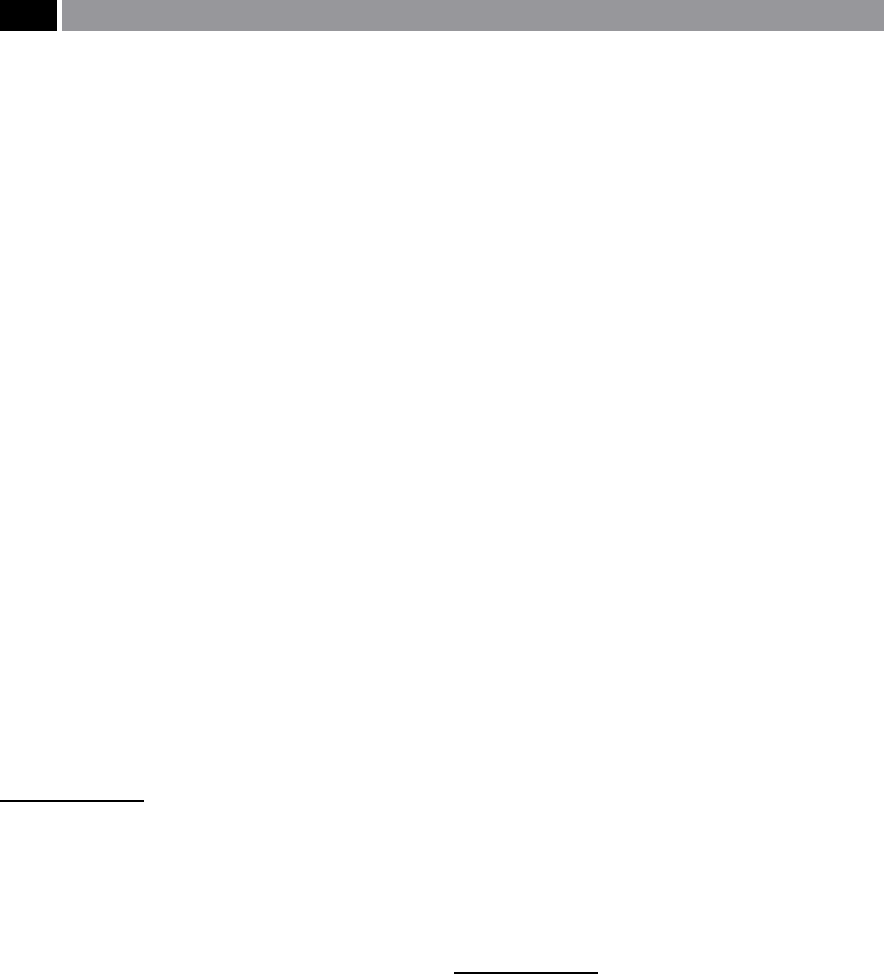
of control of the tooling). Not only is keeping track of
individual tools and their identication, tool-building,
presetting and kitting, together with other tooling-
related problems, becoming an almost impossible task,
particularly when this is exacerbated by companies
attempting to run a JIT
17
philosophy, coupled to that of
an MRPII
18
production scheduling operation.
In the past and, for many ‘traditional’ CNC produc-
tion environments, any form of ‘tool management’ was
generally the province of the machine tool operator.
So, alongside each machine would be situated a limited
kit of tools, these being maintained and replenished
with spares and consumables, via the operator’s liaison
with the tool stores. Hence, a skilled setter/operator’s
main tooling responsibility was to select the correct
tooling, then devise cutting techniques and utilise the
appropriate machining data necessary to eciently cut
the parts. is ‘working-situation’ enabled a process
planner, or part-programmer to treat the machine tool
and operator plus the tool-kit, as a single, ‘self-main-
taining system’ – with a well-established performance.
Such production circumstances, allowed work to be
allocated to specic machine tools, whilst leaving the
detailed cutting process denitions: tool osets, tool
pocket allocation, tooling cutting data (i.e. relevant
speeds and feeds), coolant application, machining op-
erational sequencing, etc., to that of the operator’s pre-
vious skills and knowledge.
17 ‘JIT’ , refers to the manufacturing philosophy of ‘Just-in-time’ ,
where the system was developed in Japan (Toyota – in the
main), to ensure a philosophy and strategy occurred to mi-
nimise time and production wastages. e JIT policy has es-
sentially six characteristic elements, these are:
(i) Demand call – the entire manufacturing system is ‘led’ , or
‘pulled’ by production demands,
(ii) Reduction in set-ups and smaller batches – minimises
time-loss constituents and reduces WIP*,
(iii) Ecient work ow – thereby high-lighting potential ‘bot-
tlenecks’ in production, *work-in-progress (WIP) levels,
(iv) Kanban – this was originally based on a ‘card-system’ for
scheduling and prioritising activities,
(v) Employee involvement – using their ‘know-how’ to solve
the ‘on-line’ production problems,
(vi) Visibility – ensuring that all stock within the facility is
visible, thereby maintaining ‘active control’.
18
‘MRPII’ ,
Manufacturing Resource Planning (i.e. was devel-
oped from MRP) – essentially it is a computer-based system
for dealing with planning and scheduling activities, together
with procedures for purchasing, costs/accounting, inventories,
plus planned-maintenance activities and record-keeping.
Today, with the increasing diversity of work that
can be undertaken on the latest CNC machine tools,
which has occurred as a result of the exibility of
manufacturing in conjunction with reductions in eco-
nomic batch quantities, this has change the pattern of
working. In order to cope with such work diversity,
some ‘
stand-alone machine tools’
19
have acquired a
very large complement of tools. However, a situation
soon develops in which neither the operator, nor the
part-programmer is suciently in control to accept
responsibility for the range of tooling dedicated to any
specic machine tool
20
. So, as a result of a full-deploy-
ment of CNC machine tools, the production organi-
sation related to tooling applications, would normally
change to one in which:
•
e production process is dened separately – be-
ing remotely situated from the shop oor,
•
Machining programs and associated tool list are
produced – these being sent down to both the ma-
chine tool and tool-kitting area via a suitable ‘DNC-
link’
21
, with all of the process data and tooling ‘fully-
dened’.
NB
ere may be some element of doubt concern-
ing the quality of the tooling denition and even
the cutting data produced when the part was origi-
nally programmed.
•
Batch sizes become smaller – the operator is under
increasing pressure to run the given program with-
out alteration, which leads to ‘conservative cutting’
resulting in less-than-optimum machining,
•
Machine operator runs the program with the
minimum of alteration – this means that the ‘ne-
tuning’ of the operator’s past experiences are not
19 ‘Stand-alone machine tools’ , is a term that refers to highly-
productive CNC machines that are not part of an automated
environment, such as either, a exible manufacturing cell, or
system (FMC/S).
20 If the company has
not purchased a computer-aided manufac-
turing (CAM) so-/hard-ware system, then it will not be in a
position to take full advantage of the complex aids for tool-
ing-selection criteria available with many of the more sophis-
ticated CAM systems now currently available.
21 ‘DNC-link’ , is a term that refers to the direct numerical con-
trol, this being associated with a shared computer for the dis-
tribution of part program data, via data lines to remote CNC
machine tools and other CNC equipment in a system.