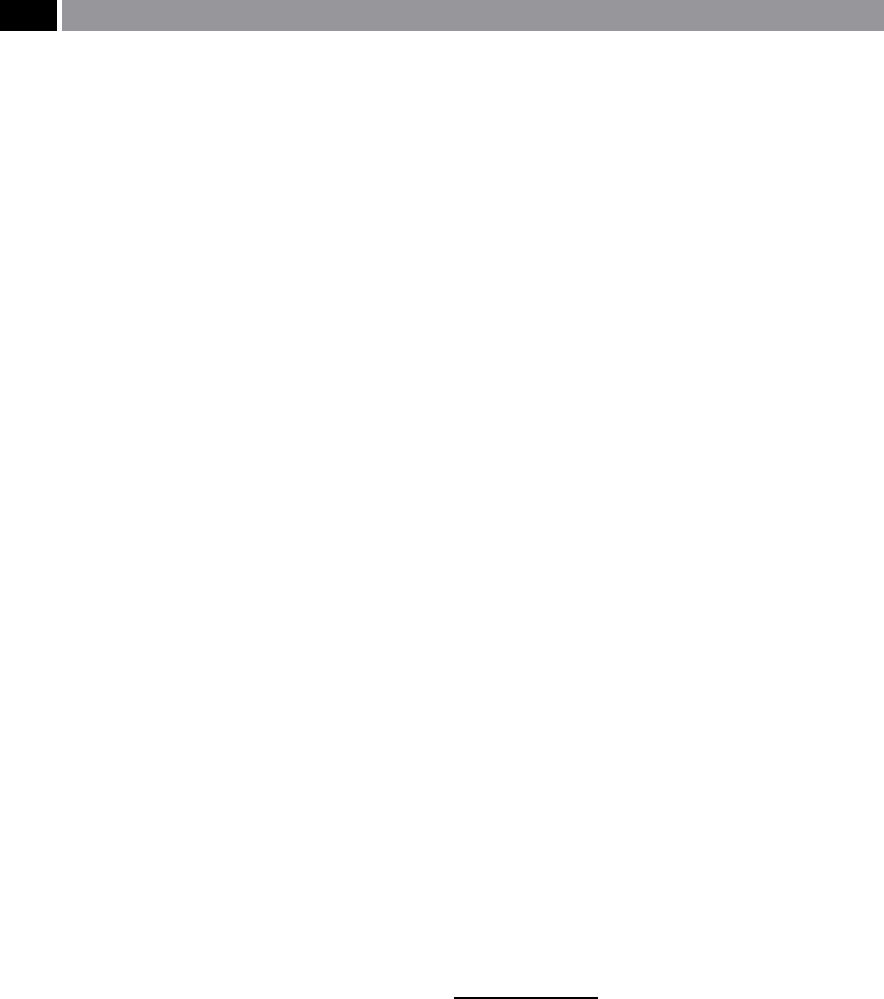
otherwise lead to premature tool breakage. While an-
other note of concern when micro-drilling is its pene-
tration rate. If too high a drill feedrate is programmed,
then the micro-drill will immediately fracture. Some
micro-drilling manufacturing companies either rec-
ommend a single-ute assymetric drill geometry – al-
lowing high chip loads, coupled with an ecient chip
evacuation process, conversely, another approach is to
increase the number of drill utes, but this may cause
chip evacuation problems with ‘sticky’ workpiece
materials. At present, micro-drills can normally drill
holes with L/D ratios of 5:1, but it is anticipated that
these L/D ratios will soon be up to 10:1. In any micro-
drilling operation, the rst few revolutions of the drill
are crucial (Figs. 49 and 50), as the drill’s point expe-
riences eccentric forces as it enters the cut, with any
workpiece irregularities causing the drill to ‘walk’ – re-
sulting in its bending, breakage, or at the very least
some ‘helical wandering’ (i.e axially – see Fig. 70) as
the drill penetrates into the part. In order to mini-
mise the eccentric forces as a micro-drill enters a hole,
many micro-drilling manufacturers recommend that a
pilot hole (Fig. 50b) of between 1-to-2 drill diameters
deep is produced, utilising a short and rigid pilot drill.
A pilot drill’s point angle (
i.e. see Fig. 46 – top) should
have an included angle that is either identical, or
greater than that micro-drill producing the nal hole.
If smaller included angles were selected, as the drill en-
ters the pilot drilled hole, this causes the micro-drill’s
cutting edge to chip. is tool wear-eect is because,
as the micro-drill’s more shallow point angle initially
contacts the previous pilot-drilled hole – with its more
acute angled geometry, as the micro-drill enters work-
piece, this contact will take place at the outer edges of
the lips before the drill point touches the hole’s surface.
In lieu of a pilot-drilled hole, then begin the feedrate
at somewhat less than the nishing feed, or perhaps,
utilise a ‘pecking-drilling action’ – drill to a predeter-
mined depth, partially withdraw the drill, then drill
deeper into the workpiece, once more partially with-
draw the drill, then repeat this sequence. ‘Pecking’ has
the further benet of avoiding dwell at the bottom of a
‘
blind hole’ , this being an important surface integrity
feature with work-hardening materials.
H
ole tolerances that have been satisfactorily micro-
drilled in a range of workpiece materials are of the
o
rder: ± 5 µm, with tolerance-in-roundness (TIR) of
<2.5 µm. By utilising coolant delivery at high pressure,
either through-the-drill, with the ‘larger drill sizes’;
or alternatively ood coolant for minute micro-drills;
usually allows a 30% increase in cutting speeds coupled
to extended drill life. Although care should be made
when utilising through-coolant drills
65
, as their small
coolant hole diameters will simply clog unless the cool-
ant has been passed through s
ome form of micro-ltra-
tion unit, to remove ‘nes’ and other types of potential
clogging debris.
Micro-Mills and Milling
Over the last few years, with the advances in cutting
tool materials in combination with that of cutting tool
technology, has led to signicantly smaller milling
cutter diameters with more complex geometries be-
ing produced (Fig. 255-bottom le). In fact, several
important technologies have developed during the last
decade to assist the cutting tool manufacturers to cater
for the micro-machining industries. Probably the most
important of these new technology applications is the
design and development of very high accuracy six-axis
CNC tool grinding machines, having temperature con-
trol and coolant condition monitoring – these being
key elements in the cutter-grinding process. Grinding
tolerances held by these machines on say, an φ0
.12 mm
ball-ended end mill, must be within <2.5 µm (TIR).
Complementary to these multi-axes CNC grinders,
has been the improvements in diamond grinding
wheel technology, in conjunction with appropriate
grinding wheel metrological inspection techniques,
that have contributed to the signicant advancement
in micro-tool manufacturing quality and productivity.
Whilst continuing our discussion on the cutting tool
material front, micro-milling cutters are now being
produced from extra-ne grain cemented carbides, al-
lowing sharp cutting edges in conjunction with good
milled surface nishes. For example, one Japanese mi-
cro-tooling manufacturer oers a standard range of
‘
micro-mills’ , from: φ5 µm to φ5
5 µm; in incremental
65 ‘Ethanol’ , is an alternative applied lubrication strategy, to that
of either the usual water-based ood coolant method, or by
through-the-tool delivery. Here, ethanol is a form of alcohol,
occurring naturally in the sugar fermentation process, its
benets are that it has less-than-water viscosity, enabling it to
penetrate into the tool/chip interface in a superior fashion to
that of other coolants. Ethanol is usually delivered to the cut-
ting zone in the form of a spray-mist. While another bonus
of the application of ethanol is its low evaporation point, giv-
ing it eciency in cooling and as a lubricating agent for tool
spindle speeds (i.e. of up to and including) >60,000 rev min
–1
.
Moreover, ethanol simply evaporates and this eect negates
any disposal costs, while it provides a slight ‘chilling-eect’ on
the part, minimising thermal growth problems on miniature-
sized components.