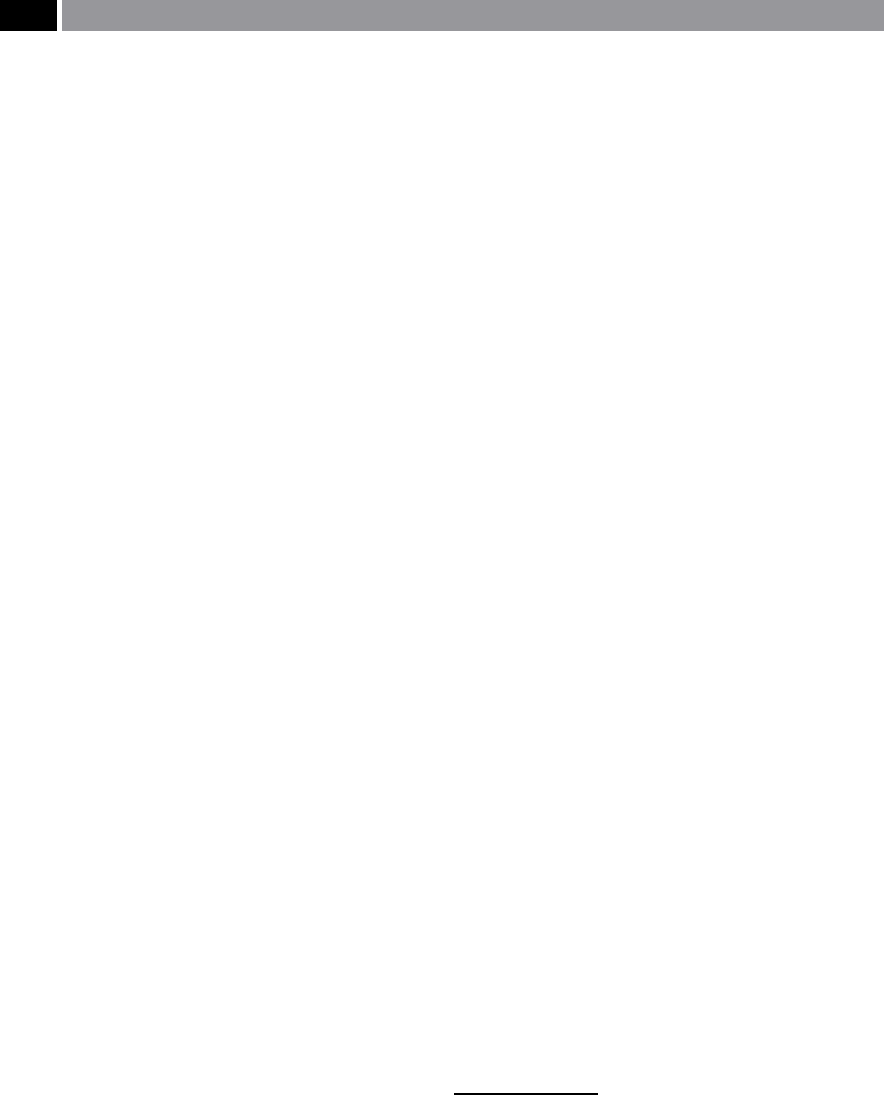
eect of less additional stock produced by round in-
sert’s on the workpiece prole, is shown schematically
in both Figs. 247ai and aii and, should be compared to
Fig. 246a – this latter eect being the result of utilising
square-shouldered cutting inserts, in terms of stock to
be removed later in semi-nishing operations.
Amongst the notable benets of using round inserts,
are that they produce a variable chip thickness, which
allows for higher feedrates if compared to other insert-
shaped geometries. Round cutting inserts provide a
v
ery smooth cutting action (i.e see Fig. 246 – bottom
right: inset), because the entering angle changes from
almost zero – in the case of very shallow D
OC
’s, to that
of 90° – under certain conditions with the larger D
OC
’s.
us, at the maximum D
OC
, the entering angle is 45°
and when copying with the periphery, the angle is 90°.
is D
OC
variability using round inserts, also goes some
way in explaining why these inserts are so strong in
comparison to other insert shapes. Namely, round in-
serts with their actual ‘work-loading’ – at the cut’s ini-
tial progression – is successively built-up, rather than
almost immediately with inserts having greater enter-
ing angles, usually provided by their less-than-robust
geometry counterparts. Consequently, round inserts
should always be regarded as the primary choice in
cutter selection when either roughing, or for medium-
roughing operations. When 5-axis machining, the use
of round cutting inserts can be usefully exploited, as
they have virtually no limitations when machining
sculptured surfaces. erefore, with optimum CNC
programming, either round inserts, or toroid-shaped
milling cutters can normally be substituted for ball-
nosed end mills (Fig. 79b), as they can oer: superior
cutting performance; improved chip-breaking e-
ciencies; as well as better chip evacuation; this latter
point is important when deep cavities might otherwise
retain work-hardened swarf. Typically, the increases
in productivity range between 5-to-10 times better,
if compared to that of previously utilising ball-nosed
end mills. Round insert tooling is very rigid so as a re-
sult, they only produce a small amount of run-out and,
when combined with ground, positive and light cut-
ting geometries, may be used for semi-nishing and
o
ccasionally some nishing operations (Fig. 246 – bot-
tom right: inset).
Some of the main questions to be answered re-
garding the correct application of technology is con-
cerned with optimising: the cutting data; likely insert
grades; together with their geometries; in relation to
the: specic workpiece material to be machined; actual
machining operations to be undertaken; anticipated
productivity requirements; and the likely workhold-
ing restaint/security issues. Die and mould work in-
variably involves complex sculptured male and female
surfaces, with any calculations of the eective cutting
s
peed being based upon either the ‘true’ , or eective
diameter in-cut (‘D
e
’ – see Fig. 247b). So, if the D
OC
is
very shallow – as is the case when semi-nishing op-
erations are being carried out, then the ‘true’ cutting
speed will be much lower (Fig. 247b). If the original
cutter diameter was chosen for the cutting data calcu-
lations, then for a shallow cut – due to ‘D
e
’ being the
eective diameter, this drastic reduction in actual cut-
ting speed will not have been anticipated, causing the
feedrate utilised to be severely compromised, as it is
dependent on the calculated cutter’s rotational speed.
is will not only severely impede component produc-
tivity, but will increase the tool’s potential wear-rate
signicantly, this being the case for all round insert
cutters, ball-nosed end mills, plus end mills having
large corner radii. Due to the adverse and miscalcu-
lated cutting data, there is a likelihood for premature
cutting edge frittering and chipping – created by too
low a cutting speed and localised heat in the cutting
zone. When undertaking either nishing, or super-n-
ishing of the die and mould sculptured surfaces (Fig.
246biii) on hardened tool steel, it is vitally important
to choose tool materials and coatings with ‘hot hard-
ness’ capabilities
45
.
A major factor to consider when milling for either
nishing, or super-nishing hardened steel sculptured
surfaces by HSM, is to take shallow cuts. Notably, the
D
OC
should not exceed 0.2/0.2 mm (a
e
/a
p
– Fig. 247b).
is strategic machining decision should be made, so
that excessive deection of the cutting tool assembly is
avoided, enabling a high tolerance level and geometric
accuracy to be held on the die, or mould. Accordingly,
very sti tool assemblies are essential, usually utilising
solid cemented carbide: due to its inherent stiness;
coupled with the maximum core diameter possible;
that the die, or mould part features will allow.
45 ‘Tool materials for: hardened steel milling’ , they are usually
coated cemented carbide, with the micro-grain structural
matrix (i.e. typical grain size being <1 µm), providing good
wear resistance and transverse rupture strength (i.e. this be-
ing ‘related’ to its toughness). Coatings can include: titanium
aluminium nitride (TiAlN); titanium carbonitride (TiCN);
having multiple coatings of between 2 to 12 µm thick, applied
by Plasma Vapour deposition (PVD). Diamond-like coatings
(DLC) are also utilised. (Source: Dewes and Aspinwall, 1996)