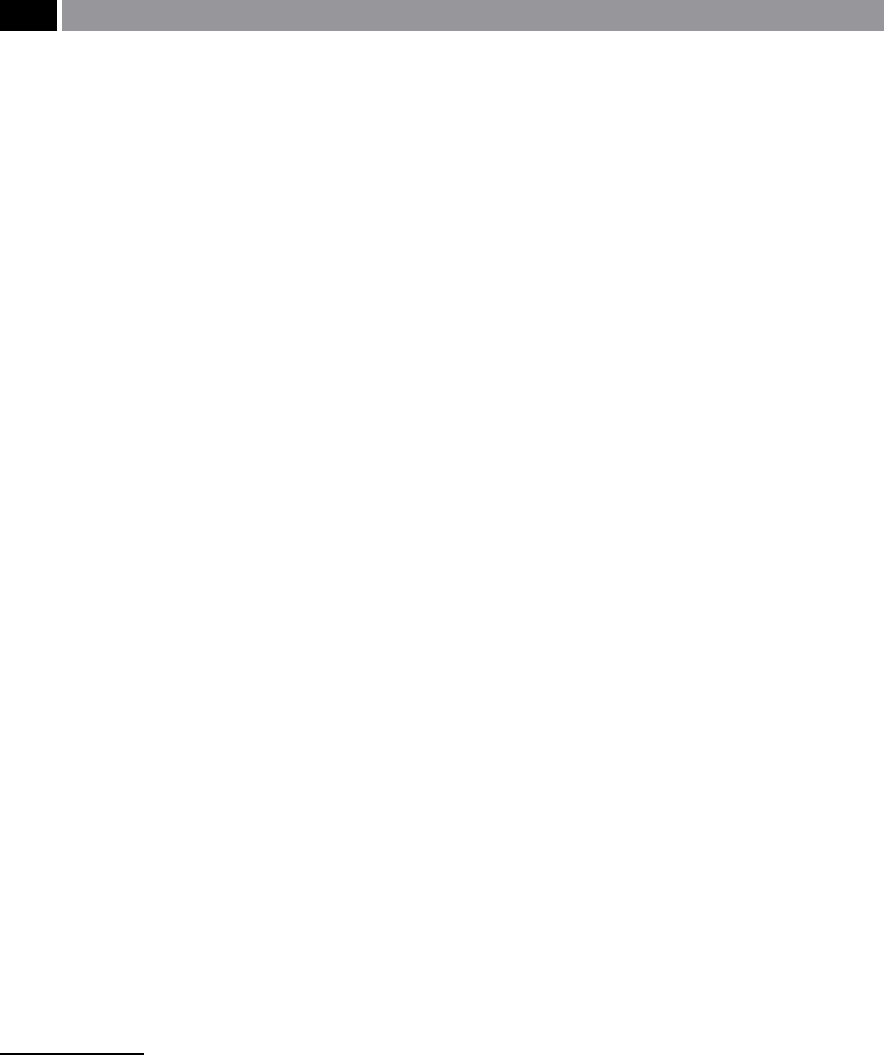
N = maximum rotational speed of tooling assembly
(rev min
–1
);
F =
force (N).
When the above equation for cutter unbalance is
utilised, for these tooling assemblies, utilising the fol-
l
owing values: G = 2.5; M = 4.294; N = 6,000; which
then gave an allowable imbalance U = 17.9 g-mm. is
level of imbalance means that the cutter’s mass can-
not rotationally shi by more than 17.9 g-mm, if it is
to maintain dual-plane balance at a peripheral speed
of at least 3
,000 m min
–1
. In fact, two identical cutter
assemblies were designed and manufactured, hav-
ing a BT40 taper tment – for the vertical machining
centre (i.e. Cincinnati Milacron Sabre 500). In order
to maintain both structural rigidity and integrity,
the complete cutter bodies and their associated ta-
pers were each produced from single stock of EN24T
steel. Aer precision turning and milling the complete
bodies and insert pockets, these cutters were nitride-
hardened
29
to HR
C
52, prior to a ‘very light-grinding’
process and then balancing. e four cutting insert
pockets were equally-spaced (pitched) and the but-
ton-style cemented carbide inserts were: φ1
2 mm by
4mm thick, single-sided and TiN-coated (Stellram:
RPET 1204 DFZ). e insert pocket geometry had a
11° toe angle with a neutral geometry. Button inserts
were selected as they give the strongest shape cutting
geometry available (see Fig. 23), producing an innite
approach angle to the workpiece (see Fig. 83b), thus
minimising impact load at entry to the cut while of-
fering multiple cutting edges – when subsequently
turned in their seatings. As one might expect, insert
security is vitally important, due to the great centrifu-
gal eects and applied cutting forces. Due to the pre-
vious nitride-hardening process, hardened insert seats
were unnecessary, once the retaining screws had been
‘torqued-up’ locking and then sealing them – for se-
29 ‘Nitride-hardening’ , produces a very hard surface with a
soer and tougher matrix. e UHSM cutters were held in a
pressure-tight furnace and heated to between 500-550°C for
some hours in an ammonia gas*, allowing the nitrogen atoms
to diuse into the surface and to form ne stable nitride pre-
cipitates with aluminium constituents, allowing the nitrided-
steel surface to be precipitation- hardened. No subsequent
heat-treatment is necessary.
*Approximately 30% of the ammonia disassociates ( NH
3
→
←
3H+N) and part of the nascent nitrogen is absorbed by the
surface layers of the steel. (Source: Cotrell et al., 1979)
curity. e actual seatings for the inserts had consid-
erable body-support around their periphery, just hav-
ing a working-clearance at the insert’s cutting region.
ese UHSM face-mills were extremely compact, with
the minimum stand-o height from the cutter’s gauge
line (i.e. see Fig. 236), which reduced the eects of the
previously mentioned ‘rigidity rule’.
Due to the relatively large diameter and weight of
these face-mills and the fact that the machining centre
had limited spindle power, these cutters could, if used
a
ppropriately, exploit the ‘mass’ , or ‘ywheel-eect’ of
their weight in conjunction with rotational speed to
‘store inertia’. So, when the spindle power is restricted,
cutters with high mass must be taken up to their de-
sired rotational speed in a progressive manner, other-
wise they are likely to ‘trip’ a ‘spindle over-load’ in the
CNC controller. is steady and progressive increase in
t
he cutter’s rotational speed occurred at 500 rev min
–1
increments – dwelling for several seconds to minimise
inertial power overload, between increases to the de-
sired peripheral speed. Due to the machine tool hav-
i
ng a maximum spindle speed of 6,000 m min
–1
, this
equated to a peripheral cutting speed of 3,000 m min
–1
,
with the face-mill having 0.5 m cutting circumference.
Once the cutter has reached its top speed, it can then
be rapidly progressed (i.e. fed) across the workpiece at
a
rate of 20 m min
–1
. In this case the workpiece ma-
terials were a range of stainless steel alloy testpieces
(Fig. 236). Aer rapidly face-milling these ‘stainless
t
estpieces’ , the cutter’s rotation was decremented in
500 rev min
–1
intervals until stationary. e cutter once
stationary, could have its edge wear (inserts) assused
and workpiece milled surface texture and surface in-
tegrity could be inspected and investigated.
One factor to bear in mind concerning UHSM with
large face-milling cutters being utilised for their ‘in-
e
rtial eect’ , is to design them without driving dogs.
If these ‘dogs’ were tted, not only can they introduce
out-of-balance eects, but tend to signicantly disrupt
the air-ow and introduce alarming and high noise
factors. is aspect of cutter design is important, if
the cutter cannot ‘cleave through the air’ with aerody-
namic eciency, turbulent air ow will result and op-
erational noise becomes excessive. One problem that
these particular cutters did not suer from (i.e despite
the conventional taper-cone angle) – unlike many of
their higher rotational speed counterparts, was ‘spin-
d
le nose swelling’ , which can cause a lack of regis-
ter if the taper tment connection is not of either the
double-, or triple-contact face-and-cone types. One
unexpected aspect of employing such large face-mills