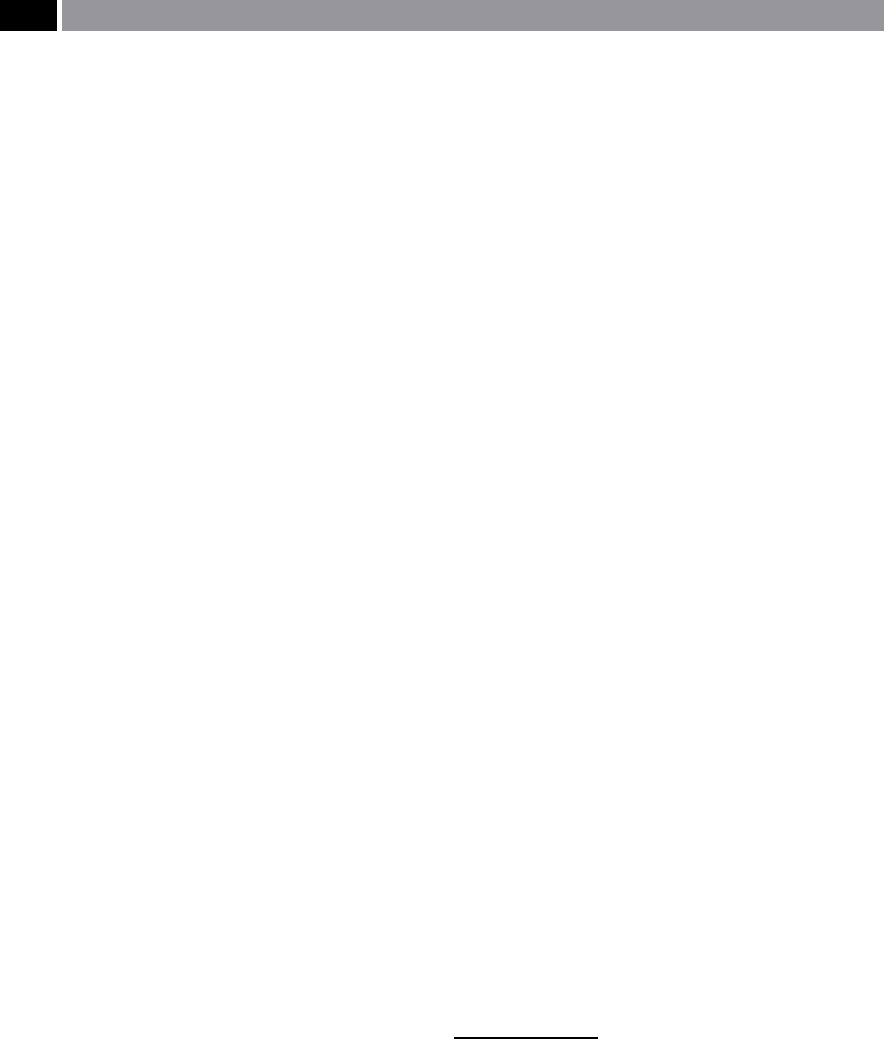
a hob will more than likely have very ne detailed
work on its surface, perhaps with radii as small as
0
.25 mm, requiring a tool tip radius of 0.025 mm.
In order to machine the button’s elaborate features
with such a small milling cutter, the spindle speeds
m
ight need to reach 40,000 rev min
–1
, utilising a
feed per revolution of 0.008 mm, giving a feedrate of
320 mm min
–1
. Many production engineers would
not consider this as an example of high-speed mill-
ing, but let us look more closely at this particular
machining problem. If the controller has a servo-
g
ain of 4, with a feedrate of 320 mm min
–1
, this
means that the servo-lag would be 0.75 mm min
–1
,
which is consistent with milling radii of 0.25 mm.
However, if the servo-gain was 1, this would cause
a
servo-lag of 0.320 mm min
–1
and in this case, it
obviously could not machine that button’s intri-
cate detailing. In such circumstances, it would be
necessary to appreciably reduce the feedrate to
s
ay, 75 mm min
–1
to generate the button’s contours,
leading to the cycle-time increasing by 400%. Let
us also now consider the impact of block process-
ing time under these conditions. To mill a radius as
s
mall as 0.25 mm, we would need to produce linear
stroke lengths of just 0.075 mm – to reproduce ac-
ceptable button detailing. is intricate contouring
w
ork requires a block processing time of 15 ms. If
the CNC controller has a block processing time
o
f just 60 ms, then the feedrate must be limited to
7
5 mm run
–1
which again, increases milling time by
a factor of four.
2. E
CM pattern electrode for a Turbine fan (i.e large
aluminium casting) – here, the electrode’s geom-
etry has very gentle three-dimensional curves. In
this situation the chosen CNC machine tool’s mill-
i
ng spindle has a 250,000 mm min
–1
capability, cou-
pled to adequate power to cut at a feed of 0.25 mm
rev
–1
. is production requirement produces a feed-
rate of 62,500 mm min
–1
(i.e. being the product of:
250,000 x 0.25) would be possible. For accuracy
and precision, a chordal deviation (C
d
) of 0.005 mm
would indicate a stroke length of 0.75 mm – if the
minimum radius of curvature for the Turbine fan’s
g
eometry was 25 mm. Assuming that the servo-
gain of 1 was available, then we would obtain errors
a
s large as 0.125 mm and with such errors, the ma-
chine tool would not produce an acceptable part.
F
urther, at 62,500 mm min
–1
, if the block process-
ing time (T
b
) was 60 ms, this ‘timing’ would require
stroke lengths of 2.5 mm instead of the 0.75 mm we
needed for the required accuracy and precision.
erefore, in order to eliminate the eects of low
gain, or slow processing time, it is necessary to de-
press the feedrate, resulting in the cutting time be-
ing increased up to 400%.
When considering these two practical examples from
a metaphorical sense, the former method can be com-
pared to that of racing a go-kart on a small tight track,
while the latter method is similar to a highly tuned
sports car racing on a longer and smoother track. e
g
o-kart may only reach speed a of 30 km h
–1
, whereas
the sports car may hit speeds of >200 km h
–1
. e
corner forces and reaction times are similar for both
methods, even though the speeds are vastly dierent.
Looked at from yet another viewpoint, we can say that
the frequency of response of both the drive and car,
that is their servo-gain and processing time, are very
s
imilar in both examples even though the speeds (feed-
rates) are radically dierent.
In the day-to-day production environment, the du-
plication of specic and precise contours is the end re-
sult of a combination of many inter-related factors. As
the number of machine tool axes required to produce
sculptured part surfaces increases, the diculty of ob-
taining the desired prole also becomes proportion-
ally problematic. So, machine tools that would nor-
mally produce excellent general-purpose machining
work, may not be either accurate, nor ecient enough
to manufacture complex part contouring geometries.
at is, unless their CNC processors can achieve block
p
rocessing speeds of <10 ms, with servo-system gains
of up to 4, having sucient ‘look-ahead’
16
capabilities
(i.e. see Fig. 222g) that are required, for any realistic
and practical HSM applications.
16 ‘Look-ahead’ facilities, are when the controller has the abil-
ity to look-ahead through the following sequenced program-
ming blocks* to determine successive motions and actions
– an important feature for any HSM applications. Many of
today’s sophisticated CNC controllers can look-ahead through
a considerable number of these blocks, thereby prompting the
controller’s response, prior to undertaking any command exe-
cutions. *A ‘Block’ can be dened as: A set of words, characters,
digits or other elements handled as a unit – hence, the term
‘block’ – which creates a sequence of lines of a computer pro-
gramming language, that can then be activated upon by the
machine tool‘s CNC controller, producing the necessary pro-
grammed-actions. (Source: Smith et al., 1993)