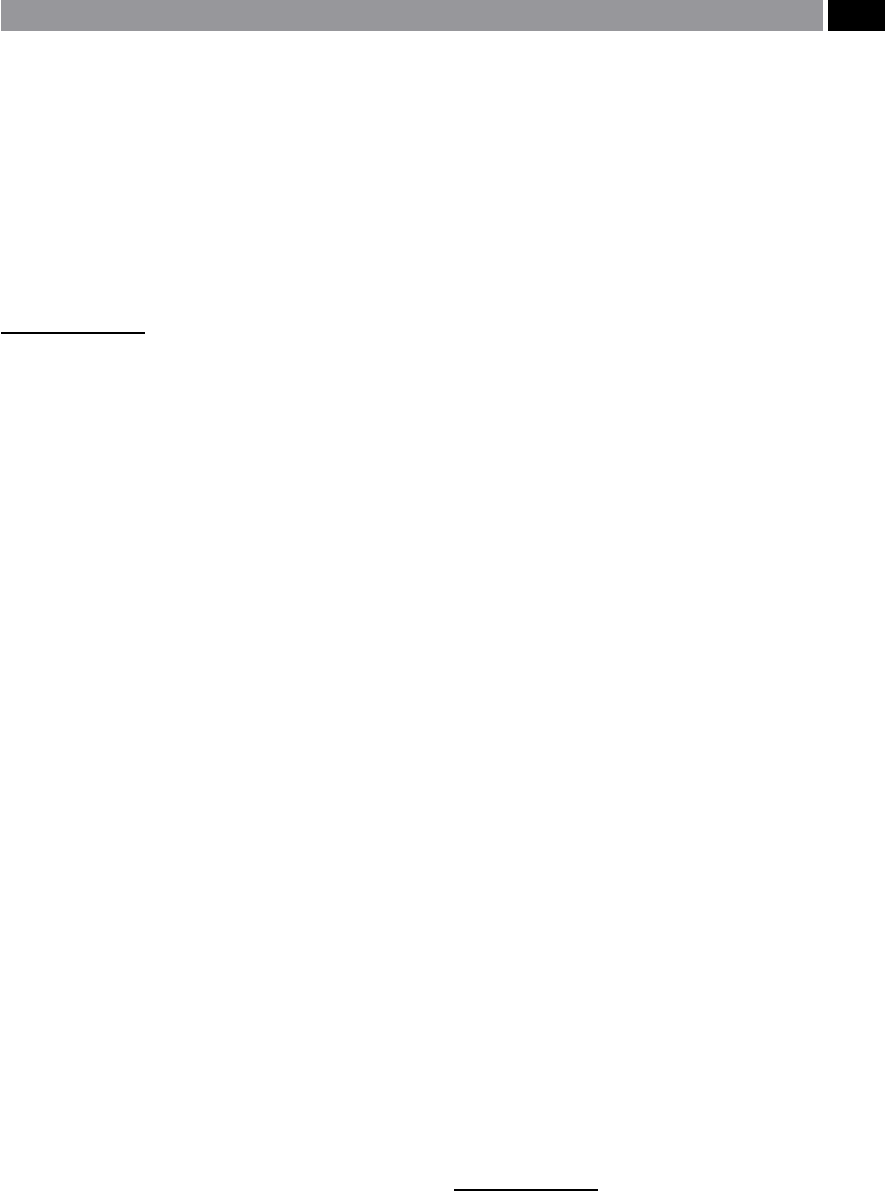
7 µm. However, if linear encoders are tted this mini-
mises any potential ‘ballscrew wind-up’ , although the
problem of an ‘
Abbé -error’
7
is still present.
Yet another source of machine tool-induced prob-
lems are more specically termed ‘
uncertainties’
8
,
while ‘
hysteresis’
9
can also contribute to the overall ‘er-
ror budget’. us, hysteresis may result when the same
position has been commanded by the CNC controller,
7 ‘Abbés Principle’ – was derived by Professor Ernest Abbé in
1890 (i.e. having studied and graduating from the University
of Jena) and is still valid today. e Abbé principle simply
states that: ‘e line of measurement and the measuring plane
should be coincident’. An example of this ‘Abbé Law’ well-
known to engineers the world over, shows that a conventional
micrometer calliper ‘virtually-obeys’ the ‘Abbé principle (i.e.
there is a small ‘cosine error’ present – which can usually be
ignored), whereas, the Vernier calliper has a much larger o-
set between the xed and moving jaws – where the compo-
nent being measured is situated, to that of the beam – where
the scale’s reading for this measurement is taken. Ideally, both
measurement and reading should be lined-up, without an o-
set. [Sources: Busch, 1989; Whitehouse et al., 2002]
8 ‘Uncertainty of machine tool positioning’ – the question oen
asked in calibration-related tasks, is: ‘What is measurement
uncertainty?’ Uncertainty of measurement refers to the doubt
that exists about any measurement; there occurs a margin of
doubt for every measurement. is expression of measure-
ment uncertainty raises other questions: ‘How large is the mar-
gin?’ and ‘ How bad the doubt?’ Hence, in order to quantify
uncertainty two numbers are required: (i) being the width of
the margin – its interval, (ii) plusits condence level.
NB
is latter value states how sure one is that the actual
value occurs within this margin.For example:On a CNC ma-
chine tool, the command may be to move the X-axis slide-
way 1000 mm plus, or minus 0.05 mm at the 95% condence
level. is uncertainty could be expressed, as follows: X-axis
slideway motion = 1000 mm ± 0.05 mm, at a level of con-
dence of 95%. In reality, what this statement is implying to
either the programmer, or calibration engineer is that they are
95% sure that the actual X-axis position now will lie between:
999.95 mm and 1000.05 mm. Many factors can contribute to
the overall ‘error budget’ as it is sometimes known, but this is
beyond the scope of the present discussion – see references for
further information. (Smith, 2002)
9 ‘Hysteresis’ ,
can be dened as: ‘e dierence in the indicated
value for any particular input when that input is approached in
an increasing input direction, versus when approached in a de-
creasing input direction.’ (Figliola and Beasley, et al. 2000)For
example:Hysteresis usually arises because of strain energy
stored in the system [i.e. in this case, within the machine
tool], by slack bearings, gears, ballscrews, etc. (Collett and
Hope, 1979)
but from opposite directions, causing the motion sys-
tem to creep by an amount larger than the backlash
alone (i.e. the hysteresis). is eect is the result of un-
seen working clearances and compounded by the ma-
chine’s elastic deformations, although by pre-loading
the ballscrews it will minimise some of these eects.
In HSM machining applications, all ballscrew and
indeed any screw-driven systems have some additional
limitations, such as its ‘critical speed’ of rotation. At the
critical speed, a ballscrew starts to resonate
10
at its rst
natural frequency (i.e termed ‘whipping’). Hence, the
critical speed is proportional to the ballscrew’s diam-
eter and is inversely proportional to the distance be-
tween the screw’s supports – squared. For a very long
and slender screw-driven machine tool application
with wide supports, here, most recirculating ballscrews
w
ould have a critical speed of approximately 2,500 rev
min
–1
. It should also be said, that for many ballscrews
assemblies they can be rotated at higher rotational
s
peeds than the 2,500 rev min
–1
previously mentioned,
before they reach their critical speed, but for very fast
accelerations and decelerations, then they become in-
creasing challenged. In fact, on some HSM machine
tool congurations, multi-start ballscrews have been
employed to increase linear response, but here the
‘critical speed’ will probably be lessened – due to re-
duced inherent ballscrew stiness. Even ‘matched’ twin
ballscrews have been tted to HSM machine tools – to
minimise any potential ‘yawing motions’ at high lin-
ear speed by the moving member along the machine’s
bedway. ese ballscrew limitations are probably why
linear-motional drives are becoming a realistic alter-
native, but they are only tted at present, to high capi-
tal cost HSM machine tools.
One of the bi-products of HSM’s greater stock re-
moval rates, is the excess volume of hot swarf which
must be speedily and eciently removed from the vi-
cinity of the machine – which is more readily achieved
for horizontal machine tool congurations. er-
mal eects in general on any machine tool become a
problem, particularly as many milling spindles utilise
direct-drives, with the motor being mounted in-situ
with the spindle. Here, the spindle motor creates heat,
the thermal eects of which can be analysed by either
10 ‘Resonant frequency’ , can be dened as: ‘e frequency at
which the magnitude ratio reaches a maximum value greater
than unity.’ (Figliola and Beasley et al., 2000)
Machining and Monitoring Strategies 439