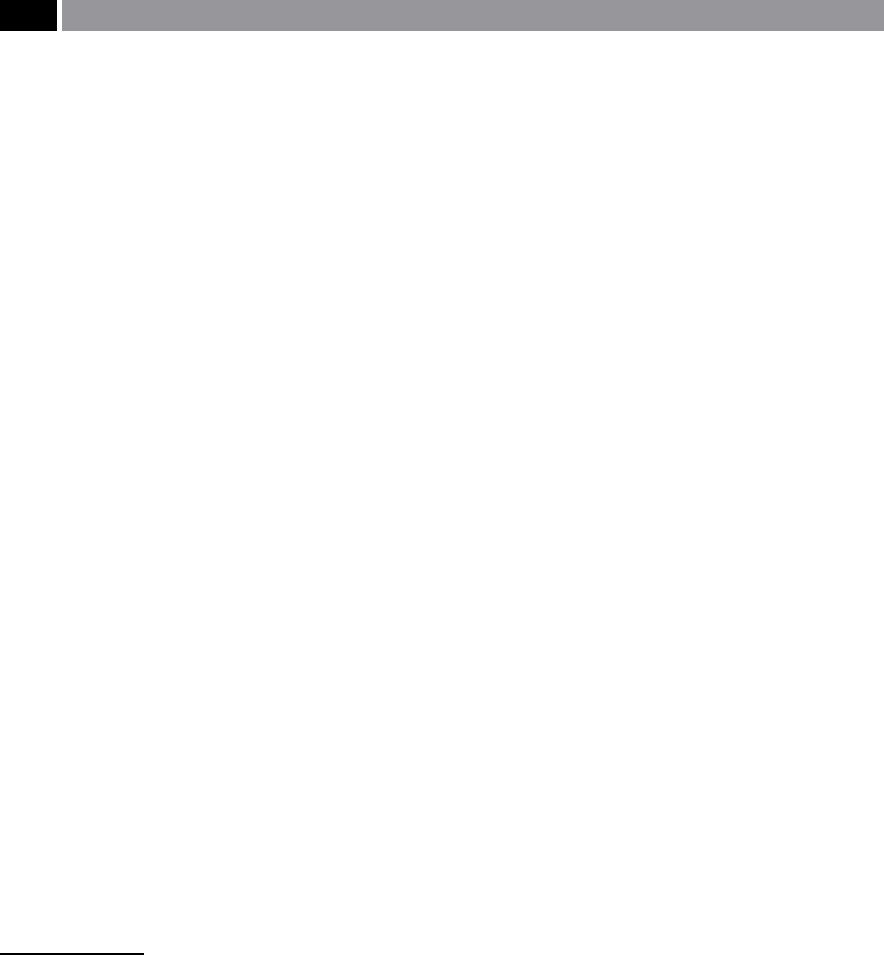
•
Protection of people and the environment – to
what extent are the personnel exposed to cutting
uids: before; during; and aer use? Are there local
constraints on uid disposal?
e above criteria concerning cutting uid selection,
can be sub-divided into two distinct groupings – com
-
m
ercial and production, as follows.
Commercial Criteria
e commercial criteria determine the ‘weight’ to be
given to various production decisions. For instance, if
the time factor is more important than the cost factor,
then higher cutting speeds will be used and so the de
-
m
and placed on the cutting uid will be greater. If, dif-
f
erent materials and types of machining
p
rocesses are
involved in the production process, then a ‘universal’
cutting uid might be a better choice than a number of
dierent uid products, even if the latter uid compo
-
s
itions individually produced a better performance.
Production Criteria
In either one-o, or batch production, individual
machines tools are likely to have their own separate
cutting uid supply, however in a mass production
environment, uid centralised systems are the norm.
e production criteria for the choice of cutting uid
includes the: type of machining process; cutting con
-
d
itions – workpiece material, cutting data, tool mate-
r
ial, etc., together with the machine tool type and its
conguration
18
. us, on the basis of these produc-
tion-based decision criteria, an initial choice will nor-
18 ‘Machine tool conguration’ , take for example, the case of
an ‘orthogonal’ * machining centre, it relates to whether the
machine has a horizontal, or vertical spindle orientation, with
one, or multiple spindles present, having three, four, or mul-
tiple linear and rotary axis control and of the conventional,
or high-speed machining (HSM) variety. Most machine tools
today fall into the ‘orthogonal’ machining category, but some
‘non-orthogonal’ machining centres exists, which oer con-
tinuous kinematics that have multiple-axis control – for even
simple straight-line motion, oen available with omni-direc-
tional spindle orientations – for ease of cutter access to say, a
complex, or sculptured machine part geometry.
*Orthogonality of axes means that each axis is positioned at
90° with respect to each other, such as on a three-axis verti-
cal machining centre (i.e. X-, Y- and Z-axes, with the Z-axis
normally incorporating the machine’s spindle).
mally be made regarding the type of cutting uid to
be used – whether it is an aqueous-, or oil-based uid
type that is required.
8.7.2 Selection Procedure
When selecting a cutting uid, it is important to take
the uid manufacturer’s instructions into consider-
a
tion. If their recommendations are ignored, it may
render any previous guarantees invalid. Many of
these cutting uid manufacturers
s
pecify that certain
products be utilised, normally only applying them to
either special machining circumstances, or where dif
-
cult cutting conditions are likely to be encountered.
Equally, other cutting uid producers only specify the
general type of instructions, such as: what type of cut
-
t
ing uid to employ, for example, aqueous, or not, to
be used, on the contrary, some uid manufacturers do
not specify anything! Usually it is possible to rely on
the manufacturer’s specication tables which indicate
their most suitable product for a particular range of
machining operations. However,
before c
onsulting a
cutting uid manufacturer’s set of tables, the follow-
i
ng
f
actors must be either known, o
r established. ese
crucial decisions include:
•
Type of machining operation – care must be taken
to ensure that correct and ecient planning of the
machining strategy for the successful completion
of the part is known and, the optimum machining
techniques to achieve this objective are conrmed,
•
Water characteristics – hard/so, chloride, sul-
phate, bicarbonate content has been both tested
and accurately established,
•
Type of workpiece material to be machined – with
due regard to machining of: work-hardening mater-
ials, or ‘sticky’ materials – aluminium and copper
alloys, etc.,
•
Type of machine tool ltration system – having ei-
ther: no ltration; sump
o
nly; paper lter; centri-
f
uge; etc.
NB I
n the case of the centrifuge, semi-synthetic
products are not r
ecommended, while washable l-
ters should only be utilised with synthetic, or semi-
synthetic products.
As a general ‘rule of thumb’ , emulsions with EP addi
-
t
ives should be employed for heavy cutting work, whilst
synthetic products are normally best when cutting at
high speeds. By way of an illustration, if one consid
-