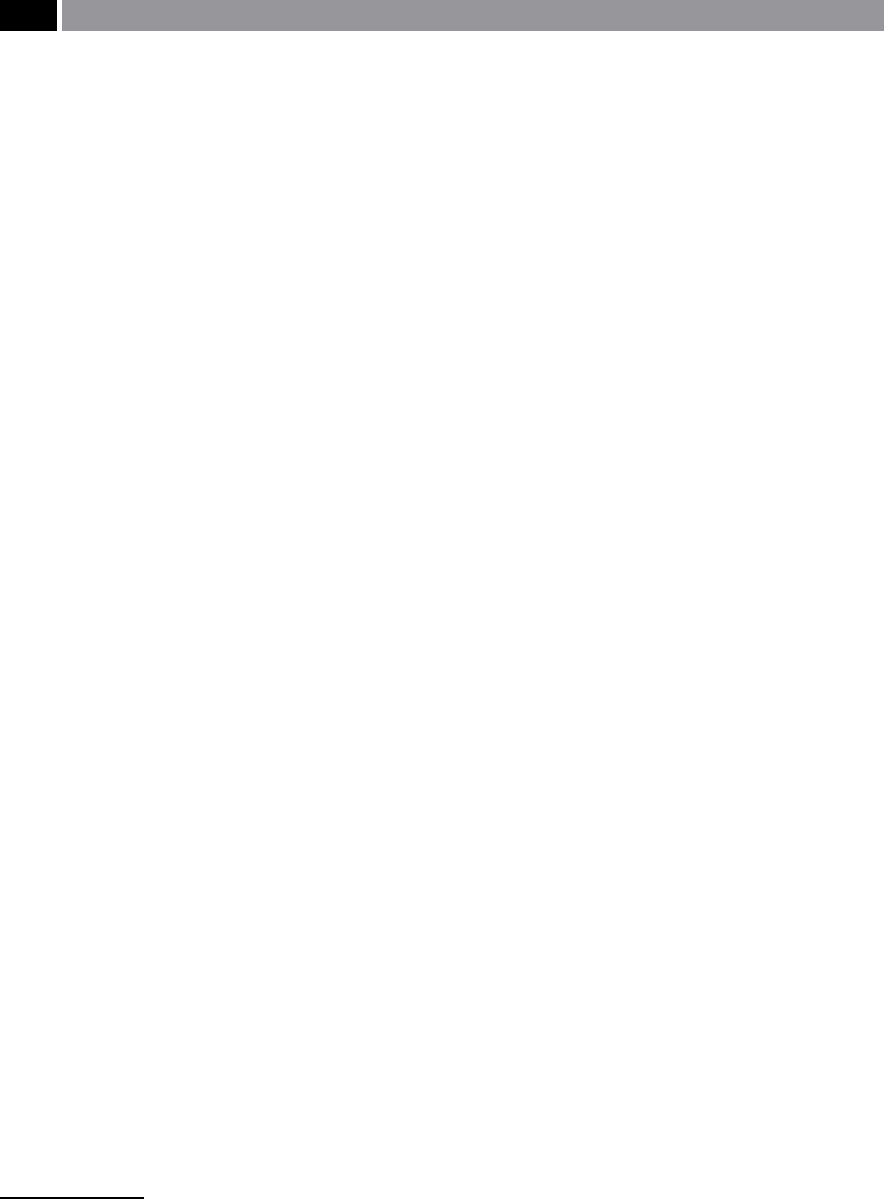
Many other skin conditions can occur and their
causes can emanate from a number of MWF sources
– going beyond the current scope and objectives of
this chapter. Although through the application of bar
-
r
ier and conditioning creams, together with clean and
suitable protective clothing, coupled to good washing
facilities, these factors will inevitably lessen the pos
-
s
ibility of allergic reactions and skin disorders.
Tumours and Cancerous Effects
However, less well known than the allergic and skin
condition previously mentioned, are the other more
serious debilitating health eects on the machine tool
personnel exposed to MWF’s. Industrial experience
suggests that continuous and long exposure to certain
mineral
o
ils can give rise to skin thickening, known as
keratosis, whereby ‘warty-elevations’ (i.e. see Fig. 211b)
can slowly develop over a period of some years. Hence,
these warts will either: remain as they are; disappear;
or in the worse case scenario, become malignant.
A considerable volume of research in both the
chemical and biological elds has been undertaken,
in particular, into the eects of mineral oils in cut
-
t
ing uids and their aect on worker’s health. Mineral
oils may contain carcinogens – chemical compounds
which are active in causing cancer, with currently, a
number of these compounds having been identied.
ey
o
ccur in the main, as polycyclic aromatic hydro-
carbons and, when present in modern rened mineral
oils exist in extremely small proportions – making their
‘positive’ chemical identication exceedingly dicult
to dene. Oil renement by acid treatment has now
been replaced by more modern rening techniques,
including solvent-rened treatment and hydrogenera
-
t
ion – greatly reducing the undesirable proportions
of aromatic compounds (i.e. these latter compounds
being potential carcinogens)
33
. Moreover, chemical
coolants were originally based on diethanolamine
and sodium nitrate, which for some time have been
suspected of forming ethanolnitrosamine – another
suspected carcinogen. In order to remove this pos
-
s
ible carcinogen, in
1
984, cutting uid manufacturers
removed the nitrates from their formulations. Finally,
33 ‘N-nitrosamines’ , and its chemical compounds are a signi-
cant danger to worker’s health and, the American Environ-
mental Protection Agency (EPA), stated in a report of their
ndings in 1974, that: ‘As a family of carcinogens, the nitrosa-
mines have no equal.’
if one considers permissible exposure levels (PEL’s)
from nitrosamine sources. en, it has been stated that
smoking t
wenty (untipped) cigarettes per day will de-
liver 0.8 micrograms o
f various nitrosamines which al-
most equates t
o eating a kilogram of fatty bacon per day
(i.e. 6 microgrames), thus, when undertaking these
seriously debilitating smoking/eating toxicity habits
over a signicant period of time, they would consider
-
a
bly increase the risk of cancer.
Cutting Fluid Mists
Mists resulting from machining operations and their
subsequent collection resulting from the application of
cutting uids, are usually given a low priority by most
manufacturers when compiling a list of potential capi
-
t
al items for the workshop. To press this point still fur-
t
her, many companies would much sooner purchase a
new machine tool, than install a special-purpose air
cleaner. In the automotive industries interest in the
level of air quality has some degree of importance,
while elsewhere in smaller production workshops it is
somewhat of a hit-or-miss aair. Given the potential
worker health risks involved today, with high-speed
machining (HSM) coupled to increased tooling cut
-
t
ing data and
h
igher-pressure coolant supplies (i.e.
see Fig. 195 – top), possibly the greatest threat posed
to a worker is from atomised mists (i.e. sub-
µm s
ize)
within the local atmosphere. Many companies that
incorporate mist collection ltering, will only remove
particles of >4
µm i
n size, leaving the critical sub-µm
particles still present in the atmosphere.
e earliest chemical interventions to reduce mist-
i
ng were high-molecular-weight polymer additives,
that act to stabilise MWF’s and thus suppress mist for-
m
ation. With conventional petroleum-based uids,
polyisobutylene has been the preferred anti-mist ad-
d
itive. While, for aqueous-based cutting uids, poly-
e
thylene oxide (PEO) has been utilised. Due to the
susceptibility of PEO’s to shear degradation, repeti-
t
ive additions of the PEO polymer are needed to main-
t
ain mist reduction. Today, a newer class of shear-
stable polymers has been developed to overcome the
shear degradation as indicated by PEO’s. ese latest
polymer products have been derived from complex:
2-acrylamido-2methlypropane sulphonic acid mono
-
m
ers, hence, providing longer-term performance in
continuously recirculating aqueous-based MWF sys-
t
ems.
So, very high concentration cutting uid mists will
over a short period of time cause: ‘smarting’ of the
eyes; irritation of exposed skin; result in slight irrita
-