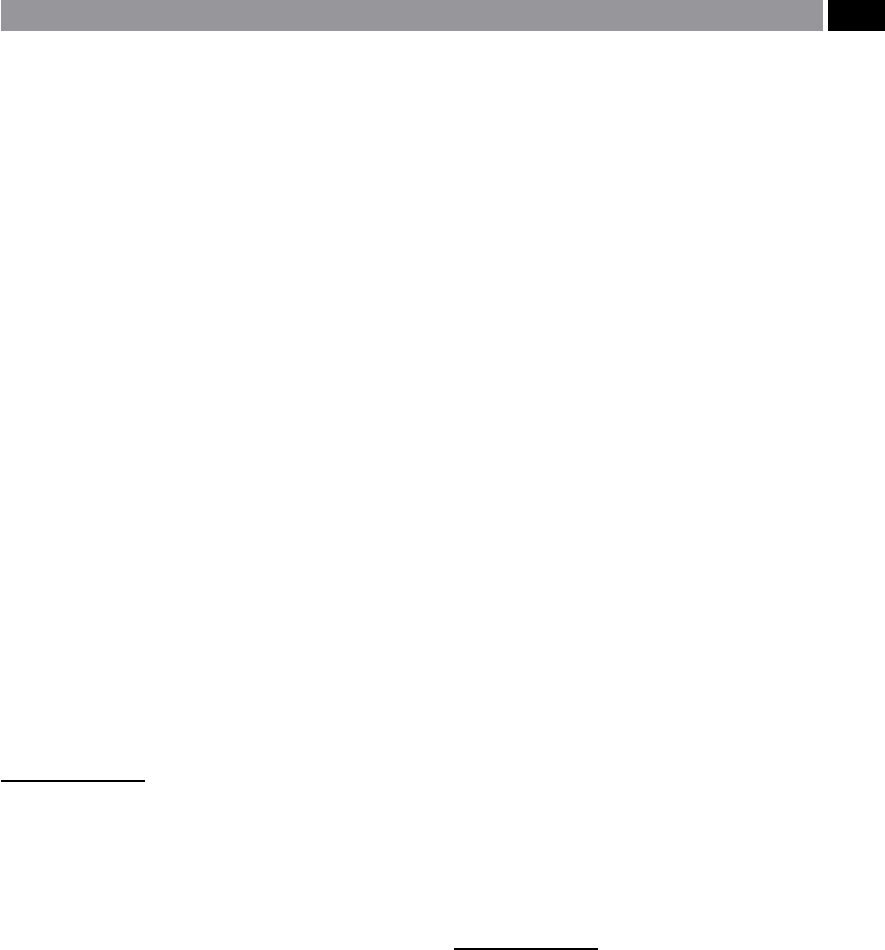
face – as it moves to various points on the workpiece’s
geometry. e tooling is held here and in eect, is a
cantilevered beam (i.e. the tool is normally only sup-
ported at one end only). In this situation the tooling
assembly can be equated to that of boring tooling, then
its inherent rigidity will decrease by the cube of the
stand-o distance from the ‘gauge line’
18
. When a ma-
chine tool builder calibrates this orthogonal-designed
machine tool, they will measure along the base of the
column – either optically (i.e. by for example, autocol-
limation
19
instrumentation), or with laser interferom-
etry, thus feeding-back any potential error sources for
CNC’s dynamic compensation, during execution of
the part program. Nonetheless, the column can either
minutely: twist; bend; or even move; if its temperature
varies by only just a few °C. In fact, it has been widely
reported that up to 70% of the total errors present on a
machine tool are thermally-related.
On conventional machine tools – with slideways,
essentially one does not really know what is occur-
ring in all of the degrees of freedom at any particu-
lar time. Although even if we did know the dynamic
status, unless some form of ‘adaptive compensation
s
ystem’
20
was tted to the machine, having some so-
phisticated multiple sensors positioned on and within
critical positions on the machine’s structure, then oth-
erwise, it would be almost impossible to compensate
18 ‘Gauge line’ of the tool, is the distance from where its eective
length is taken, specically when the tool length compensa-
tion distance is needed for the CNC programming details.
Normally, this ‘gauge line’ is datumed from a known point on
the male spindle taper, located in, and standing slightly proud
of its female counterpart. is measurement is either prefer-
ably set in a tool presetting machine, or it can be obtained on
the machine tool by some form of table-mounted touch-trig-
ger cube. Alternatively, the tool’s length can also be accurately
measured by some form of laser-activated instrumentation,
strategically-positioned at a suitable part of the machine tool’s
structure – where it will not interfere with any subsequent
machining operations.
19 ‘Autocollimation’ was the ‘traditional’ technique that was em-
ployed for any form of machine tool calibration. Autocollima-
tion instruments and equipment, utilise highly-evolved ac-
curate and precision optical apparatus to measure alignments
and squarenesses of the machine tool’s axes, which can then
be utilised to compensate for any error sources detected in the
machine tool’s kinematics. [Sources: Taylor Hobson, 1984/
Spectrum Metrology, Leicester (UK)]
20
‘Adaptive error compensation’ , basically utilises sophisticated
geometric algorithms that allow for compensation of the geo-
metrical elements, via a range of strategically-positioned sen-
sors on orthogonal machine tools. (Source: Ford, 1993)
for such error sources – as they occur. Clearly then, it
is no coincidence that both the ‘Variax’ operates with
six legs and, it also has six degrees of freedom. ese
leg orientations have three pairs of two legs that cross
each other and which are secured, but free to swivel
at either end (i.e. see the simulated renditions in Fig.
223 and partial assembly of an actual ‘Variax’ machine
tool in Fig. 224). With these six legs, all of the degrees
of freedom are controlled, which in turn, eradicates
the usual sources of errors exhibited by conventional
multiple and ‘stacked’ slideway axes. Some of the ma-
j
or benets obtained from the ‘Variax’s’ design congu-
ration are:
•
Extremely rigid machine tool – coupled to small
mass making it 500% more rigid than a conven-
tional machine, due to the fact that all forces
whether they are in compression, or tension are fed
through the six legs and its associated space frame,
•
Exceedingly fast in operation – as all the ballscrews
must move together, they only have a light mass to
contend with, making it up to 5 times faster than an
orthogonal machine tool,
•
Very high continuous thrust – due to concurrent
and synchronised use of the six ballscrews,
•
High accuracy and precision – this is due to the
machine’s inherent rigidity, coupled to the fact that
all six degrees of freedom are controlled, with laser
feedback through the centre of the ballscrews
21
,
•
No supporting structure – the ‘Variax’ is self-con-
tained, so it does not need foundations. e ma-
chine has a three-point location and the weight
of the spindle head is neutralised, as far as the
ballscews are concerned – by the three large gas-
spring supports
22
(i.e. see Figs. 224 and 225a).
21 ‘Laser-controlled feedback’ , through the centre of the
ballscrews, negates the Abbé oeset error, with any errors in
the legs (i.e. axes) being averaged, rather than ‘stacked-up’ as
is the situation in conventional machine tools. Hence, volu-
metric accuracies are in line with that of a Co-ordinate Meas-
uring Machine CMM – see details in Fig. 223a.
22 ‘Gas-spring supports’ ,
are tted outside the actuator platform
(i.e. see Figs. 224 and 225a), they are strategically positioned
so that they carry actuator platform’s gravity-induced
load. us, these gas-spring support placements and their
operation, means that the actuators have to only overcome
inertia and momentum to move the machining head. is
has the kinematic benet of enabling the machine spindle to
move through space faster than any single actuator changes
its length, this combination allows the ‘Variax’ to move and
accelerate up to ve times faster than a conventional machine
tool.
Machining and Monitoring Strategies 453