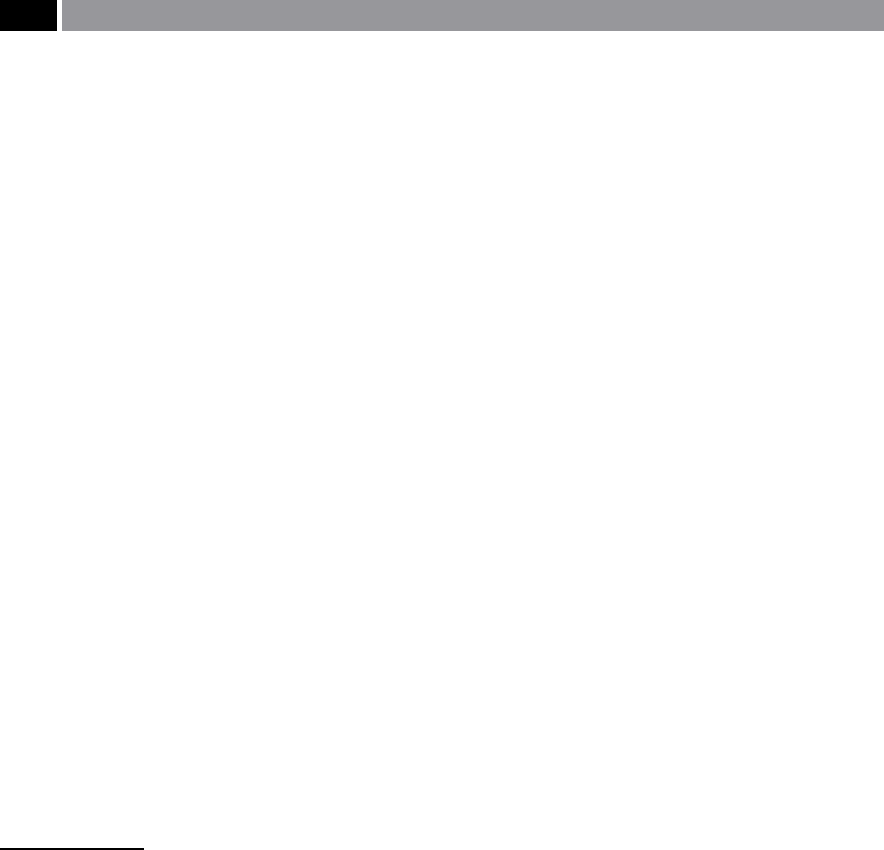
cranked-probe – with its calibration obtained from
the ‘reference measurement sphere’ being located on
the CMM’s table, utilised to inspect the φ1
0 mm hole
geometry and there respective co-ordinate positions.
is probe arrangement was swapped for a conven-
tional ‘touch-trigger probe assembly’ to measure the
machinable disk diameters – while holding the same
cartesian co-ordinate relationships as when it was
o
riginally UHM. Later – without ‘breaking-down’ ,
while still maintaining the same angular orientation,
this stereometric artefact assembly was inspected on a
roundness testing machine (Taylor Hobson: ‘Talyrond
265’) for individual disk parameters of roundness and
cylindricity
37
assessment – for the ‘three-disk relation-
ship’. e results of all of these ‘averaged’ roundness
measurements and Ballbar polar plots are graphically
depicted as histograms in Fig. 243c.
When a comparison is made of these results from
three individual and completely diering inspec-
tion procedures, namely: Ballbar; CMM; and Taly-
rond, they show some degree of measurement con-
sistency individually, but less so when each disk data
is grouped. For example, in the case of the Ballbar, it
i
ndicated a 1 µm variation (i.e. range) from the top-to-
bottom disks, while having a mean value of 17.5 µm.
e Talyrond polar plots (i.e. ‘Least Squares Reference
C
ircle’
38
: departures from roundness) also produced
consistent roundness results, ranging from <4 µm,
having a mean value of ≈14 µm. Conversely, the larg-
est variability occurred with the CMM, producing a
37 ‘Cylindricity’ , can be dened as: ‘e minimum radial separation
of 2 cylinders, coaxial with the tted reference axis, which totally
enclose the measured data’. (Source: Taylor Hobson, 2003)
NB A ‘working denition for cylindricity’ , might be: ‘If a
perfectly at plate is inclined at a shallow angle and a parallel
cylindrical component is rolled down this plate. If it is a truly
round cylinder then as the component rolls, there should be
no discernible radial/longitudinal motion apparent’. (Sources:
Dagnall, 1996; Smith, 2002)
38 ‘Least Squares Reference Circle’ (LSC1), can be dened as: ‘A
line, or gure tted to any data such that the sum of the squares
of the departure of the data from that line, or gure is a mini-
mum’. is is also the line that divides the prole into equal
minimum areas
NB
is LSC1 is the most commonly used ‘Reference Circle’.
e ‘out-of-roundness’ , or ‘departures-from-roundness’ as it
is now known, is then expressed in terms of the maximum
departure of the prole from the LSC1 (i.e. the highest peak
to lowest valley – on the ‘polar plot’). (Source: Taylor Hobson,
2003)
range of 15 µm, with a mean value of ≈23 µm. Prior to
discussing why the CMM results signicantly varied
from those obtained by both the Ballbar and Talyrond,
it is worth visually looking at a comparison between
the general proled shapes of typical ‘polar plots’ pro-
duced by both these techniques. In Fig. 242a, a rep-
resentative ‘polar plot’ from a Ballbar is shown and,
likewise in Fig. 242c, one from a Talyrond is depicted.
eir respective proled shape geometry in terms of
harmonics, is remarkably alike, illustrating the same
generally similar lobed-shape combined with its iden-
tical angular orientation.
Returning to the CMM results, only a few data
points are utilised to obtain a measured diameter,
while with the Ballbar and Talyrond alike, they liter-
ally take thousands of data points to obtain the polar
plotted proles. If, when the CMM touches each of
the machinable disk’s prole with the ‘touch-trigger
p
robe’ , this co-ordinate’s data could have been ob-
tained at the extremes of the elliptical shape, namely,
at its major and minor diameters, this may account for
such a variation in both the range and discrepancies,
when compared to the data obtained by the Ballbar
and Talyrond.
e four φ1
0 mm holes in each disk that were pro-
duced by HSM utilising circular interpolation at their
respective quadrant positions (Figs. 241 and 242b), are
given in the form of tabulated data in Table 16 – in
terms of their positional accuracy and radial change,
from their theoretical centres. From this φ1
0 mm hole
data, then the radial change for each disk, from the
t
op, middle and bottom disks, was: 46 µm: 45 µm: and
42 µm: respectively, giving a positional uncertainty
across these disks of 4 µm.
Conversely, if the dierence is considered for the
three stacked disks with respect to their angular rela-
tionships to each other, at: 0°; 90°; 180°; 270°; then their
a
ngular positional changes are: 46 µm; 26 µm; 32 µm;
and 49 µm; giving a positional uncertainty of 23 µm.
is positional uncertainty is still relatively small con-
sidering that in this case, each hole’s position is on a
dierent Z-axis plane – spanning 200mm in height.
Although if one considers the ‘Grand mean’ for both
cases then they have a positional uncertainty of just
1 µ
m, which for a machine tool that at this time was
around three years old is quite exceptional – having by
now, undertaken considerable industrial machinabil-
ity trials for the automotive and aerospace industries,
but admittedly, this vertical machining centre had pre-
viously been both Laser- and Ballbar-diagnostically
corrected – showing the ‘true’ relevance of calibration
to resolve and reduce any ‘errors’!