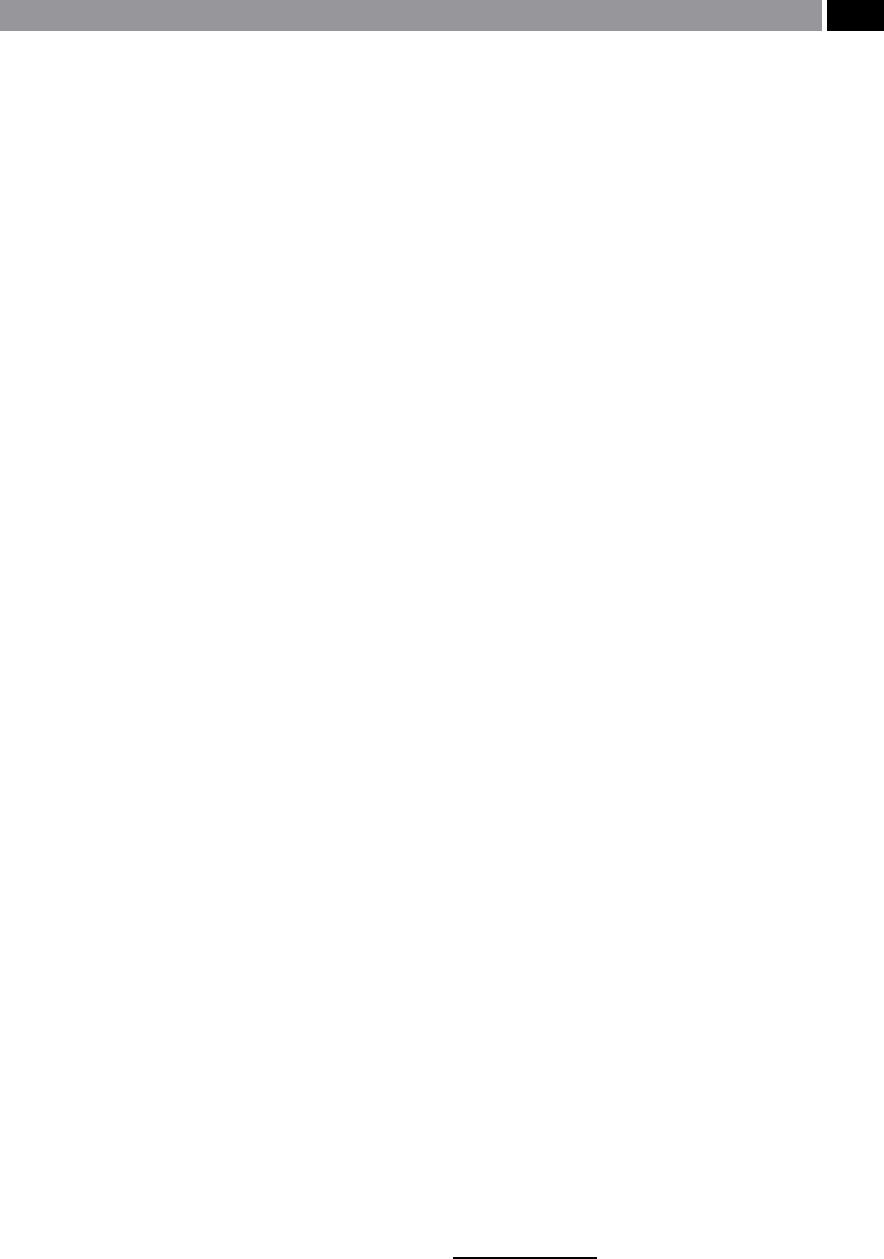
When applying ‘NURBS’ to a complex part’s curva-
ture, it is important to recognise that it denes the entire
curve, not just a series of facets, enabling it to express
any curve geometry, utilising less data than for other
‘curve-tting techniques’. Data transmission times are
signicantly improved as a result, this is because one
does not have to transfer all of the curve data, just the:
control points; the order of the polynomial; the knot
vector; and its weighting; as dened by the CAD sys-
tem. Once this has been achieved, the machine tool’s
CNC controller then decodes this information, in or-
der to control its servos. While a single ‘NURBS’ ex-
pression can describe a simple curve, complex curves
(e.g. Fig. 248c) are described by moving ‘weighting’ on
the control points, running the calculation, then mov-
ing the ‘weighting’ again and re-calculating and so on,
in a recursive manner. us, each point moved has
an inuence on the others, but the more the control
points utilised, the less their inuence becomes – in a
similar manner to the so-called: ‘law of diminishing
returns’. ‘NURBS’ is comparable to linear interpolation
in that the greater the accuracy the more the number
of points needed, although it requires less data in to-
tal – with a gure of 60% data-reduction, with an as-
sociated 40% improvement in time, has been claimed.
Although the solution to virtually every curve-tting
g
eometry can be undertaken by ‘NURBS’ , it cannot
partake in all ‘surface-describing miracles’. If the CAD
system outputs poor data, this will end up with a simi-
l
arly pitiable ‘curve-tting routine’ , so as the old saying
goes, it’s the equivalent of: ‘Garbage in, garbage out!’ In
time, these ‘NURBS’ will have even more renements
added to enhance the already powerful ‘curve-tting
processes’.
9.8.4 Sculptured Surface Machining –
Cutter Simulation
Once the free-owing curves for the sculptured sur-
faces have been generated and the actual workpiece
is about to be machined, many companies embark on
a ‘cutter simulation routine’ prior to undertaking any
surface machining. Many of the sophisticated surface
machining soware packages, can provide several
variations of complex surface machining routines.
Typical of such routines, is that shown for a particular
leading company’s product for the multi-axis sequen-
tial machining, depicted in Fig. 249a. is specic
‘sequential surface machining’ routine (Fig. 249a), is
an interactive, graphic implementation of ‘drive-part-
check’ surface machining, as dened in the: Automati-
cally Programmed Tool (APT) Standard. is routine
is greatly enhanced when utilised in combination with
two other machining soware packages, namely: ‘Se-
quential machining’; and ‘Drive curve mill’. While an
enhanced function incorporated into the machining
package is termed ‘looping’ ,
which enables the user to
generate multiple passes on a surface, by dening the
inner and outer tool paths, allowing the system to then
generate the intermediate stock-clearance tool path
steps.
A typical modular-package might oer: surface con-
touring; parameter line machining; rough-to-depth;
and zig-zag tool paths; having any design modica-
tions, or changes being automatically handled through
what is termed ‘associativity’ ,
thereby signicantly re-
ducing any attendant costly, but otherwise necessary
prove-outs. By utilising cutter simulation, parameters
such as: feedrate; spindle speed; and part clearance; are
instantly accessible and, being ‘modal’ they remain un-
changed, unless the user modies these values. While
at any time during the development of the simulation,
a user can test a setting by generating a tool path with
its accompanying high-resolution graphic display (Fig.
249a). Surface machining will automatically simulate
the cutter’s tool path, being displayed on a graphics
screen and generate textural output into a ‘cutter lo-
cation source le’ (CLSF). Aer simulation, the user
may either choose to accept the tool path simulation
and then save these parameters, or reject it and modify
whatever parameters are necessary to correct for any
attendant problems encountered. It should be stated
that if a problem had occurred when actually cutting
the complex geometric component’s surface – such as
‘
surface gouging’
50
, this would have probably scrapped
the otherwise expensive stock of workpiece material,
that has also added signicant value to it, by the time-
consuming process of machining this part’s intrinsic
geometric characteristics.
So the application of cutter simulation is not only
economic and scally important, it oers many other
signicant production benets. erefore, with such
enhanced cutter simulation, a range of important fea-
tu
res can be addressed ‘o-line’ , such as:
•
Supporting typical CAD ‘Surfaces and Solids’ pack-
ages,
•
Providing both 3- and 5-axis contouring motion –
including tool orientations that may be oset from
50 ‘Surface gouging’ , is if a cutter unintentionally removes mater-
ial (gouges-out) a portion of surface.
Machining and Monitoring Strategies 505