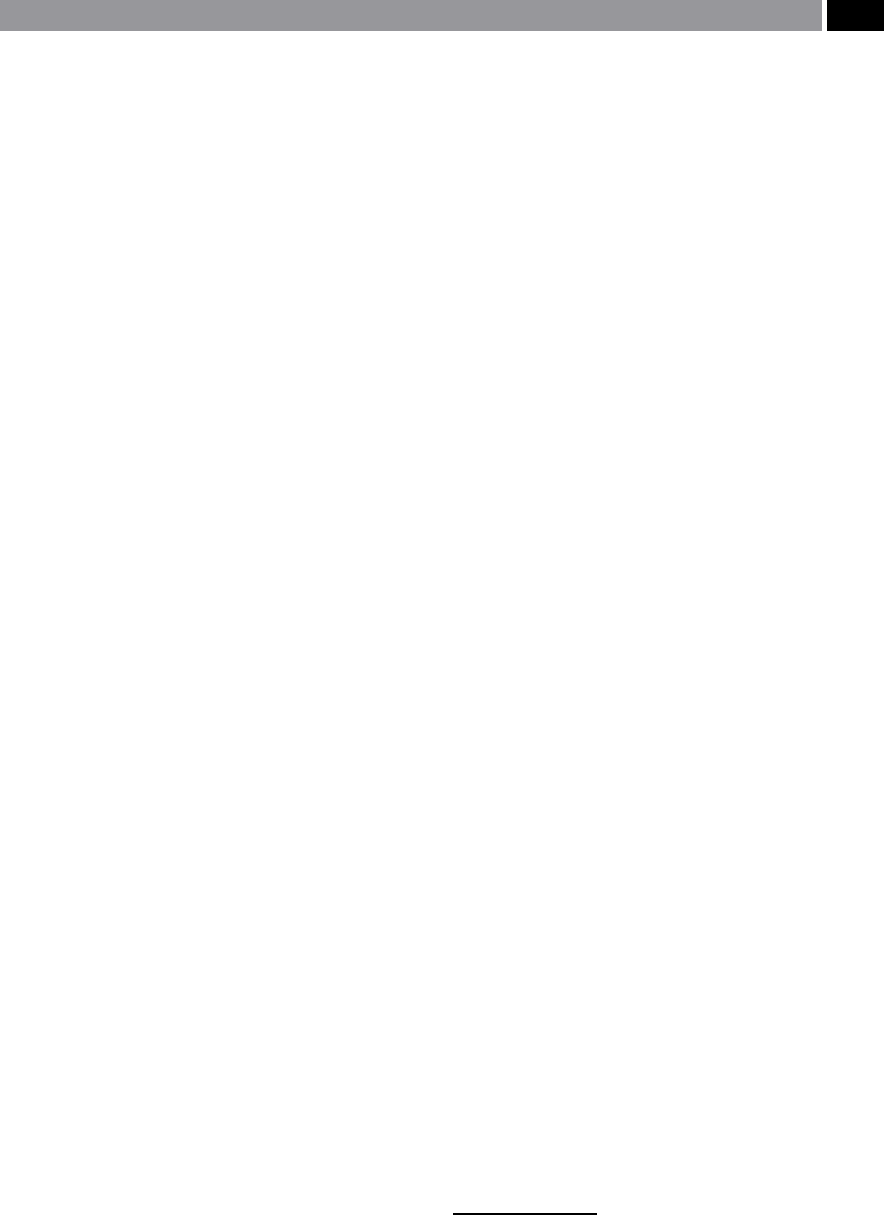
tool, giving a superb pay-back on the original invest-
ment, when one considers the major benets listed
above.
Machine Tool Optimisation
If a company has signicant numbers of CNC machine
tools in their manufacturing facility, then it may not
be feasible to introduce an ‘adaptive control’ system
across all of these machines – despite the positive
merits described above, simply on nancial grounds
a
lone. Under such circumstances, perhaps a ‘soware-
approach’ by simulating the cutting operations to the
problem of machining optimisation, may be the way
forward? Some companies oer CNC programming
optimisation packages that are based upon literally
thousands of ‘man-hours’ of development and rene-
ment (i.e. Fig. 259b, shows a very sophisticated version
of such a tool verication and simulation system).
ese simulation systems are oen part of a larger: op-
timisation; verication and analysis product that can
be ‘tailored’ to suit a machining company’s product
range and manufacturing output. ese ‘knowledge-
based’ systems of the machining process, via previous
simulation, know the exact: D
OC
; width of cut; and
angle of cut (i.e. for cutter orientation, when prol-
ing); for the machining process under consideration.
Further, the system also knows how much material
is to be removed by each cutting edge, as such, the
system also has information on the tooling available
from the magazine, therefore it selects correct tool and
assigns to it the optimum feedrate. Moreover, once
this information has been established for the new tool,
it outputs the tool path – which was identical to say,
that of the original tool, but now having signicantly
improved feedrates, although the system does not alter
its trajectory.
While setting up the system, it is usual for such
soware (Fig. 259b) to prompt the user for cutter set-
tings as the part simulation occurs, by in essence, add-
ing the user’s intelligence to that of the cutter’s opera-
tion. With these systems it is usual to have all cutter
settings stored in an optimisation library, thus the user
only has to dene the setting once. While, the more
sophisticated systems nd the maximum volume re-
moval rate and chip thickness for each tool, then it
employs them to determine the optimisation settings
for that tool.
In optimised roughing-out, the objective here is ob-
viously to remove as much stock material as possible
in the fastest time. Conversely, for nish-machining,
chip-loads may vary considerably, as the tool proles
through the workpiece material that was le behind
during previous roughing cuts over the contours
– to near-net shape. By optimising the tool’s path, the
soware adjusts the feedrates to maintain a constant
chip-load
78
(Fig. 259b). is cutter optimisation will
improve the tool life and give an enhanced machined
surface nish to the component. is fact is especially
c
ritical when ‘tip-cutting’ , with either a ball-nosed end
mill (Fig. 247b), or contouring over a surface with a
small step-over, such as when semi-nishing, or n-
ishing a steel mould cavity (Fig. 249b).
Summarising the advantages of utilising a simu-
lated optimisation cutter-path soware package, such
as the one in Fig. 259b which only illustrates some ba-
sic and simple tool paths. us, cutter-path optimisa-
tion oers the user the ability to:
•
Machine more eciently – cutting more parts in
the same amount of time, by signicantly reducing
the machined component’s cycle-time,
•
Reducing part cost thereby saving money – increas-
ing productivity by reducing the time it takes to cut
parts, will become a signicant saving per annum,
•
Improving part quality – by minimising the con-
stant cutting pressure, thus reducing cutter deec-
tion, with nished corners, edges and blend areas,
needing less subsequent hand-nishing,
•
Cutter life improved – because of optimised cut-
ting conditions are used, which prolongs tool life.
Moreover, with shorter in-cut time, this results in
less tool wear, also having the benet of reducing
down-time to change inserts, or tooling,
•
Reduction in machine tool wear – as a more con-
stant cutting pressure between the machine tool
and the workpiece reduces variable forces on the
axis motors, giving smoother machine operation,
•
Utilises time available more eectively – allowing
machinists to operate several CNC machine tools,
or setup the following job, etc., as they do not have
to be constantly ready to reduce/increase the ma-
chine’s feedrate over-ride.
By investing in suitable simulation and optimisation
soware of the tool’s path, enables a company that is
currently involved in a considerable amount of ma-
78 ‘Constant chip-loads’ , are normally recommended by cutting
tool manufacturers, as they reduce the eect of ‘chip-thinning’
somewhat.
Machining and Monitoring Strategies 537